Mechatronic bogies: The benefits of adoption and how to reduce risks
Posted: 11 March 2015 | Christopher Ward, Mitixa Jani, Sarah Dunnett | No comments yet
The School of Electronic, Electrical and Systems Engineering with the Department of Aeronautical and Automotive Engineering at Loughborough University (UK) are undertaking innovative research that is exploring concepts and issues associated with mechatronic railway vehicle bogies. In particular, it considers how the reported benefits of these sub-systems, such as reduced complexity and less track wear, are balanced against perceived risk of their adoption on to a rail network. The work is also investigating how any identified risks with the technology could be reduced to a level equivalent to that accepted for current ‘passive’ bogies by the implementation of advanced condition monitoring techniques. This project is set within the context of a progressive and ambitious UK Rail Technical Strategy1 and the Rail Value for Money Report2 that both emphasise the need to reduce operating costs through the implementation of disruptive technology, such as the increased use of mechatronics on rolling stock. Christopher Ward, Mitixa Jani and Sarah Dunnett from the School of Electronic, Electrical and Systems Engineering, provide further details.
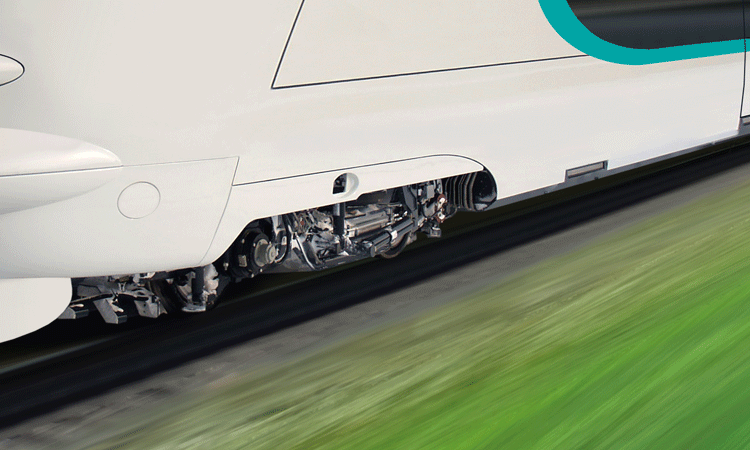
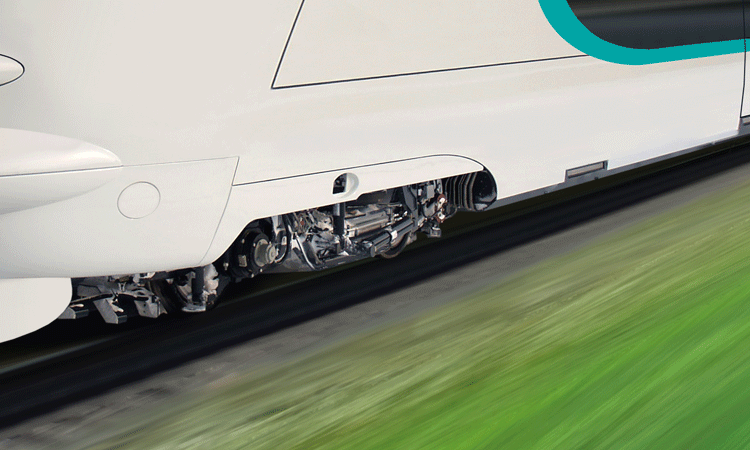
© ssuaphotos / Shutterstock.com
Bogie design context and drawbacks
Railway vehicle bogies are mature and well defined engineering sub-systems. They have developed over the history of the railways from empirically-driven mechanical engineering technology, where phenomena such has hunting3 and flange climbing were poorly understood but overcome through heuristic incremental experimental development, to complex vehicle sub-systems that require large multi-disciplinary teams to develop and where the science of contact mechanics and their dynamic behaviour is constantly improving and applied in advanced design codes.
