Using big data: There is no time for business as usual
Posted: 1 November 2017 | Gilles Peterhans (UIP), Maria Price | No comments yet
International Union of Wagon Keepers1 (UIP) colleagues Gilles Peterhans (Secretary General) and Maria Price (Head of European Policies and Public Affairs) take an in-depth look at the new digital and automation trends impacting wagon keepers and explain how the sector must keep pace with modern-day solutions to deliver more attractive rail freight services.
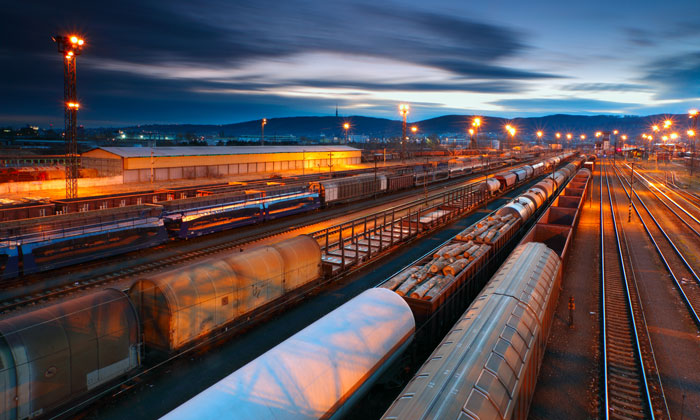
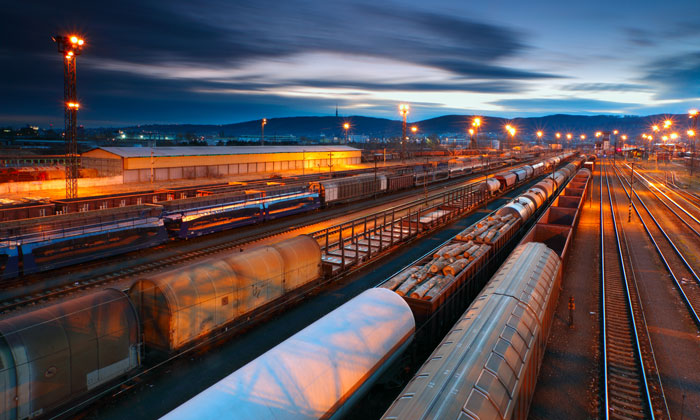
We have often argued that complying with new EU, international or national laws and trying to address the market demands and those of our customers is a big challenge for railways and where to focus their investments. For once in the world of digitalisation and the Internet of Things (IoT), we are at a stage where we are not only implementing legal requirements, such as Telematics Applications for Freight (TAF), but we are also looking for smart and innovative solutions to deliver more attractive rail freight services. For some, the new buzzwords ‘digitalisation’ and ‘automation’ are a disruption, for others they offer new opportunities. This is a new challenge for some, to which the rail sector must adapt, and to others, it is time to catch up and become the new generation of service providers.
As a default when considering a new project, every business or company (and that includes a wagon keeper) looks at the big Return on Investment (ROI). We look for a business case to justify the investments towards new retrofit and to offer new generation rail freight wagons. Previously the pressure was (and remains so) to deliver a silent wagon. Today, the new pressure, or more like the new trend, is to automate and digitalise.
Digital transport is key to the UIP’s private wagon keepers who manage 210,000 wagons, carrying more than 50 per cent of the rail freight tonne-km in Europe, and representing private investments of almost €10 billion with an annual investment volume of €400-500 million. With numerous suppliers banging on the door and doing a great job in bringing this enthusiasm of digitalisation, people and industries get hyped up on the digital technologies only to realise that they must also consider the benefit that digitalisation and data exchange can bring to their businesses and customers.
Before we decide on what IT tool or smart solution we want, first we need to ask ourselves what problem are we trying to solve, and what does the customer, as well as ourselves, really want and need? Therefore, to assess the business case for a wagon keeper we are not going to develop complex economic modelling and financial calculations. The starting point of a business case for the wagon keeper is to provide an added value for the customer.
