How to implement efficient railway maintenance through digitalisation
Posted: 16 April 2019 | | No comments yet
Ahead of Global Railway Review’s webinar in association with Alstom, which will explore how to implement efficient railway maintenance through digital solutions, we posed some questions to Christophe Sanguina, Market & Portfolio Director for Alstom Services.
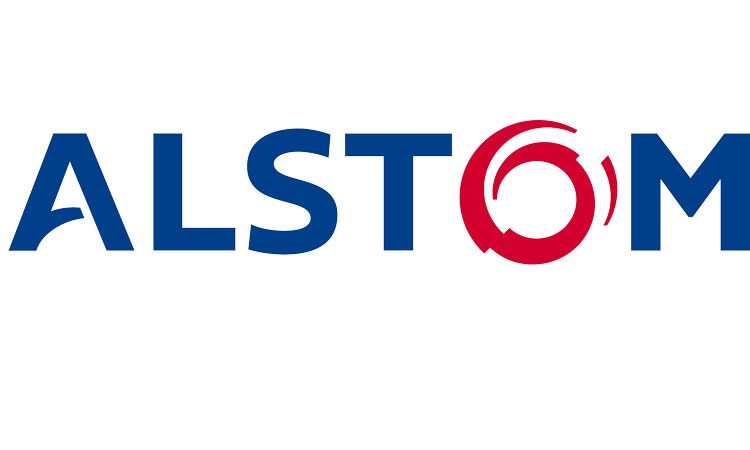
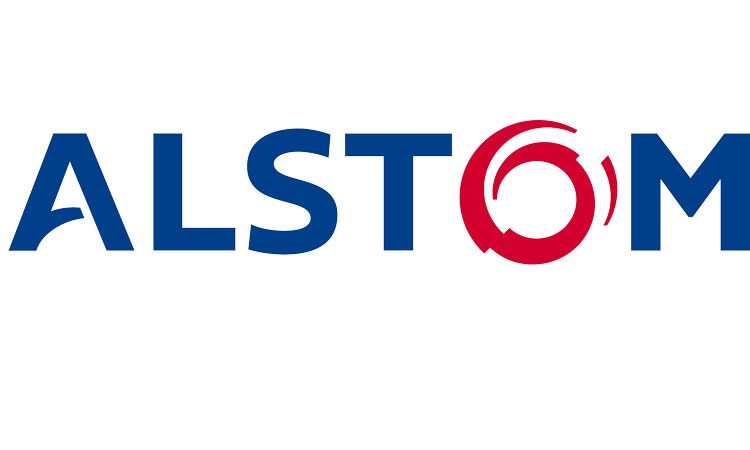
To what extent do you think digitalisation has changed maintenance activities in the railway sector?
Digitalisation allows us to collect and use data as never before. At Alstom, digital advances have allowed us to rethink maintenance from the ground up – including our business model – while helping us overcome the industry’s unchanging challenges; reducing costs, ensuring the reliability of processes and optimising the availability of trains. Thus, extensive digitalisation has become a necessary step in the modernisation of the railway industry.
There are many areas of application; spare parts and maintenance planning, obsolescence monitoring, prediction of failure, specific instructions and technical documentation, access to remote experts, e-learning, and much more. In every case, digitalisation raises efficiency in both daily activities and long-term planning.
Alstom’s HealthHubTM represents an innovative approach to condition-based and predictive maintenance for rolling stock, infrastructure and signalling. This integrated range of decision-support tools (sensors, cameras, lasers, dataloggers, etc.) continuously monitor the state of assets to prevent failures, questioning the standard execution of maintenance activities. Building on HealthHub’s success, Alstom now proposes Dynamic Maintenance Planning (DMP) – a new batch of solutions which allow a more responsive, flexible and fluid execution of maintenance tasks. DMP is the next phase of digitalisation in maintenance; turning collected data into action.
What are the main benefits of the Dynamic Maintenance Planning system?
DMP is best described as the culmination of a multi-phase programme stretching back over 20 years.
The first phase is concerned with being able to monitor our assets, which include infrastructure, rolling stock and signalling systems. Sensors, cameras, lasers, dataloggers and others continuously monitor the state of assets and identify changes in subsystem performance.
As a second phase, collected data must be transformed into ‘smart’ data. This involves algorithms capable of automatically identifying failures and sending alerts. Data is bundled and secured, then sent to a web platform able to predict the remaining useful life of the assets and to anticipate other failures before they occur. The ability to transmit and interpret this data is essential for system reliability.
As mentioned, DMP is the third phase, in which the deep wells of collected data are put into concrete action, ensuring maximum efficiency and effectiveness of day-to-day works. DMP is composed of 12 applications which interact together to allow truly intelligent maintenance. DMP, as its name would suggest, dynamically adapts during operation and at each step of the maintenance plan, building seamless interactions between operations and maintenance.
Its key benefits include automated information flow, visibility and traceability of activities, avoiding redundant or excessive maintenance, optimised operations and increased industrial execution efficiency.
What will be the key takeaways from the webinar?
The webinar will demonstrate how Alstom manages assets throughout their lifetimes, from manufacture to maintenance, providing a vantage point to observe and understand the behaviour of entire railway systems. Participants will learn how a railway expert approach leverages digitalisation and allows the selection of the most appropriate condition-based and predictive maintenance solutions. Most importantly, the webinar will illustrate how to make the leap from data to action – to move from (relatively) simple real-time asset monitoring to concrete maintenance actions for rolling stock, infrastructure or signalling systems.