Plasser & Theurer: Delivering safety, reliability and cost-efficiency
Posted: 3 October 2017 | Bernd Metzger, Claudia Peinsipp | No comments yet
With several decades of experience in the development and construction of track maintenance machinery, Plasser & Theurer’s track inspection vehicles contribute greatly to the safety, reliability and cost-efficiency of railway systems around the world. Colleagues Claudia Peinsipp and Bernhard Metzger explore the importance of track inspection activities and how Plasser & Theurer vehicles can provide assistance.
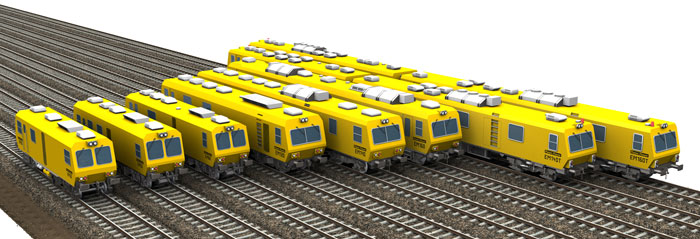
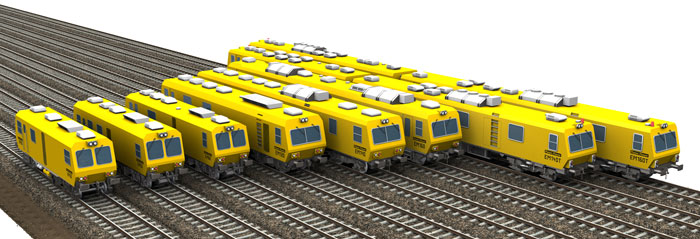
A track inspection vehicle, usually self-propelled, provides space for inspection systems, operators, operator stations and other optional interior furnishings such as a conference corner and even bedrooms.
Depending on the number and type of inspection systems, other equipment, and the measuring speed, Plasser & Theurer offers a wide variety of track inspection vehicles. This includes the EM30, the smallest track inspection vehicle in the product portfolio suitable for low measuring speeds, and the EM160T consisting of two vehicle units, which is suitable for speeds up to 160km/h.
Every track inspection vehicle is specifically designed to meet each customer’s specific needs and is built with well-proven components that utilise the most modern manufacturing techniques. This prerequisite results in vehicles with a typically operational lifecycle of 25 years and more.
Why is it necessary to inspect tracks?
The track is a dynamic system. Varying factors such as rail traffic, the nature of the subsoil, temperature fluctuations and precipitation are the main causes of track deterioration. To ensure safety and plan maintenance work efficiently, it is necessary to establish the current state of the track and evaluate the rate of deterioration.
Track inspection vehicles supply a wealth of information, based on the inspection equipment installed. For inspection systems, Plasser & Theurer follows the philosophy that only highly accurate and reliable systems with the lowest maintenance requirements shall be used in order to maximise the benefit for customers.
The following are examples of the most commonly used measuring and inspection systems, which can be operated at speeds of up to 300km/h, depending on system configuration:
Track Geometry Measuring System
Longitudinal level, alignment, track gauge, superelevation, twist (derived from superelevation), and the track gradient are measured by means of contactless technology and with high accuracy under realistic conditions (true axle loads). Apart from detecting exceptions, the results from the track geometry measurements are used for scheduling tamping works and can even indicate areas that may require ballast cleaning. The Track Geometry Measuring System from Plasser & Theurer is fully compliant with the relevant EN 13848 standard and requires no minimum measuring speed, unlike other conventional inertial measuring systems.
Rail Profile Measuring System
With this system, the full rail profile is measured and includes automatic rail type detection, rail height, rail head width, rail inclination, track gauge and minimum track gauge, and rail head lip. Rail height and width wear, plus the wear of the rail head area, can be calculated from these parameters. Based on this information, rail grinding and rail replacement can be planned.
Ultrasonic Rail Flaw Detection
Ultrasonic inspection makes it possible to identify internal rail flaws, such as cracks and splits, and to monitor their progression in order to replace defective rail sections in time.
Clearance and Ballast Profile Measuring System
Analysing the measured clearance profile also provides information on the ballast distribution, the position of the catenary wire, as well as distances to the adjacent track axes and station platforms. This allows for immediate identification of clearance infringements and an optimisation of the amount of new ballast required for tamping works. It also indicates problems with the catenary wire geometry.
Track Component Video Monitoring System
A video monitoring system helps identify loose or missing rail fasteners, anomalies in the rail surface, and cracks in concrete ties.
Catenary Wire Geometry and Wire Wear
The geometry of the catenary system can be checked (height and stagger). A pantograph allows to perform these measurements under dynamic conditions. By measuring the catenary wire wear, it is possible to analyse if and where it is necessary to replace the catenary wire.
These examples illustrate that whatever track inspection vehicle is chosen, it is possible to measure a wide variety of track parameters by performing just one measuring run, thus saving time, money and resources.