In the same way as people use digital solutions in their daily lives, companies have become more aware of the need for sharing of information and access to data necessary for daily operations. When a railway operator plans to run a train composed of wagons belonging to different wagon keeper companies, it is important that, for example, the pre-departure checks are not delayed due to differences in the references of wagon data. Therefore, as early as 2010, UIP and its wagon keepers recognised the importance and potential for standardised data exchange and established the so-called RSRD2 – an online portal for freight wagon data which enables its users to query data and, when necessary, transfer data into their own production system. This solution for data exchange complies with the requirements of the TAF and grants ‘open access’ to any interested actor on a justified need-to-know basis.
If we are talking about existing tools, there are already many products and solutions on the market that involve digital technologies to serve rail freight requirements and to increase its potential for overall efficiency, quality of service and safety. Railways are already taking small steps in the following areas:
- Traffic management and signalling
- Telematic Applications for Freight (TAF)
- Monitoring and diagnostic sensors for braking and maintenance
- Digital tracking and tracing
- Electronic databases for rolling stock and infrastructure.
There are also continuously new activities for research and innovation and demonstrations of digital features that can promote productivity and punctuality in freight transport. Within the ‘Innovation Programme 5’ of the joint technology initiative, Shift2Rail, there are also projects related to automated coupling, timetabling, and condition monitoring for predictive maintenance.
As aforementioned, aside from IT tools, we need to ask ourselves what problems and issues we are trying to solve. We have identified that the most critical issues are: Data exchange, big data analytics and information interoperability.
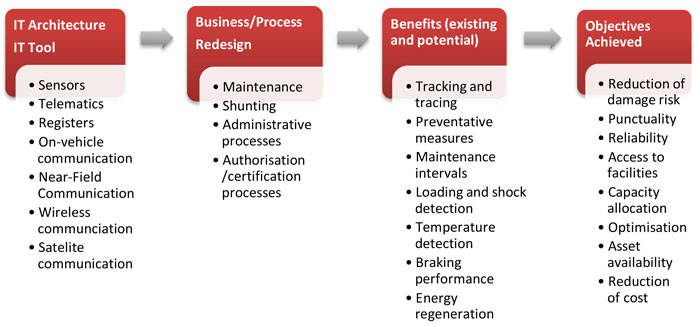
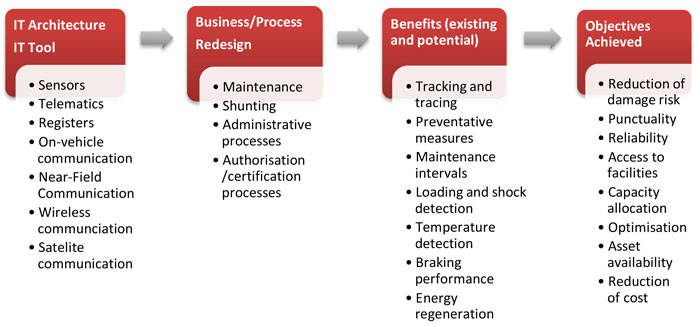
Figure 1: A business case for stakeholders to
maintain objectives for reliability and competitiveness
Data exchange
Digital rail freight transport is about capturing a large amount of data by installing telematics devices and sensors on wagons, locomotives and rail tracks, and using it to monitor and analyse vehicle condition and performance. These help to track and trace a vehicle and its load, to detect incidents such as shocks along the way or to monitor the functioning or condition of the rolling stock, to identify extraordinary wear and tear, or to measure weight or temperature of the load. Such equipment would be able to offer data not only on location, but also on the status of the wagon and its performance, also referred to as ‘event data’. For example, a wagon’s position can be available based on GPS coordinates which can also inform the customers whenever wagons enter custom-definable geographic areas (port, borders, terminals), or even approach a marshalling yard and siding. With such data, forwarders and customers can better plan the entire transport production chain and rail operators, infrastructure managers and facility operators can optimise their wagon scheduling.
