Experiencing first-hand high-capacity, precision and reliability at Plasser & Theurer
Posted: 22 February 2019 | Johann Dumser - Plasser & Theurer | No comments yet
Efficiency and quality with a competitive edge can only be achieved if man and machine complement each other perfectly. Global Railway Review’s Commercial Director, Sam Pirani, and Junior Editor, Tara Nolan, witnessed this first-hand with an exclusive tour around Plasser & Theurer’s production site in Linz, which Tara details below…
One hour and 15 minutes onboard ÖBB’s comfortable Railjet service takes you from Vienna’s main station to the city of Linz, where lies the heart of Plasser & Theurer’s operations.
By centralising the warehouse structures, the track maintenance machine manufacturer has perfected the process of production and assembly. During our tour around the vast site, Johann Dumser, Director of Marketing and Communications highlighted some of Plasser & Theurer’s fundamental procedures.
Utilising automation
Robots and automated machines have had a place in Plasser & Theurer’s production since the early 90s: “Wherever possible we have automated the work processes,” said Johann. “This allows us to ensure continuous quality standards.”
Offering more detail on this, Johann identified the quick pace of developments in the Chinese markets and their ability to keep costs low. These pressures require Plasser & Theurer to “keep up with new technologies” if they are to compete.
Furthermore, automation and technological developments have enabled space to be saved across the site. Johann detailed: “The cutting shop has been automated, which means all material is delivered straight there and stored. The majority is stored in the automated high-bay warehouse that can hold up to 290 tonnes of steel in an area of approximately 70m2.”
However, Johann does not see a future where every stage will be automated. “We will always need the human mind”, he said, explaining that the robots have to be “programmed by experienced specialists” onsite in Linz.
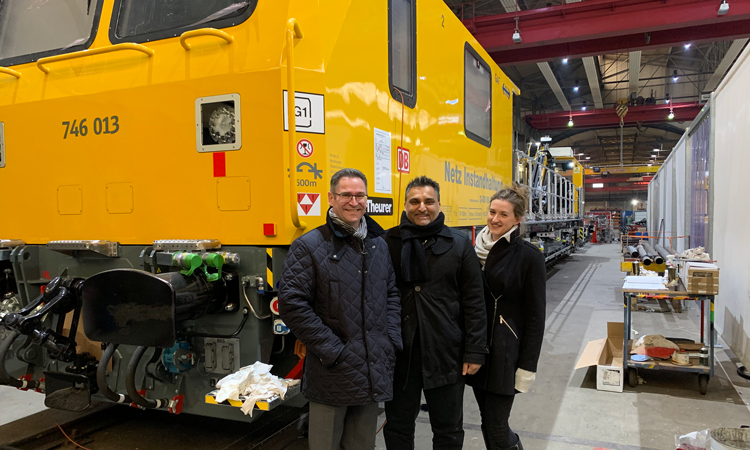
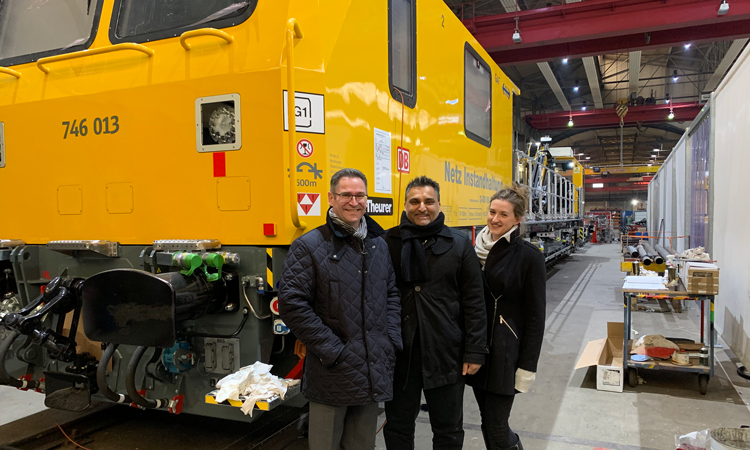
The Global Railway Review team with Johann Dumser
Sustainable production
Across 29 workshops, Plasser & Theurer manages the production of track maintenance machines seamlessly. Walking through each site – with the methodical whir of machinery and diligence – efficiency is witnessed in real time.