To obtain the maximum benefit from the collected data, it is necessary to convert the raw data into real information by thorough evaluation. It is also important to put different parameters into context, which can identify the root causes of defects.
Based on this information it is possible to classify the condition of the track – i.e. good condition or requiring action.
By comparing time series of measuring runs of previous months or years it is possible to perform a trend analysis and ascertain the deterioration rate for each section of the track. This helps identify the locations with the fastest deterioration and therefore the most urgent need for action.
Therefore, highly accurate location synchronisation of the different parameters is a prerequisite – the EM series provides such exact positioning by using inertial navigational based GPS and other location synchronisation options. Intensifying the level of aggregation also allows a wider group of people to utilise the information for their specific needs (see Figure 1).
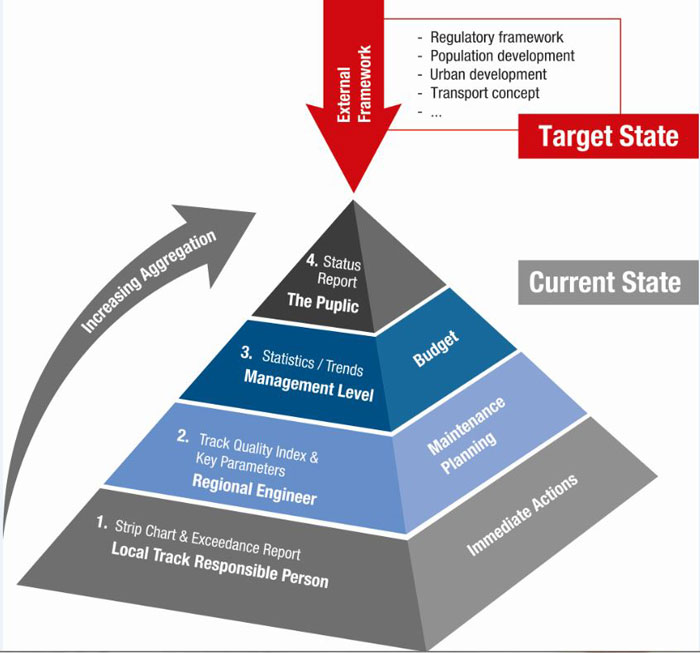
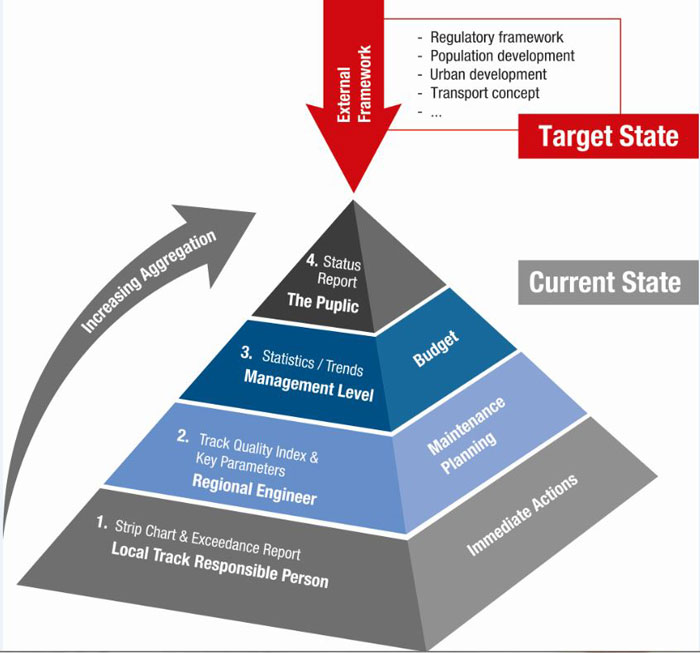
Figure 1: Aggregation Pyramid1
Another possible application for measuring systems is the installation on track maintenance machines. This offers opportunities that go beyond the mere measurement of track parameters. An inertial navigational track geometry measuring system, such as the one offered by Plasser & Theurer, installed on a tamping machine allows for precise surveying. In addition, it allows for control measurements after maintenance has been performed, eliminating the need for separate measuring runs with a dedicated measuring car. In addition to the complete documentation and quality control of the maintenance work, it also saves a lot of time as it allows the track section to be re-opened for regular traffic immediately following the completion of works.
A new development for the application of measuring systems is the turnout tamping assistance system PlasserSmartTamping – The Assistant from Plasser & Theurer, which has revolutionised the tamping process in turnouts and crossings. It increases the quality of the tamping results and simplifies the working procedure significantly. Rotating laser scanners allow for an optimisation of the ballast amount required during tamping. They are also used to check whether the track comes too close to a station platform or is lifted too high under a bridge. Other maintenance machines, such as ballast cleaning machines, use measuring systems to optimise laying and positioning of the track during work.
