An alternative overhead system: the Rigid Overhead Conductor-rail System
Posted: 27 November 2019 | Ankur Saxena | No comments yet
A Rigid Overhead Conductor-rail System (ROCS) can be used at stations for improved electrical clearances and has several advantages over conventional tensioned overhead equipment (OHE). Ankur Saxena, Engineering Manager at Furrer+Frey, explores further.
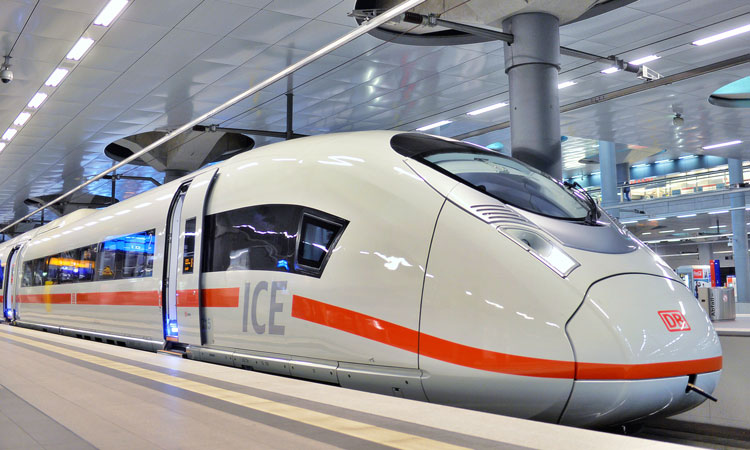
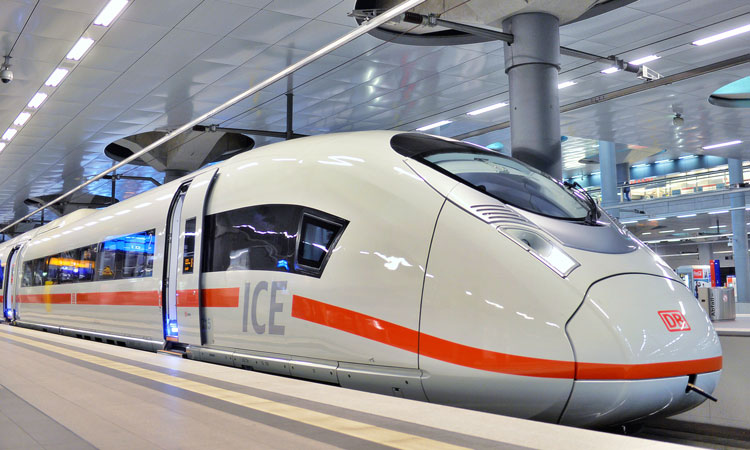
The costs of the recent UK mainline electrification projects have attracted much adverse publicity, resulting in delays to projects and the cancellation of future electrification projects. A look at the way electrification infrastructure projects spent their budgets shows that a major chunk of overall cost was associated with achieving 25kV electrification on the existing Victorian infrastructure. A lot of stations, bridges and tunnels cannot achieve compliant electrical clearances required for a 25kV electrification system as they were never designed to accommodate electrified stock in the first place.
In all recent electrification projects, be it the Edinburgh Glasgow Improvement Programme (EGIP) in Scotland or the Great Western (GW) electrification project in England and Wales; designers and delivery partners faced great challenges in delivering a 25kV overhead system that respects the required electrical clearances from existing infrastructure.
This was not an easy problem to solve, as designers either have to go for an expensive, bespoke arrangement to maintain the clearances or go for derogation i.e. permit smaller clearances where justified by a CSM RA compliant risk assessment (in accordance with Railway Group Standard GL/RT1210 AC Energy Subsystem and Interfaces to Rolling Stock Subsystem which contains the UK national technical rules mandated by ENE TSI).
The costs of the recent UK mainline electrification projects have attracted much adverse publicity, resulting in delays to projects and the cancellation of future electrification projects. A look at the way electrification infrastructure projects spent their budgets shows that a major chunk of overall cost was associated with achieving 25kV electrification on the existing Victorian infrastructure. A lot of stations, bridges and tunnels cannot achieve compliant electrical clearances required for a 25kV electrification system as they were never designed to accommodate electrified stock in the first place.
In all recent electrification projects, be it the Edinburgh Glasgow Improvement Programme (EGIP) in Scotland or the Great Western (GW) electrification project in England and Wales; designers and delivery partners faced great challenges in delivering a 25kV overhead system that respects the required electrical clearances from existing infrastructure.