Despite the developments and associated improvements in scientific understanding, the basic layout and function of a bogie has altered little since their inception in the nineteenth century4. Though functional, as proven on a daily basis throughout the world on networks of greatly varying operating speeds, they have a number of significant issues that make them costly to purchase, costly to operate as they are essentially ‘consumable’ items5, and costly in terms of the high levels of servicing required.
The basic layout of a bogie (that will be familiar to most readers) is shown in Figure 1. They commonly consist of two wheelsets (an assembly of two profiled and flanged wheels connected by a solid axle) connected to a robust steel bogie frame by a very stiff primary suspension that combined provide the guidance mechanism and ensure vehicle stability over a range of operating conditions. The frame is connected to the vehicle body via a soft secondary suspension that reduces vibration transmission to the passengers or freight. In modern vehicles this is usually via elastomer airbags that provide stiffness and damping, in addition to self-levelling properties for varying passenger and freight loads. In higher speed bogies there are additional anti-yaw dampers to reduce high-speed bogie oscillations, known as hunting, and anti-roll bars to reduce roll and sway motions. The bogie can also be home to a number of extra systems such as: mechanical brakes; air supplies and reservoirs; traction motors and associated transfer gearbox; sanding systems; sensors for wheel slip and slide protection; besides other numerous components.
A number of the issues with this system can be attributed to the bogies’ pair of wheelsets. Wheelsets by their nature are unstable ‘kinematic oscillators’ and give rise to the bogie hunting phenomena which was first identified qualitatively by George Stephenson4. To stabilise wheelsets a very stiff primary suspension is needed in yaw. This ‘yaw stiffness’ is a combination of the shear stiffness arising from the vertical suspension and that of the suspension bush, i.e. not attributable to a particular component. Counterintuitively, this ‘yaw stiffness’ provides damping by creating a complex system of energy dispersal in the wheel/rail contact patch, stabilising the wheelset.
This primary ‘yaw stiffness’ needs careful selection as it is a fixed value and becomes a key design trade-off. Rather simplistically: stiff primary ‘yaw stiffness’ gives the capability to go fast in a straight line but with poor curving; lower stiffness means restricted speed in a straight line but improved curving. This ‘yaw stiffness’ stabilisation leads to track and wheel wear as the vehicle cannot be optimised for all operating speeds and routes. Wheelsets generally do not experience ‘pure rolling’ as such creep forces are produced in the contact (due to wheel on rail sliding). However this is a dominant force in the guidance mechanism so some creep is needed but with the downside that wheelsets typically need re-profiling at regular intervals and rails need attention due to wear. The stiff primary suspension means that the two wheelsets and the bogie frame become a complicated dynamic system, the stabilisation of which is increasingly difficult with higher speeds. Bogies are therefore equipped with yaw dampers to eliminate this oscillation transmission at higher vehicle speeds, thus increasing the mechanical complexity of the system.
Bogie systems in general are very heavy and bulky, occupying a large volume under a rail vehicle. Due to rail vehicles being designed for a life of 30-40 years, this means that non-consumable components have to be designed to endure a long fatigue life calculated for the worst case loads (where the vehicle is assumed to be permanently crush loaded). In this critical area the industry appears wary of the use of composite materials due to crash worthiness, repairability and longevity concerns.
For bogie systems, real-time condition monitoring is a relatively new concept and may not be giving a true picture of system performance and remaining life. Systems such as Bombardier’s ‘ORBITA’6 and Alstom’s ‘Traintracer’7 have proved to be a commercial success but predominantly these systems look at collected signals and use trend analysis to determine issues that are translated into knowledge through expert analysis. Although effective, this method of doing condition monitoring is relatively nascent and there is much scope for improvement.
Despite this analysis highlighting issues with bogies, they are fundamentally very good pieces of passive mechanical engineering and perform excellently in a variety of situations. But they are designed for a compromise and have to be optimised to a specific type of route profile. This makes for a very expensive way of designing and deploying rolling stock. Risk analysis for designing and operating in this way has been built up over the past century and a half and they are extremely safe (if expensive) systems. The next section highlights that this mature technology has perhaps reached its zenith and if step changes in performance and cost are required disruptive technology needs to be embraced.
