Axle bearings and condition monitoring for railway vehicles
Posted: 18 March 2016 | Volker Brundisch - Bombardier | No comments yet
Axle bearings are a fundamental rolling stock component. Volker Brundisch, Product Manager Mechatronics at Bombardier Transportation, discusses the different monitoring strategies and technologies available for axle bearings to ensure they are observed effectively during their lifetime.
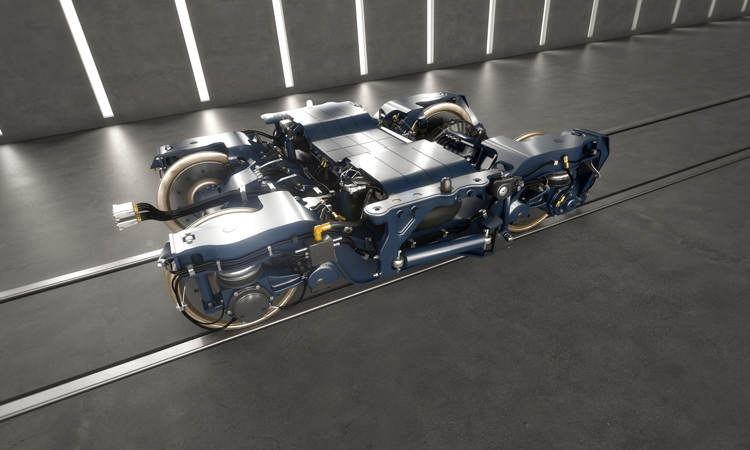
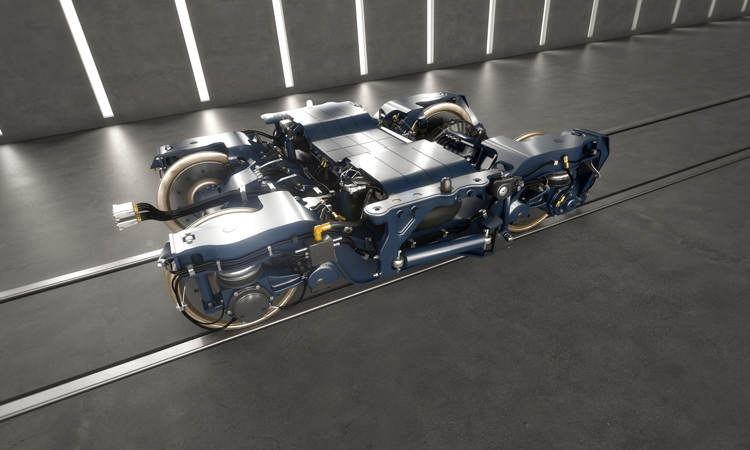
Bearings and their failure behaviour
The railway’s major differentiator from other means of transport is a pair of wheels (often jointed to a wheelset) rotating around a common axis, and supported and guided through a pair of rails. Axle bearings are the connecting design elements from the wheelset to the non-rotating parts of the vehicle. They must transmit the weight of the vehicle to the wheelsets while providing a smooth rolling movement for the wheelsets. Combining significant relative movements and high forces creates the risk for wear. Recent rolling stock are equipped with greased roller bearings –while historically, these were plain bearings which require maintenance (re-fil lubrication) and monitoring (sensing manually).
An axle bearing’s lifetime for a specific application is influenced by a large number of factors. When the design assumptions on the operating conditions are all fulfilled, the axle bearing will statistically reach its calculated life. But if this is not the case, the deviation between the real operating conditions and the design assumptions leads to damage of the axle bearing before its calculated end of lifetime. Once the damage process is initiated, it tends to accelerate: the pre-damaged bearing is source for local vibrations and heat, which both represent additional loads, and subsequently a source for damage increase.
The standard ISO 15243 classifies the bearing failure modes in six main groups and various sub-groups, with reference to features which are visible on the bearing’s functional surfaces.
Technology survey for condition monitoring
Railway operators follow different maintenance strategies; the widely distributed ones are:
- Preventive – when components are maintained /replaced ‘far before a failure’ based on lifetime (measured in years or kilometres) and independent from their precise condition
- Reactive – when components are maintained/replaced only ‘after the failure’
- Condition-based monitoring (CBM) – when components are maintained/replaced depending on their condition, by intention ‘closely before an upcoming failure’.
The CBM strategy offers to exploit the maximum lifetime of each single component, provided that its residual lifetime can be estimated:
- A measureable parameter exists which describes the state of an upcoming failure
- The failure follows steady characteristics, i.e. it does not suddenly change
- The upcoming failure can be monitored and recognised well before a fatality occurs.
These pre-conditions are given for characteristic failure patterns of axle bearings. In all cases, the measurable parameter represents the energy which is dissipated from the bearing towards the environment. Looking forward until fatality of a blocked or destroyed bearing occurs, this includes:
- Vibrations – in a very early fault stage, the axle bearing excites structural vibrations
- Noise – with increasing mechanical damage of the rollers’ path, the bearing becomes more and more a source of noise; although the level is much lower than environmental noise, it can be detected due to the characteristic frequencies
- Heat – in the final stages, the axle bearing gets hot, which can be noted from either trackside (hot axlebox detection, HABD) or on-board (request from TSI High Speed).