Digitalisation is changing the industry
A modern-day wagon keeper is not only an asset owner, but also a service provider who supplies data that is necessary for the handling, operations, and maintenance of a wagon. Rail freight wagons are an integral part of rail freight transport and as such their data is also integral to the big data of the Single European Railway Area (SERA), whose objective is to remove administrative and technical barriers and develop simplified and common procedures and technologies at European level. Through a digital SERA, data can be collected from different sources (such as wagon keepers, rail undertakings, infrastructure managers, forwarders, facility managers and authorities) and exchanged to mutually benefit the railway system as a whole, reflecting the top priorities which include:
- Harmonised EU vehicle certification and authorisation
- Vehicle registration and marking
- On schedule EU-wide implementation of standardised data exchange (TAF TSI)
- Common guidelines for maintenance
- Harmonised systems for safety.
While some may see this as an opportunity, others may see this as a threat to their business. The path to digitalisation can be particularly steep for some medium- and small-sized companies, who may be expected to invest a great deal of technology and human resources. However, if we want to improve B2B and B2C business model and efficiency, then we need to be open to data exchange and interconnections such as machine-to-machine data.
UIP supports the EC initiative ‘Free Flow of Data’ that tackles issues of interoperability, ownership, usability and access of data. It even suggests establishing harmonised solutions towards digitalisation such as:
- Common goals for exchange of information
- Economies of scale: Share of development and operation costs and share the benefits
- Standardised and consistent data sets and formats
- Easy access to data, e.g. by central interfaces regardless of data sources
- Common governance of jointly used data exchange tools.
With the existence of a variety of telematics tools and sensors from different industry suppliers, it is of utmost importance that there is a common standard for communication (including for protocols and technological principle decisions). For this reason, an Industry Platform for Telematics and Sensor Technology, such as the ITSS, has already been put in place.
Big data analytics
Digitalisation and big data change how we collect, analyse and use data. They make us think twice on what data we should collect. As a result, it has indeed increased the value of data. The challenge we face is what to do with and how we can use this data. This is an evolution towards the way we handle big data coming from multiple sources, as well as an evolution in organisational, operational and technical decision-making. Only intelligent identification and a combination of relevant data from various sources will bring the desired improvements. A significant share of predictive maintenance for rolling stock will only be achieved with the right data collected and correlations identified. These technologies are still in their infancy, but might become a key success factor in the near future.
The business case today is both the customer demand and the digital trend itself. As shown in Figure 1, in order to maintain objectives for reliability and competitiveness, freight logistic companies and the railway operators, infrastructure managers, and wagon keepers may have to change their processes and business models and make decisions based on information received with the help of digital solutions. This will also improve communication between the actors along the supply chain and bring added value to their daily operations.
Rail interoperability also means information interoperability
As data is collected in all kinds of forms and from various sources, data and information interoperability should drive the development and implementation of digital solutions. Keepers, workshops, railway undertakings, infrastructure managers, shippers, forwarders and facility managers collect data that is necessary for their operations and forward planning. What remains is that such data is possible to exchange between the various sources and actors of the freight supply chain. Moreover, we are moving from in-house legacy systems to web-based services using Cloud and mobile applications. This requires a common approach, common standards and a common communication protocol that will allow for data to be collected, processed, queried and delivered to the relevant actor. In other words, we are now entering an era of digital trust and having confidence that we can rely on the digital solutions. This includes:
- Trust in the systems and their compliance to regulation and standards
- Trust in the data (availability and reliability)
- Trust in the security of data
- Trust that potential risks are understood.
The transition to digitalisation and automation could be slowed down when data catalogues and interfaces are not harmonised and standardised, creating inefficiencies and delays in services. Rail is a mode of the freight logistics, which on its own is a transport system of different actors with different priorities, own legacy systems and own data. Therefore, digitalisation without coordination in Europe can undermine the whole objective of SERA and with that the efficiency of rail freight by creating new barriers – this time digital ones. Having a strong and efficient framework for data exchange and big data analytics and information interoperability will bring forward the right combination of tools and digital solutions.
References: