HS2 complete largest ever UK pour of carbon-reducing concrete at Euston site
Posted: 18 October 2022 | Elliot Robinson (Editorial Assistant - Global Railway Review) | No comments yet
Construction at HS2’s Euston station has seen the use of innovative, green ‘Earth Friendly Concrete’ which saves 76 tonnes of CO2.
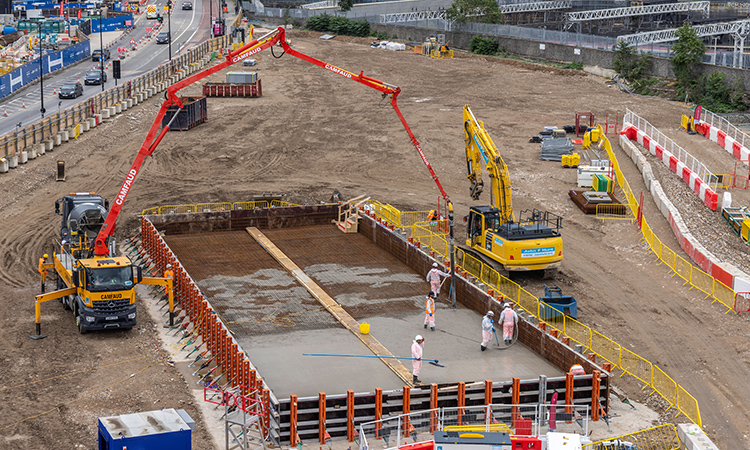
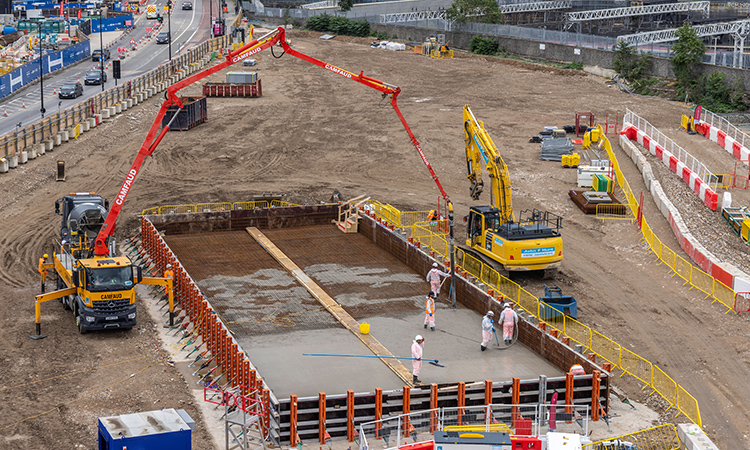
Credit: HS2
The construction of HS2’s new Euston station has undertaken the largest ever UK pour of Earth Friendly Concrete (EFC), a material that reduces the amount of carbon embedded into the concrete, saving over 76 tonnes of CO2 overall. John F Hunt, working for HS2’s station Construction Partner, Mace Dragados Joint Venture (MDJV), completed the 232 m3 concrete pour in early September. A time-lapse of the pour can be found at the bottom of the page.
‘Earth Friendly Concrete’
The EFC product, supplied by Capital Concrete, has been used as a foundation slab that will support polymer silos used for future piling works at the north of the Euston station site. Whilst the foundation is temporary, it will be in use for two years, and historically would have been constructed with a more traditional cement-based concrete.
The use of the product on this scale is an important step forward in how new, innovative environmentally sustainable products can be used in construction. It also helps support HS2’s objective of net-zero construction by 2035 and achieve its goal of halving the amount of carbon in the construction of Britain’s new high speed rail line.
Related news you will enjoy:
Businesses across the UK encouraged to become HS2 supplier
HS2 launch the first of six giant London tunnelling machines
“HS2 is at the forefront of adopting new technologies to reduce the environmental impacts of construction and is on its way to achieving a 50 per cent reduction in carbon emissions compared to traditional construction methods,” Mark Fenton, Carbon Manager at HS2 Ltd, said. “Whilst there have been a lot of examples of using low carbon concrete across the project, the scale of its use at Euston station is a huge step forward in us understanding how it can be used more widely in construction going forward, reducing environmental impact for generations to come.”