Future possibilities
The rail industry and academic community have variously proposed and investigated concepts for bogie systems to overcome the highlighted shortcomings and a number have focussed on the use of mechatronic systems. This follows the established trends in the automotive and aerospace sectors. A project based at Loughborough University in collaboration with the University of Salford8 looked at the best of these ideas and suggested how they could be drawn together into a vehicle that embraced the concept of ‘design for control’ from the early design phases.
The concept looked at many disparate concepts such as active vehicle coupling and active closely-coupled pantographs, but the majority of the benefits come from a rethinking of the suspension, guidance and traction/braking mechanism and moving away from the constraining concept of a bogie.
The concept is further highlighted in Figure 3 and at its core is the replacement of the wheelsets, with their purely passive guidance and passive suspension. Instead a combination of independently-rotating wheelsets and a single stage of suspension offers a much more adaptive, space-efficient solution with improved performance.
Removal of the solid axle between the wheels means that the hunting mode is effectively eliminated and that track wear is reduced due to lower longitudinal creep forces. However, this means that guidance is now needed (via a number of potential mechatronic systems) that steers the wheelset down the track. This guidance results in much lower track forces, lower lateral displacements and lower accelerations felt by the passengers.
The independently-rotating wheelsets would be connected to the vehicle body via a single mechatronic stage of suspension meaning there is be no need for a heavy bogie frame. This would save a great deal of weight and mechanically simplify the suspension system. The mechatronic suspension has been shown in research to have similar performance to a traditional passive dual stage system, saving weight and space9. No air supply would be needed for the suspension as it could be a purely an electro-mechanical system.
The active guidance and suspension would need high fidelity inertial sensors to operate. The concept is to use the data from these sensors in conjunction with advanced condition monitoring techniques to get a true picture of the life left in a bogie and the condition of key components. This allows a transition from calendar-based to condition-based maintenance. It would also allow for the re-thinking of design constraints to produce a lighter, more mechanically simple and high performance bogie.
If it is so good, why isn’t this happening already?
It could be argued that all of these concepts would reduce the risks associated with the guidance and suspension mechanisms of rail bogies. However, from experience this is not the perception in the rail industry that is mechanical engineering led and risk-averse for very understandable and hard won reasons. When presenting the concepts the usual questions from a sceptical audience are “what if the computer/sensor/actuator fails?” and “won’t this just cost more?” or statements like “the rail industry is too small to want this”.
The experience of the aerospace industry can be taken as an indicator of how disruptive technology becomes the norm. In that sector ‘fly-by-wire’ is considered the only method by which to design flight control systems for high performance military fighter jets and civilian airliners. This is now proven and accepted technology that is used for performance, economic and safety reasons. However, when first proposed a substantial component of the aerospace design community claimed that ‘fly-by-wire’ would never work due to performance, economic and safety reasons!10
The aircraft industry’s steady adoption of this technology was due to a number of key champions proving the benefits of this concept over more than a decade. This iterative proving method persuaded enough key engineers to provide a critical mass of positive opinion to diminish the effect of the ‘naysayers’.
A similar approach will most likely be needed in the rail industry. However, as mentioned earlier, there are clear contemporary signs that a once conservative industry is becoming open to more ‘extreme’ concepts. There is also tacit understanding that change must come in order to provide value for money for the customers and improve the performance of a currently ‘full’ system constrained by its technology level. It will be a matter of proving that the benefits far outnumber any risks, and if they are present how they can be constrained. This project is aiming to answer the final question.
Project plan
The project is in its early phases but has a clearly defined path. The current Stage 1 work involves understanding why bogies are designed and maintained the way they are now and the level of risk that is accepted. This work has involved a ground up failure modes and effects analysis (FMEA) of a generic ‘high-speed’ bogie and findings from this are being translated into a fault tree analysis (FTA) to statistically understand the paths and reasons for failure. This work is feeding in to the quantification of the running dynamics of a passive vehicle and effects of failures to understand ‘how bad things can get’ before a catastrophic event occurs. This early work is considered as a ‘benchmarking’ exercise.
