BONAXLE® – induction hardened axle providing higher safety and lower LCC
Posted: 13 November 2017 | Global Railway Review | No comments yet
Ahead of Global Railway Review’s webinar in association with GHH-BONATRANS on 28 November 2017, we put some questions to Petr Kucharczyk, Technical Sales Specialist and speaker of the webinar, to understand more about the topics to be covered.
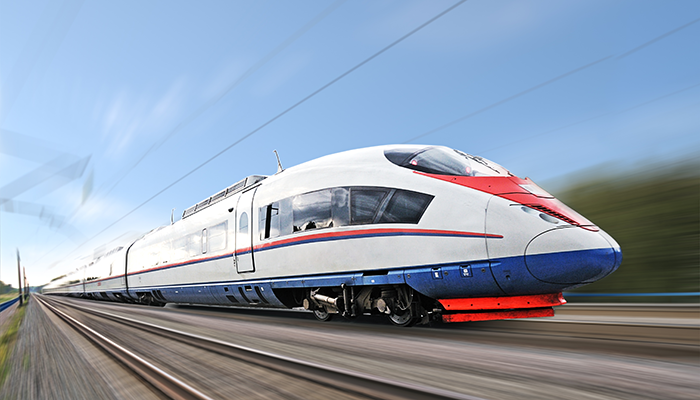
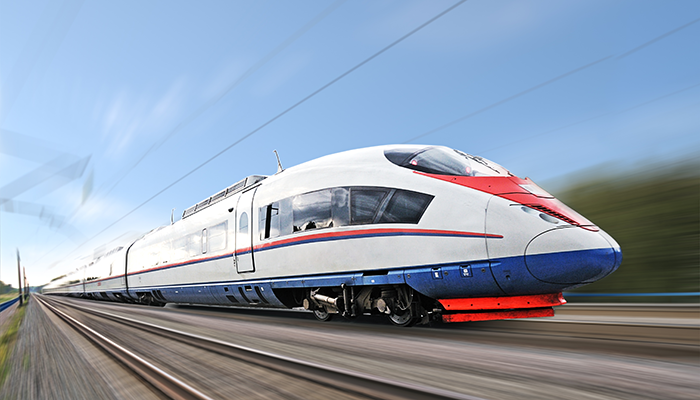
What will we learn during the webinar?
Wheelsets and axles create numerous challenges for modern day rail-bound transportation, but especially for railway operations. The webinar will investigate the ways in which BONAXLE® helps to mitigate some of these issues. It will cover BONAXLE®’s versatility with regard to geometrical designs and steel grades, such as EA4T or EA1N according to EN 13261, and the scope of tests that have been carried out to validate BONAXLE® – particularly crack initiation and propagation test, fatigue and tensile strength and impact stone test, etc. We will also provide a reference list of projects (the vehicles and their operators) in which BONAXLE® has been applied or is being tested in the field.
What are the benefits of BONAXLE® for various customers?
There are three major groups of customers and their respective expectations and associated benefits are likely to vary. Alternatively, they may appreciate all the benefits but with a different order of priorities. First of all, rolling stock operators will benefit from BONAXLE®’s stone (ballast) impact resistance, which brings savings in subsequent maintenance of wheelsets, including significant extension of a wheelset lifespan. BONAXLE® also enables NDT intervals to be extended and so reduces TLCC and increases availability of rolling stock in operation; this is due to its resistance to crack initiation as well as propagation. Also, BONAXLE® allows older platforms of rolling stock wheelsets to comply with current safety requirements. Secondly, wheelset maintenance workshops will appreciate the product’s resistance to wheel seizures during the replacement of wheels (or other components such as bearings) thanks to the high hardness of axle seat (journal etc.). And finally, rolling stock designers and manufacturers will benefit from the way in which BONAXLE® enables material (steel) savings due to the weight of wheelsets in design stage, resulting in operationally more efficient rolling stock. BONAXLE® also accommodates higher axle loads while maintaining satisfactory safety margins. From theory to practice: Locomotives of Czech and Finnish railways are already benefiting in operation, so will the new tramways in Poznan. High-speed trains in Germany, France, Russia, Korea, etc. are preparing for trials.
What sets BONAXLE® apart from other comparable products in the market?
Other technological improvements on axles usually tackle one or two issues – for instance high-thickness coating deals with stone (ballast) impact resistance mostly in high-speed operations, or cold rolling of axle surface catches on partially increased fatigue limit and partially reduces a risk of crack propagation. BONAXLE®, however, tackles a huge variety of issues in a complex way in one innovative product. Therefore, we envisage its extensive application in all vehicles in future – the quickest will be for those with powered axles. In passenger transportation it can be used from high-speed trains to DMU/EMUs, metro cars and tramways, in freight from locomotives to wagons. BONAXLE® leaves no doubt that GHH-BONATRANS are pioneers of wheelset solutions.