Digital and geoinformation technologies in the development of Russian railway infrastructure
Posted: 22 May 2017 | Alexander Misharin, Igor Rozenberg | 1 comment
The JSC Russian Railways 2030 Development Strategy involves the large-scale deployment of advanced technology to all of the company’s business activities, including its complex infrastructure. It is tasked, among other things, with developing the technologies and processes for the design, construction and operation of high-speed lines (up to 350km/h), as well as enabling high-intensity heavy haul operations. Based on the Russian and global experience, these tasks are dealt with by introducing comprehensive measures and processes based on advanced technical and process design solutions. For European Railway Review, Alexander Misharin, First Vice President of JSC Russian Railways and Igor Rozenberg, Director General of JSC NIIAS provide an overview of these solutions.
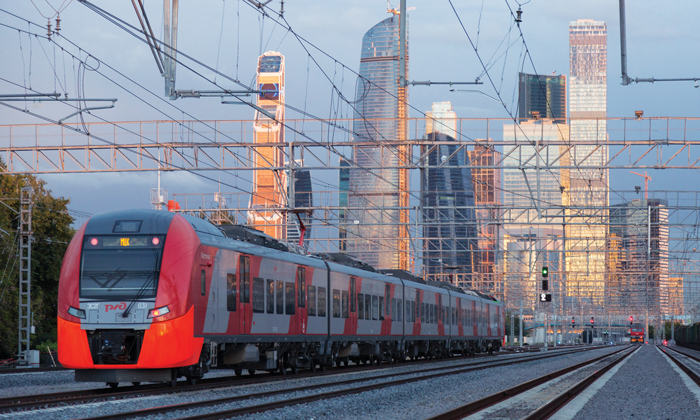
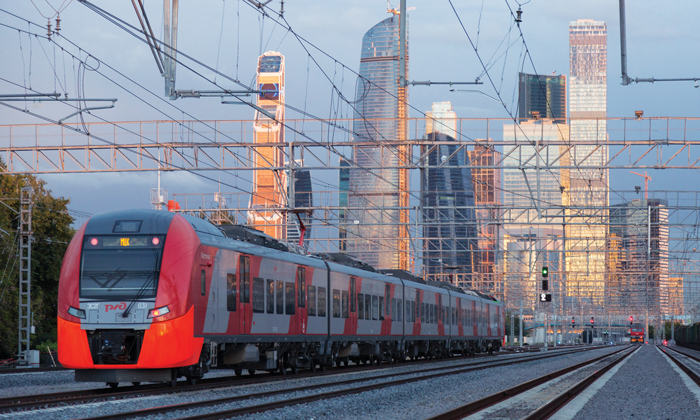
One of the innovations actively developed by the Russian Railways with regard to track and other railway infrastructure construction and maintenance is the use of coordinate-based methods. These consist of the deployment of a single high-precision coordinate space over the railway network that would enable a unified coordinate description of railway infrastructure facilities at all stages of their lifecycle, including survey, design, construction, maintenance and repair of track and structures.
It should be noted that matters of track design within the absolute coordinate system interest most members of the global railway community. The International Union of Railways (UIC) has developed Leaflet No. 728 that covers the migration to absolute coordinates.
Further UIC activities aimed at updating the provisions of the leaflet and development of high-accuracy coordinate referencing methods in railway transportation will be lead by Russian Railways experts.
Also, importantly, the comprehensive nature of the implemented solutions allows the use of deliverables across a whole range of tasks in the railway industry. Thus, Russian Railways aim to use high-accuracy coordinate models to implement digital route maps integrated in GLONASS/GPS-enabled onboard train control and protection systems. The number of trains equipped with navigation and communication train protection systems that operate on the Russian railway network amounts to nearly 20,000 units. It is expected that this solution will result in the improvement of operational performance and quality of transportation process management, as well as traffic safety.
Background and implementation
The correctness and relevance of the decision to use coordinate-based methods in per-design track operation is supported by many years of global experience that demonstrates the feasibility of reducing annual track maintenance and alignment expenditures by 20-30% through the reduction of interaction forces between the track and the rolling stock.
The implementation of coordinate-based methods by the Russian Railways is currently carried out by deploying High Accuracy Coordinate Systems (HACS) along railway lines by means of GLONASS-based satellite technologies. This is alongside the development of a highly capable information technology resource that integrates the whole base of spatial data in the form of the Integrated Railway Infrastructure Spatial Data System (KSPD IZHT).
This method was first used during the creation of the Moscow– Saint Petersburg high-speed line, where a high accuracy coordinate system was deployed to support the establishment of the Russian Railways’ common coordinate and time space (800km). The HACS includes 34 GLONASS/GPS reference stations, a satellite data processing centre and a geodetic chain that enables high-accuracy referencing of all railway infrastructure facilities. Meanwhile, the overall length of the HACS network operated in Russia is approximately 8,000km.