Stage 2 will propose new mechatronic ‘bogie’ architecture based upon the best aspects from literature, quantify the benefits and demonstrate the level of risk associated. This will initially follow a similar path to Stage 1 with the establishment of a ground up FMEA and accompanying FTA. Dynamic models with the closed loop mechatronic systems will also be developed to quantify the effects of key failures. The FMEA and FTA will highlight key risk components and systems that should be the target of condition monitoring so that algorithms can be developed. The efficacy of the algorithms will be proven on data from the dynamic models and a comparison between the risks of passive and mechatronic ‘bogies’ drawn.
Conclusion
The development path of the traditional bogie is reaching its zenith and if further performance and cost improvements are to be found the adoption of disruptive technology is required. This article has proposed the use of mechatronic bogies that can be more ‘track friendly’ and also create new packaging opportunities in vehicle design. Certainly if the industry is to take advantage of the new technology there are a number of technological hurdles to be overcome, not only the failure issues but also new component development such as a replacement for the airsprings, electrically driven brake actuators and so on. For this reason there is a perception that this technology is ‘risky’. Research is being undertaken to quantify what this risk would actually be and compare this to the risk levels accepted for the running of today’s passive bogies. The conjecture is that these risks (if proven to exist) could be reduced by the adoption of advanced condition monitoring and that this will be shown through modelling studies.
References
- Technical Strategy Leadership Group (TSLG), The Future Railway, The Industry’s Rail Technical Strategy 2012, Supporting Railway Business, http://www.futurerailway.org/Documents/RTS%202012%20The%20Future%20Railway.pdf, accessed 10/2/2015
- Office of Rail Regulation, Rail Value for Money Study, 2011, http://orr.gov.uk/publications/reports/rail-value-for-money-study, accessed 10/2/2015
- A.O. Gilchrist, The long road to solution of the railway hunting and curving problems, Proceedings of the Institution of Mechanical Engineers, Part F: Journal of Rail and Rapid Transit, 1998, vol. 212, no. 3, pp 219-226
- A.H. Wickens, The dynamics of railway vehicles – from Stephenson to Carter, Proceedings of the Institution of Mechanical Engineers, Part F: Journal of Rail and Rapid Transit, 1998, vol. 212, no. 3, pp 209-217
- S. Marsh, Wheels are turning, Rail Engineer 17th July 2012, http://www.railengineer.uk/2012/07/17/wheels-are-turning/, accessed 10/2/2015
- Bombardier, Innovation & Technology: ORBITA – predictive asset management, the future of fleet maintenance, http://www.bombardier.com/en/transportation/products-services/services/innovation-technology.html, accessed 11/2/2015
- Alstom, Trainlife Service: Flexibility & Partnership, http://www.alstom.com/Global/US/Resources/Documents/Download%20Centre/Brochure%20-%20TrainLife%20Services.pdf, accessed 11/2/2015
- C. Ward, T.X. Mei, P.D. Hubbard & M. Mirzapour, Half-cost train: Design for Control final report, report available from RSSB on request
- A. Pacchioni, R.M. Goodall & S. Bruni, Active suspension for a two-axle railway vehicle, Vehicle System Dynamics: International Journal of Vehicle Mechanics and Mobility, vol. 48, Supplement 1, 2010, pp. 105-120
- V.R. Schmitt, J.W. Morris & G.D. Jenney, Fly-by-Wire – A Historical and Design Perspective, ISBN 0-7680-0218-4, SAE publications, PA, USA, 1998
Dr Christopher Ward is a Lecturer in control systems engineering. His research work focuses on application of advanced control and condition monitoring concepts to transportation systems. Christopher is a Chartered Engineer and Member of the IMechE.
Mitixa Jani is an EPSRC sponsored PhD student. Previously she worked as a Performance Engineer on the Class 395 vehicles at Hitachi Rail. Mitixa is a Chartered Engineer and Member of the IMechE.
Dr Sarah Dunnett is a Lecturer in risk and reliability. Her research interests include aspects of system reliability modelling, fault diagnostics and prognostics and the automation of reliability techniques.