Earth Friendly Concrete is made from a combination of ground granulated blast furnace slag, pulverised fly ash and a high-alkaline chemical, rather than Portland cement. Its geopolymer binder system reduces embodied carbon by around 70 per cent saving 250kg of CO2 per cubic metre poured.
Lowering emissions
“This largest ever UK pour of earth friendly concrete is symbolic of the ambition we have at Euston to get our carbon emissions down at every possible opportunity,” Ben Wheeldon, Programme Director for Mace Dragados Joint Venture, said. “This project is a hotbed for innovation, not just in the decarbonisation space, but generally, and we’re making sure of that by bringing on board the right supply chain partners and encouraging them to be bold with their solutions.”
‘Our ambition is to reduce carbon emissions during construction at every possible opportunity,” Martin Needham, Senior Project Manager for John F Hunt, said. “The pour to create the temporary slab at Euston was the perfect opportunity to utilise the cement free, Earth Friendly Concrete. We chose to use the EFC, not only for the over 70 per cent saving in embodied carbon, but also for its excellent characteristics. It has an increased tensile strength, enabling thinner slab designs and therefore a reduction in overall volume of both concrete and reinforcement.”
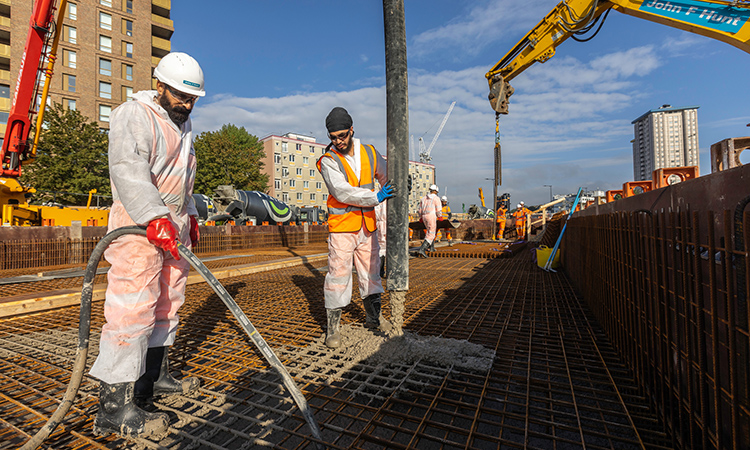
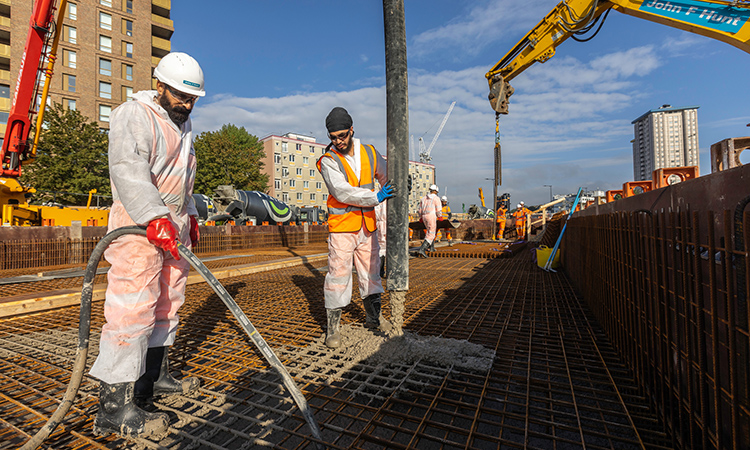
Credit: HS2
In addition to the application of EFC, innovative thinking and collaboration saw the use of 20-yard skips instead of the standard concrete thrust blocks for the temporary works design during the process to remove a retaining wall. This alone resulted in a saving of 30 tonnes of CO2. John F Hunt also used GreenD+ Hydrogenated Vegetable Oil (HVO) for all site vehicles instead of diesel, saving around 29 tonnes of CO2.
Elsewhere on the Euston site, the HS2 and MDJV team have adopted a number of measures aimed at reducing the environmental impact of construction, including the use of liquefied petroleum gas generators as a direct replacement for diesel generators, and using a new piling method that will provide heating for buildings above.
The time-lapse of the pour is below.
Related topics
High Speed Two (HS2), Infrastructure Developments, Station Developments, Sustainability/Decarbonisation, Technology & Software
Related organisations
HS2 Ltd (High Speed Two), John F Hunt, Mace Dragados JV (MDJV)