Therefore, condition-based monitoring for axle bearings can be based on evaluations for either mechanical vibrations, noise, heat, or a combination of these technologies. The lower the emitted energy to characterise an upcoming issue, the earlier a suspicious axle bearing can be detected, ensuring plenty of time to set up a maintenance action. On the other hand, a prognosis for a period larger than the maintenance interval is without practical benefit.
Energy harvesting must be noted when discussing bearing condition monitoring. At a first glance, avoiding cables from the axlebox to a controller in the carbody looks attractive; but this requires wireless data transmission plus local data compression at the sensor, which allows the collection of limited data only due to limited data transmission bandwidth.
Monitoring strategies
Without consideration of costs, the best approach is the permanent monitoring for every single axle bearing. For the practical purpose of supporting maintenance decisions, it is not necessary to reach these maximum. A collection of monitoring strategies exist and it is up to the vehicle operator (and maintainer) to select the approach with the best cost benefit ratio for their fleet.
Permanent On-board Monitoring (POM)
A well-known technical strategy is Permanent On-board Monitoring (POM) whereby all axle bearings are equipped with dedicated sensors. Data is then collected in controller units which provide permanent monitoring of the bearings’ health condition. This strategy provides maximum information; it can even detect damages which suddenly occur, for example from a strong mechanical impact. A set of different data handling procedures can be applied to reduce the available data to a status information flag for each axle bearing. Similar monitoring systems for POM are offered from several suppliers, although deviating slightly from each other in details of their design and data handling.
From a commercial point-of-view, POM has some characteristic features. The investment is significant, because every bearing to be monitored must be equipped with a sensor. In the best case, the POM system can be integrated in the vehicle design, which requires investment from the very beginning (even if a retrofit is possible in most cases) as well as periodic maintenance efforts for the POM system. In case of a robust axle bearing design without serial defects, the return on investment for the monitoring equipment may be low, especially when grouping of maintenance is concerned (for wheels, wheelsets and axle gear boxes) the axle bearings must be replaced anyhow independent from the condition, and their residual lifetime cannot be specifically exploited. As such, POM is especially interesting from an engineer’s point-of-view, rather than from a shareholder’s point-of-view for the vehicle owner.
Temporary On-board Monitoring (TOM)
Temporary On-board Monitoring (TOM) is a strategy with a part-time installation only of condition monitoring systems to the vehicles. Internally, the technology can basically be similar to POM. TOM’s cost efficiency results from sharing one piece of equipment for numerous axle bearings, which is to be balanced against TOM equipment’s handling efforts and train’s out-of-service costs. This pushes the application of TOM to cases with very long intervals between monitoring, or with a reasonable pre-indication of the necessity to monitor.
Up to a certain degree, dedicated measurements can be classified as TOM as well.
Permanent Trackside Monitoring (PTM)
For Permanent Trackside Monitoring (PTM), the sensors are arranged at specific locations along the track. A controller collects the sensor data, together with the identification of each passing vehicle. In closed networks, the vehicles return to that trackside station in high frequency, for example once per hour. As such, a quasi-permanent flow of state information can be collected and traced for every axle bearing. Several suppliers offer monitoring systems for PTM.
By its nature, PTM can never provide the same precision and continuity like POM. But, these drawbacks remain virtually irrelevant for the practical purpose (to support maintenance decisions for axle bearings). And some commercial aspects are strongly in favour of PTM rather than POM. Basically, the PTM system is not linked to the vehicles, also enabling to ‘unlink’ the investments in a condition monitoring system from those in new vehicles.
Bombardier’s recent and future activities
Bombardier has already developed a broad range of technical solutions in order to provide efficient and well-proven systems and services for every railway operator.
High-speed trains are equipped with the safety systems which are required from the Technical Specification of Interoperability (TSI). With implementation of additional analysis routines, the data gathered for safety purposes are also exploited to report bearing conditions. One application example of the POM system is the axle bearing condition monitoring function in the CBM system for V300 BOMBARDIER1 ZEFIRO1-ETR1000 which is developed in partnership with Hitachi Rail Italy for Trenitalia.
For temporary monitoring purposes, Bombardier developed a ‘mobile’ kit mainly designed for easy installation and dedicated to automated bearing assessment without infringement to the vehicle’s operation. A simple colour scale indicates the severity of a potential bearing’s issue, which provides the link to the residual lifetime and subsequently to an optimum intervention time.
At present, trackside monitoring is subject to intensive field tests. Investigations are ongoing about the optimum microphone arrangement and reliable detection algorithms. Moreover, Bombardier is carefully investigating the potential for further commercial improvements, for example through different approaches to maximising the number of bearings (and, not just bearings but wheels too) which can be monitored with a single monitoring system.
In the near future, more field tests will be performed to further evaluate the monitoring systems which are under development. In the long-run, both on-board and trackside monitoring systems shall be integrated as components into BOMBARDIER1 ORBITA1 – a predictive asset management system.
Reference
- BOMBARDIER, BOMBARDIER ZEFIRO and BOMBARDIER ORBITA are trademarks of Bombardier Inc. and its subsidiaries.
Biography
Issue
Related topics
Bogies & Wheelsets, Infrastructure Developments, Noise & Vibrations