Development of digital technologies for Russian Railways
Posted: 18 September 2017 | Efim Rozenberg | No comments yet
Some recent digital solutions employed by Russian Railways include an automated train management system and a driverless system for shunting operations in marshalling yards. Efim Rozenberg, First Deputy Director General for JSC NIIAS, elucidates these developments in this article and highlights the safety and security issues posed by such digital technologies.
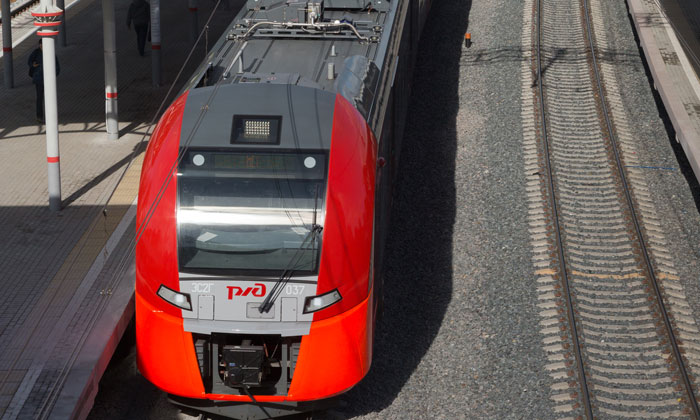
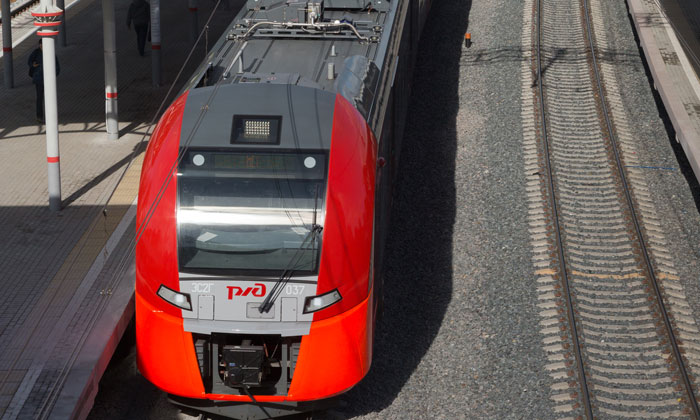
In Russia, railways account for more than 45 per cent of the national cargo turnover and over 25 per cent of the passenger turnover and consequently remain the most important mode of transportation in the country. In the context of Industry 4.0 and a highly competitive transportation market, the sustainable development of this significant sector of the transportation industry is largely dependent on the drive to develop and implement innovative technologies.
One of the most important tasks in the Russian Railways’ 2020 programme for innovative development is the implementation of the Digital Railway integrated project.
Increased competitiveness requires a transition to the digital business model that involves the coordination of all processes, online business and service management. This is the part of digitalisation that is built on the rapid development and implementation of IT in client-oriented industries and is already a hallmark of today’s global digital economy.
The fullest possible integration of ICTs
The key prerequisite for the construction of a digital railway is the fullest possible integration of information and communication technologies (ICTs) that connect the user, vehicle, train control system and infrastructure, i.e. the development of new end-to-end digital technologies to organise the transportation process. From this perspective, of particular interest are the technological innovations in railway infrastructure maintenance and railway traffic management and safety.
Many key elements of the digital railway infrastructure are already in place and operated by the Russian Railways, largely due to the efforts of JSC NIIAS – a major industry design and research institute.
For instance, Russian Railways have developed and implemented the technology for the construction of a High Accuracy Coordinate System (HACS) and associated digital track and infrastructure models (DTMs). These provide the common time and space system for the description of basic infrastructure elements and are the basis for the construction of digital route maps for on-board train protection units and the high-precision navigation positioning of vehicles.
Gradual automation of design and repair activities
This technology enables gradual automation of design and repair activities as part of coordinate-based track maintenance. The project uses the HACS and DTMs and is called the Integrated Railway Infrastructure Spatial Data System (KSPD IZHT). Currently the system covers 6,000km of the operational length of the Russian Railways network. During the pilot operation, a whole range of functional tasks were completed that relate to the spatial determination infrastructure geometry: automated identification of structure clearances, catenary geometry, visibility of crossings, as well as automation of per design track positioning.