This was not an easy problem to solve, as designers either have to go for an expensive, bespoke arrangement to maintain the clearances or go for derogation i.e. permit smaller clearances where justified by a CSM RA compliant risk assessment (in accordance with Railway Group Standard GL/RT1210 AC Energy Subsystem and Interfaces to Rolling Stock Subsystem which contains the UK national technical rules mandated by ENE TSI).
ROCS vs OHE
An alternative type of overhead system – the Rigid Overhead Conductor-rail System (ROCS) – has a number of advantages over conventional tensioned overhead equipment (OHE) for application in specific station areas.
A conventional OHE has a copper contact wire suspended from a catenary wire with the help of a dropper. The result is that a conventional system requires substantial space above the train. The contact wire has a typical length of 1.5km and is kept under mechanical tension by tensioning equipment, which also accommodates the expansion and contraction of the contact wire caused by the temperature variations.
In contrast to a conventional OHE system, a ROCS is based on a rigid bar design and does not require mechanical tension. Due to the absence of mechanical tension, there is an extremely reduced likelihood of a de-wirement or snapping of the contact line. As there is no mechanical tension in the system, a ROCS does not require tensioning devices. This can free-up space from the platform which can now be used for the travelling public rather than for heavy structures supporting the tensioning equipment – for instance, a ROCS is light enough that it can be supported from canopy structures.
The rigid bar design also means that the catenary is not required anymore, thus requiring much less space above the train. The reduced cantilever and system size reduces the electrical footprint which helps to achieve improved electrical clearances as compared to conventional OHE.
The contact wire is staggered more gradually in a ROCS than in conventional OHE, and there is no push-off or pull-off configuration. The stagger is simply achieved by moving the conductor rail clamp in across-track direction on the cantilever arm to set the required stagger, also allowing for better clearances than a conventional OHE cantilever.
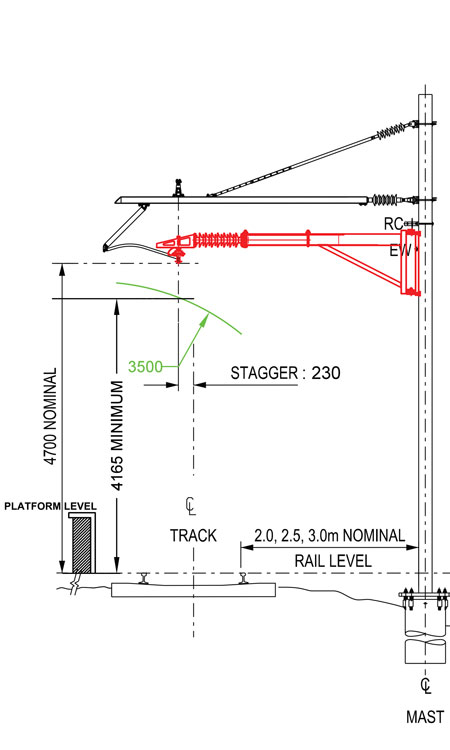
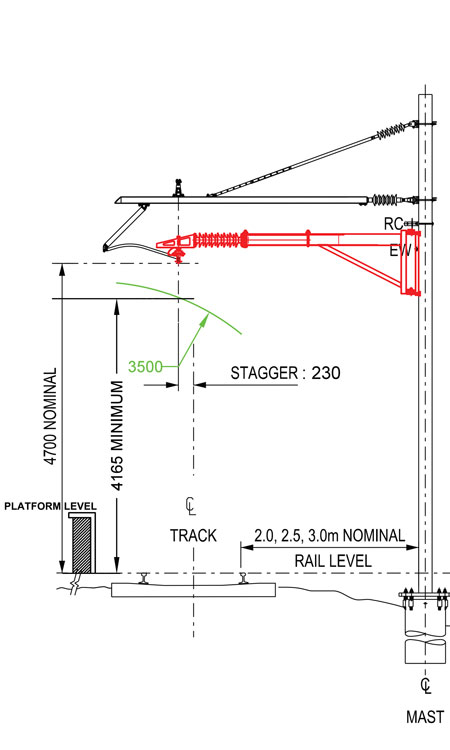
Figure 1
Figure 1 shows a conventional Master Series cantilever in black, a typical ROCS cantilever in red and electrical clearance in green (minimum required from nearest standing surface in public areas in accordance with BS EN 50122-1). What can be seen is the footprint of a ROCS cantilever that is substantially lower than the conventional cantilever.