The system of engineering solutions that supports the track reconstruction and repair developed using coordinate-based methods is based on the following principles:
- Survey and design are carried out within the HACS single coordinate space based on the geodetic chains (GC) and GLONASS/GPS systems and high accuracy differential augmentations
- Design data for specific activities are prepared with reference to the HACS with generation of output digital track models
- Ballast cleaning and levelling and tamping machines equipped with satellite navigation systems and special software for on-board control devices ensure automated control of per-design ballast cutting and track alignment
- Acceptance of the deliverables of maintenance and overhaul activities and commissioning of tracks is made based on objective measurements of track geometry and comparison with design values, which ensures significant cost savings in routine track maintenance and preparation of new design solutions.
An overview of the key differences between the conventional process of track construction and maintenance and the KSPD IZHT process is shown in Figure 1.
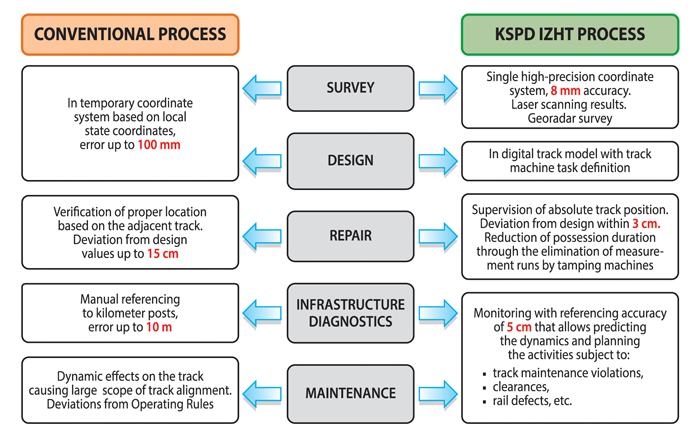
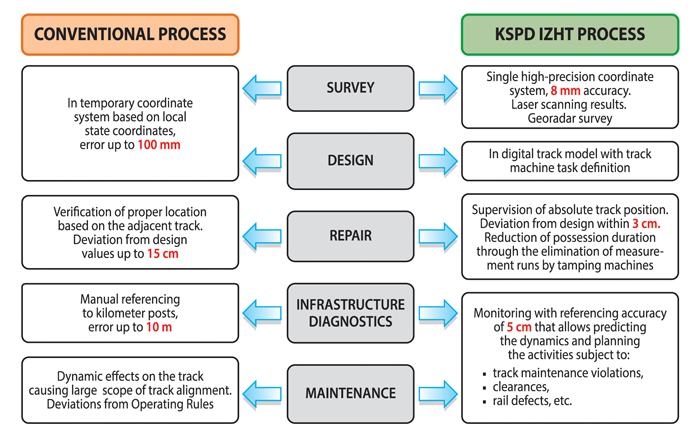
FIGURE 1: Key differences between the conventional process of track construction and maintenance and the KSPD IZHT process
The design of High Accuracy Coordinate Systems (HACS)
A High Accuracy Coordinate System is a component of the railway infrastructure and includes a geodetic chain and equipment for definition and delivery of GNSS differential corrections. HACS include the following interconnected components:
- GNSS differential subsystem that includes a network of permanent reference stations (RS) and a network centre (NC)
- Geodetic grid (GD) that includes base stations (BS), main and intermediate stations. Base stations are positioned 30- 50m apart. The mean square error of definition of the relative position of adjacent BSs in plan is 20mm. Main stations are installed 4-5km apart and intermediate stations are installed 250-700m apart. The mean square error of definition of the relative position of adjacent stations is to be not less than 8mm in plan and 5mm in height.
HACS deployed as a result, is the coordinate and metrological basis for the design, construction and operation of railway lines. It ensures the traceability of measurements and required metrology performance, and requires the absence of security restrictions for its use by involved infrastructure services.
High Precision Survey (HPS) is performed in order to stabilise GC stations with reference to the stationing and local railway coordinate system. It also enables identification of the actual values of infrastructure geometry by means of track inspection and diagnostic systems, aerial and mobile surface laser scanning, surface georadar and space-based survey.
All resulting measurements are referenced within the single coordinate space of HACS and serve as the foundation of the digital track and railway infrastructure facilities model (DTM).
DTM is a multilayer object model of track and other infrastructure elements geometrically presented in coordinate-based form, developed using the results of design and survey, high precision survey, monitoring and diagnostics. The DTM ensures the following key advantages:
- Universality of description
- Accuracy of the spatial representation of facilities
- Infrastructure facilities referencing to a single coordinate system that allows the comparison of data from different sources at all stages of the lifecycle at no extra cost.