Plasser & Theurer is proud of its long-term customer relationships and the more than 200 track inspection vehicles delivered. This success is based on the company’s reliability as a supplier, and the cost-efficiency of its track inspection vehicles. The company also believes that the supplier’s responsibility does not end with delivery. With this in mind, a worldwide service network has been implemented to provide excellent customer support around the globe.
A quality feature of each machine is that they are ‘Made in Austria’ which assures the customers they will receive high-quality vehicles with well-proven design and adapted to their needs, using the most reliable inspection systems.
Evaluating cost-efficiency
When evaluating the cost-efficiency of a track inspection vehicle, it is of utmost importance to consider the following expense factors:
Maintenance cost
The vehicle and the inspection systems shall need minimal maintenance and the maintenance tasks required shall be easily performed by the customer.
Downtime of the vehicle
The downtime of the vehicle, either scheduled for maintenance or unscheduled due to defects, shall be as short as possible.
Lifetime of the vehicle
The vehicle shall be used for several decades. Its lifecycle may be extended by regular maintenance as recommended by the manufacturer.
All this adds up to the true cost of the vehicle and by offering reliable, high-quality vehicles with impressive lifecycles, Plasser & Theurer fully meets these considerations.
Summary
Track inspection vehicles are an important instrument for track assessment due to the multiple measuring and inspection systems installed. All parameters are recorded simultaneously in a structured and aligned way, a prerequisite for reliable long-term analysis and maintenance planning.
Furthermore, dedicated track inspection vehicles allow track maintenance personnel to witness the recording in real-time on-board, which enables them to instantly understand the root causes of exceptions and to organise immediate rectification of severe defects.
Testimonials“The performance of the measuring car from Plasser & Theurer and the installed systems is satisfactory. It helps us to optimise our track maintenance. Furthermore, the operation of the measuring car is convenient and measuring results can be achieved easily in real-time.” Choi Ji Hoon, Manager, Korail “Plasser track inspection measuring systems are a vital instrument for the safety and maintenance of our track network. The systems offer a high accuracy detailed assessment of our track geometry and precision data that is utilised in planning capital projects. Their ability to adapt to emerging technology allows us to expand our network planning efficiently to new requirements. Our fleet of Plasser inspection systems has been in operation for over 20 years and is still going strong. Plasser’s support team is one of the best in the industry and we are pleased to work alongside them.” Aarron B. Brown, Manager Special Projects – Geometry, Evaluation Cars and Surveying, UPRR Engineering “New York City is home to one of the largest, oldest, and busiest inner city rapid transit systems in the world; the New York City Transit (NYCT) system. Required maintenance is constrained as the subway system must continue to function and serve while it is being maintained. Continuous safety inspections which do not interfere with the regular train traffic and optimised maintenance planning are therefore of utmost importance. For this reason, NYCT has four Track Geometry Cars (TGC) in operation which were delivered between 1984 and 2008. Automated track inspections using NYCT’s Track Geometry Cars assure the safety of the mainline tracks by performing detailed and accurate measurements under dynamic loads equal to what passenger cars impose upon the track, at train speeds.” Antonio Cabrera, P.E., Assistant Chief Officer, Track Engineering, MOW Engineering, Subways, MTA-NYCT “CSX Transportation Inc. (CSXT) has employed Plasser’s latest geometry measuring systems on its newest Track Geometry Car (TGC3). These updated systems allow us to test track geometry up to speeds of 110mph with rail profiling, a track component video monitoring system, thermal imaging, and a clearance measuring system. All systems are synchronised with our track information and mileposts, as well as dead-reckoning GPS. The clearance measuring system is used for determining track centres, ballast profiling, public crossing approach angles, as well as clearance. The thermal imaging is used for water penetration and fouled ballast conditions when synchronised with the track component video. CSXT is very pleased with the ease of operation and maintenance of the systems, and assimilation is seamless amongst the different Plasser systems.” Brad Spencer, Director – Track Testing, CSXT “Rete Ferroviaria Italiana (RFI) has been using the tamping machines UNIMAT COMBI 08-275 equipped with the Plasser & Theurer track geometry measuring system since 2014 and we are highly satisfied with their performance. The inertial track geometry measuring system allows for the precise location of defects and makes it possible to perform geometry measurements at any speed. For this reason it can be used as a process verification system of tamping works or as a track diagnostic system. Furthermore, the measuring system enables us to check the track section for long wavelength defects as soon as the maintenance work has been finished. As we receive the measuring results in real-time, the track section can be re-opened for regular traffic immediately. A separate measuring run with a dedicated measuring car for quality control is no longer required.” Massimo Martini, responsible for S.O. Civil Engineering Directorate of RFI Production Management and Roberto Bilotti, Technical Advisor for S.O. Civil Engineering Directorate of RFI Production Management |
Reference:
- Adapted from Peinsipp, C.: Maintenance optimisation through efficient information management. Master Thesis at FH Campus Wien, 2013
Biographies