The nominal contact wire height with a conventional OHE system is 4,700mm, which can be reduced to a minimum of 4,165mm subject to project approvals. The station platform infrastructure often limits the space available above the train to fit the overhead equipment. A nominal contact wire height would result in non-compliant electrical clearances to the station roof/canopy; whereas a low contact wire height compromises the safe electrical clearances from public standing surfaces – leaving the designers in a catch-22 situation.
The ROCS provides a perfect balance in such situations as it requires much less space above the train. Figure 2 shows a comparison between a conventional and a ROCS cantilever, both set at 4,315mm contact wire height and 230mm platform side stagger. The clearance of the ROCS cantilever from the platform edge is higher by almost 200mm when compared to the conventional cantilever. Delhi Metro has utilised a ROCS at elevated stations such as Ballabgarh along the Violet Line (Line 6), where the use of conventional OHE would have resulted in restricted clearances. The overhead conductor rail in station areas is directly integrated with conventional overhead contact line systems either side of the station.
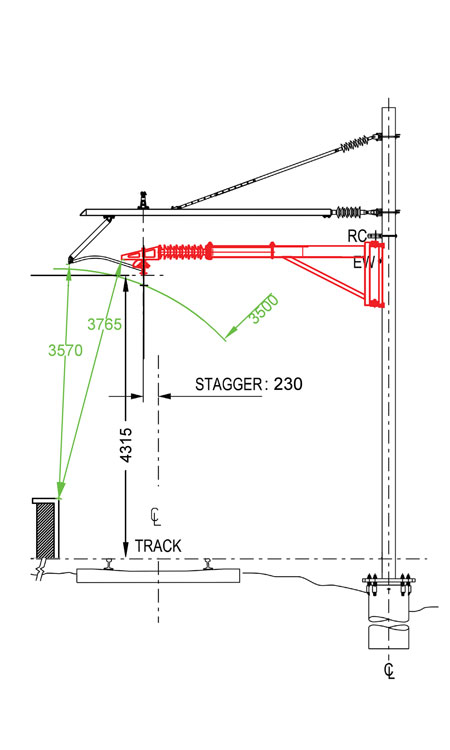
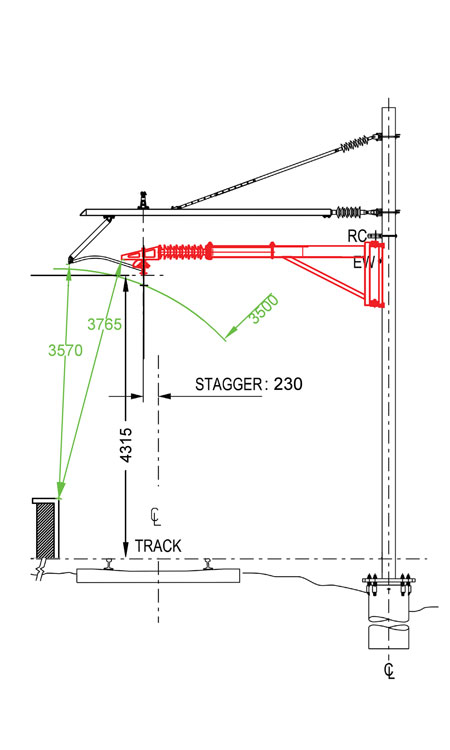
Figure 2
The ROCS allows contact wires to be staggered further from standing surface with the nearest live item being the conductor rail itself – no cantilever part or register arm is near the platform.
The ROCS mainly bears only its own weight; there are no additional mechanical tensile forces and hence requires lean structures. The ROCS installed at Salzburg Station in Austria use short, lean square hollow section masts with back-to-back cantilevers.
The system also has capability to adapt and seamlessly merge with station architecture and aesthetics. One such example would be Berlin Central Station, where a ROCS is supported from station columns and the cantilever design follows the cues from station structural design.
The system also allows installation using temporary structures while nearby structures/platform areas are under construction and renovation. It can later be switched on to permanent supports.
The ROCS can be installed utilising shorter possessions as the system allows modular construction, even including conductor rails, causing minimal disruption to operating services. These benefits of a ROCS, plus the fact that there is no contact wire uplift even if operated with multiple pantographs, make it an obvious solution for low bridges. With a ROCS, electrification under a low bridge can be achieved without carrying out bridge lifting works or compromising on performance and safety by reducing the contact wire height.
Issue
Related topics
Digitalisation, Electrification & Cabling, Infrastructure Developments