The DTM is represented by a formalised description in an XML file and allows for retrieval of the coordinates of any characteristic point of an infrastructure facility and construction of a 3D model, if required. The DTM is the basis for digital description of infrastructure facilities that is loaded in the spatial databases of KSPD IZHT.
Technical and economic effects
The single coordinate space created and maintained within HACS allows integrating projects to be performed in different time periods and/or by different design contractors. This is in addition to making realtime modifications to design documentation based on the results of design supervision with the use of HACS and information from the KSPD IZHT databases.
The technologies based on the use of HACS and information on the actual design position of the track from the KSPD IZHT spatial databases enable the following capabilities and explained in Figure 2:
- Retrieving from the design the explicit target track geometry values to be achieved as the result of activities performance
- Checking the deviation of actual parameters from the design at each stage of the reconstruction (modernisation) process, thus enabling quality assurance of specific operations
- Reducing the operation time of track machines and the number of runs required to achieve specified geometric parameters
- Explicitly evaluating the achievement of specified track geometry parameters.
The experience of practical application of the aforementioned innovative technologies on selected lines of the Russian Railways network between 2012 and 2015 allows the following projections to be made regarding the achieved technical and economic indicators:
- Cost reductions of subsequent track modernisation design projects of up to 15% per 1km, through the reduction of geodetic survey and design activities
- Reduction of ballast use by up to 5% (266m3 per 1km) through precision removal of contaminated ballast
- Reduction of track maintenance possessions duration by elimination of the measurement run by track machines that accounts for approximately 30% of the alignment operation time or 20 minutes per kilometre
- Reduction of routine track maintenance costs and increased periods between repairs in the range of 10-20% through the reduction of interaction forces between the track and the rolling stock under condition of optimal train movement patterns
- Reduction of traction costs through decreased train motion resistance forces by means of optimal movement patterns.
The key advantage of the innovative technologies that make use of coordinate-based methods, is that they enable migration to practically substantiated condition-based track maintenance through an objective evaluation of the actual condition’s compliance with design values.
The capability of scheduled monitoring with coordinate referencing of data on track deterioration and non-compliance with standard maintenance requirements within the single HACS coordinate space also allows the collection and accumulation in KSPD IZHT databases of matching information on failures associated with non-compliant track geometry. That, in turn, enables the use of the infrastructure facilities’ spatial data within KSPD IZHT at various stages of their lifecycle in a range of automated infrastructure management systems. These are operated by the Russian Railways in accordance with the URRAN1 management methodology that is being introduced by the company.
The deployment of the single coordinate and time space of the railway industry is becoming an important component of the ‘Digital Railway’ high technology platform, as it allows for a holistic description of all interacting railway infrastructure facilities and rolling stock, in realtime as well.
There are prospects for correlated data of many measurements at railway infrastructure facilities to be taken and processed for the purpose of identifying critical deviations from standard requirements and onset of pre-failure conditions based on the URRAN methodology, as well as targeted deployment of advanced Internet of Things (IoT) hardware and software. It is becoming possible to supervise business processes and operations in a real-time fully coordinated manner, as well as managing maintenance activities involving Big Data analysis. Essentially, this paves the way for a paradigm shift in the management of the railway industry that consists of migration from an administrative management system to process-centric management supported by single end-to-end processes of traffic, infrastructure and safety management.
It is for these reasons that deployment of the technologies outlined in this article is a key element of Russian Railways’ innovative development strategy for the period up to 2030. It aims to ensure the company’s enduring competitiveness in the global transportation and logistics market. In the near future those technologies and solutions will be put to the test as part of one of Russia’s most ambitious infrastructure projects of recent history. The 770km-long Moscow– Kazan high-speed line will ensure large-scale passenger operation at speeds up to 360km/h. The design, construction and subsequent operation will, among other things, be ensured by the advanced coordinate-based processes. The most valuable experience gained in the implementation of the project will lay the foundation for further development of the Russian high-speed railway network for years to come.
Reference
1. URRAN is the body of standards and procedures, as well as software and hardware facilities, intended for integrated management of resources and processes for efficient delivery of railway transportation services in a resource-constrained environment. URRAN is based on the European RAMS methodology, yet URRAN also deals with the durability, safety of business processes, fire safety, environmental impact, human factor and economic performance. URRAN is a methodology that implements a holistic approach to enterprise asset management in accordance with ISO 55000:2014.
Very interesting article and I’d like to get in contact with you.
At the moment I’m doing research on a similar topic for the Dutch Rail Asset Manager, ProRail and we’d like to get in contact with you.
Best Regards,
Jasper Hellemons MSc
Fugro