The Intelligent Rail Management System (ISUZHT) is being phased in on the Russian Railways network. After 2020 this system is expected to replace the miscellaneous automated systems that are still operated by various divisions and units of the company. It is focused on comprehensive automation of primary processes of planning and management of the transportation process and uses a single description for all required infrastructure and processes elements.
The ISUZHT platform is an integrator of automated transportation process control systems employed by the Russian Railways. It is based on the principles of integration and the intelligent processing of all primary information regarding the status of the transportation process. This includes the status of signalling systems; speed and weight of trains; location of locomotives, trains and wagons; presence of speed limits in line sections; and the technical condition of rolling stock, automation equipment, etc.
The system is based on the principle of adaptive planning. The purpose of ISUZHT is to substitute the intelligence of dispatchers with computer intelligence using methods of machine learning and artificial intelligence. The platform encompasses the existing horizons of transportation process planning – from annual and monthly planning, as well as multiday and shift-day planning of all types of resources (including traction resources), to train handling planning. To date, ISUZHT hardware and software systems have been deployed in the information and computing centres of a number of railways in Russia with a total length of approximately 50,000km.
Automated Dispatcher/Automated Driver mode
As part of the project, an automated train management system was developed for high traffic conditions in the Automated Dispatcher/Automated Driver mode. The system allows for automated control of trains running per normal schedule, while supervising it in real-time using the satellite-navigation positioning system as part of the on-board train protection system. In the event of conflicts, the system performs an automated calculation and applies an alternative schedule to avoid conflict and restore the planned schedule. Control commands and information regarding changes to the train schedule, as well as temporary restrictions, are transmitted in real-time to rolling stock via a secure radio channel.
This technology is implemented in the large-scale reconstruction project of the Moscow Central Circle (MCC), which was successfully completed in September 2016. In order to relieve the passenger transportation system of the dig city, a reconstruction of the 54km-long ring railway around Moscow, which had been built in the last century to carry industrial freight, was completed. Thirty-one stations were reconstructed or rebuilt, including 17 interchange stations that connect with metro stations, public transportation stops and suburban railway lines. Currently, more than 300,000 passengers ride on the MCC every day.
On the MCC, the Automated Dispatcher/Automated Driver system is integrated with the combined train separation system. The latter is based on an automatic block system with audio frequency track circuits integrated with a computer-based in-station interlocking system, as well as on-board safety devices, and enables trains to run according to the moving block principle. Depending on the type of traffic, two modes of operation are possible: the light signalling mode for freight trains of fixed weight and length, and signal-free mode for accelerated movement of electric trains with a minimum interval of five minutes or less.
The MCC Automated Driver system allows for a phased transition to the use of automatic (unmanned) control systems to replace human personnel.
Russian Railways attach great importance to this approach, taking into account the economic, human and security factors. Another important aspect is the reduction of labour-intensity and the development of operator functions. In the long-term, employees will need to upgrade their skills and knowledge to effectively act in unusual situations when it is necessary to assume control.
The replacement of subway drivers is underway in a number of countries, where electric trains don’t even have driver cabs. The introduction of such solutions has become part of digital technology introduction programmes in the railway industries of several countries.
However, unlike metros, railways are open systems, where anything can happen. As such, in Russia we promote the use of trains controlled remotely by an operator with an attendant or officer present on-board in cases of emergency, rather than a fully-automated unattended mode specified by IEC 62290.
Of course, there are some challenges to be met related to automatic identification of obstacles on track. Some testing is currently under way to tackle them.
Another example is a driverless system for shunting operations in marshalling yards (MALS-BM). Such a trial is already in operation at Luzhskaya Station where the shunters are controlled via a digital radio channel with continuous automatic supervision of their location using track circuits, augmented GPS/GLONASS navigation (with differential correction) and the digital yard layout model. The purpose of this project is to validate the procedure for simultaneous control of several shunting units from a single remote workstation.
At present in the automatic mode, operations are performed by an equipped locomotive approaching a set of cars and coupling with verification. More important operations are still performed with the assistance of a driver.