Of course, keeping production as sustainable as possible is a high priority. To ensure this, Johann named “the early detection of errors” as one of the most important measures in place; preventing the waste of materials, and time. This can happen thanks to the quality collaboration of the Design Department, Quality Management Department, Production Planning Department and Sales Department.
Throughout the individual areas of the plant there are “quality gates” which ensure high-quality information is available at the right time. Johann also mentioned how “clear responsibilities” play a crucial role in guaranteeing everyone is aware of their personal duties. Again, this helps reduce errors – and therefore waste – which in turn creates a more sustainable and efficient workplace.
Plasser & Theurer’s workforce
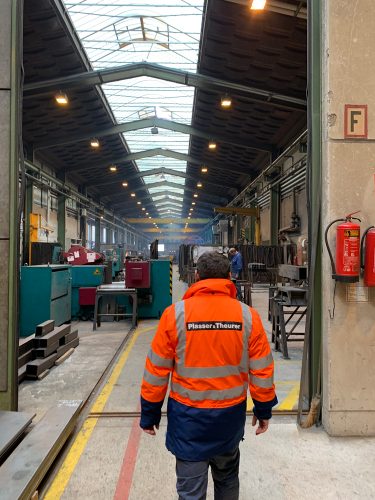
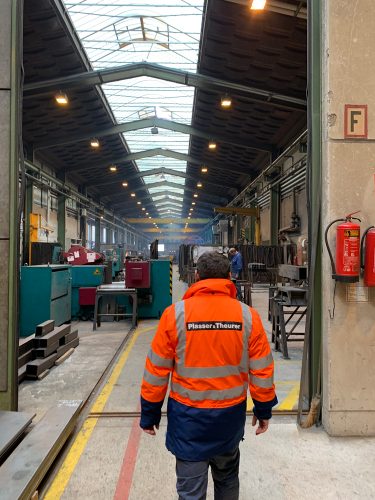
Markus Hackl, Trainer Service Center, leading the tour
Whilst exploring the site, it was clear that the workforce is vital in terms of productivity. Plasser & Theurer knows this and has many initiatives, training programmes and promotional schemes in place to ensure the workforce is happy and producing high-quality output.
“For decades we have promoted the further training of the professional skills of our staff,” confirmed Johann, “and have seen many individuals progress from production assistants to jobs in the Service Department, Design Department and management levels.”
The Linz Training Centre and Technical Service Department is significant for this development. “Every week, at least two groups of trainees come here to our main plant in Linz to attend our training courses which comprise of technical construction of machines, their operation and maintenance,” Johann explained. “Most of the trainees are operating staff and maintenance personnel, however managers are also acquainted with the key criteria of handling worksites.”
Furthermore, Plasser & Theurer takes on approximately 15 apprentices every year. The apprenticeship scheme duration is three and a half years and typically leads to occupations such as mechanical engineering technicians, welding technicians, structural steel technicians and machine technicians. “It is imperative we give the apprentices the best possible training,” said Johann. “We want them to stay with us and work in our factories after completing the apprenticeship.”
The RUS 1000 S
The tour ended with a beast of a machine: The RUS 1000 S. Plasser & Theurer’s most recent innovation, this 198m-long vehicle will be able to complete a variety of tasks which currently requires three separate machines.
“The RUS 1000 S achieves an output per shift (eight hours) of 2,000m with a team of only 20 people,” explained Johann. “We offer integrated two-phase ballasting. The first tamping cycle is integrated, following track renewal and ballast bed cleaning, the machine leaves behind a track that can be opened for speeds of up to 60km/h.”
Epitomising flexibility, the machine’s design allows it to react to obstacles such as level crossings, bridges and station platforms without difficulty.
Johann said: “In addition to comfort, punctuality is one of the influential reasons that determine the mode of transport passengers will opt for and the availability of line is the most important requirement for punctual rail services.” For this reason, Plasser & Theurer continues to develop high-capacity, high-quality machines – always with a goal to ensure rail remains the superior mode of transport. To conclude, Johann said: “The rail industry is like a family. Once you are in it, you don’t ever want to leave.”
Biographies
Issue
Related topics
Digitalisation, Infrastructure Developments, Rolling Stock Orders/Developments, Track/Infrastructure Maintenance & Engineering