The MALS shunting automatic locomotive signalling system was developed by JSC NIIAS – initially to operate in driver assistance mode approximately 10 years ago – and during this period it was actively used in the Russian Railways facilities. The use of MALS reduced the negative safety impact of the human factor. An analysis of statistical reports on locomotive operations shows that most cases of the system’s interference in the train control process, including emergency stops, are due to the driver’s attempt to overrun the allowed speed limit manually, which previously remained unnoticed if it didn’t result in accidents. With MALS all cases of speeding are logged and transferred to diagnostic workstations, e.g. in locomotive depots.
Visualisation of locomotive movement parameters and crew actions, a system of locomotive control commands at duty workstations, and display of route and signal aspect information on MALS on-board monitors enable mutual monitoring of the traffic safety of station personnel and locomotive crews and ensure process transparency. MALS enables the shunting and train operations in one area of the station to be combined with an increased traffic safety level and automatically takes account of the loads of each locomotive equipped with the MALS system and the station as a whole. The information workstations installed at the offices of the shunting dispatcher and yard master, as well as the process protocols of the systems operation, display the current status of the train, including the location of shunting locomotives and the results of work performed for a given period of time. With the help of this information, it is possible to optimise the current planning of the shunting operations and shorten the interoperation intervals or analyse the previous periods of the system and station activity.
It should be noted that the MALS system – like all the aforementioned innovative technologies – meets the requirements for cyber security, is interfaced by means of safe and secure protocols with railway automation devices, and features a functional division of vital and non-vital systems that eliminates the possibility of wrong-side failures caused by the operation of information systems.
Cyber-security issues
Cyber-security issues – which are increasingly prevalent in the context of widespread use of digital technologies – are of great importance for Russian Railways. As early as 2013, the Cybersecurity Expert Council of the Russian Railways was established, followed shortly by the establishment of the Centre for Cyber-security in JSC NIIAS, who jointly developed basic regulatory documentation. Russian Railways have carried out a lot of work and accumulated a lot of experience, during which time a thorough check of their computer-based railway signalling and remote control devices and systems has been performed. This enabled cyber vulnerabilities to be identified and an industry standard and method for cyber-security testing and certification of computer-based railway signalling and remote-control devices to be developed. Cyber-security requirements have become an integral part of any tender documentation for newly developed and implemented devices.
In practice, computer attacks against railway signalling and remote control systems can lead to violation of functional safety and wrong-side failures. At the same time, the number and effectiveness of cyber-attacks against industrial automated control systems has been steadily increasing year-on-year. Undoubtedly, under conditions of an open technology market, the consolidation of efforts of all interested parties is required. In this regard, JSC NIIAS actively supports and participates in initiatives of UIC, being its affiliated member, such as the Digital Platform and Cybersecurity Platform. In our opinion an open exchange of experience and best-practice is extremely important, as is the joint development of an international railway solution in the field of methodology for cyber-security assessment of computer-based railway signalling and remote control systems.
In addition, given the increasing digitalisation of all business processes of the railway industry, it is necessary to tackle the following key issue – namely, how to divide vital and non-vital systems safely. After all, the blending of vital and non-vital functions leads to the impossibility of proving the safety of the system (either from the point-of-view of functional safety, or from the point-of-view of cyber security). Here, we fully agree with Dr Marc Antoni, Director of UIC Rail System, who believes that “systems can be complicated, but should not be complex.”
Of course, innovative technologies such as big data, IoT and blockchain are likely to open up new prospects, and their approbation in the railway industry is already under way. We believe that it should be very cautious and based on further development of already existing systems, primarily to increase the opportunities for comprehensive risk assessment, predictive maintenance of infrastructure and rolling stock, improving the mobility of service personnel and changing the priorities in technical planning service. However, it is necessary to clearly distinguish the purpose of the technologies – i.e. control command or information action – and regulate their interaction in order to avoid reducing the safety of vital control and command systems and to avoid creating new types and classes of vulnerabilities for them when using cloud technologies. Without addressing this issue, the effectiveness and even feasibility of implementing such technologies could be questioned.
Issue
Related topics
Automatic Train Operation/Autonomous Train Control (ATO/ATC), Cyber-Security, Digitalisation