Combining capacity with track-friendly technology: FLEXX Tronic WAKO and ARS from Bombardier
Posted: 31 May 2010 | | No comments yet
The demand for capacity is on the increase across all areas of transportation. Due to its flexibility as a mass transportation system and its environmental performance, rail transport in particular is gaining in significance. As a consequence, many countries are making major investments to meet future demand and for systems to become and remain competitive. Yet whilst this development appears very positive for the sector, it also poses significant problems, especially in densely populated European countries where new lines cannot be easily built and the capacity limitations of existing lines are already heavily exploited.
The demand for capacity is on the increase across all areas of transportation. Due to its flexibility as a mass transportation system and its environmental performance, rail transport in particular is gaining in significance. As a consequence, many countries are making major investments to meet future demand and for systems to become and remain competitive. Yet whilst this development appears very positive for the sector, it also poses significant problems, especially in densely populated European countries where new lines cannot be easily built and the capacity limitations of existing lines are already heavily exploited.
The demand for capacity is on the increase across all areas of transportation. Due to its flexibility as a mass transportation system and its environmental performance, rail transport in particular is gaining in significance. As a consequence, many countries are making major investments to meet future demand and for systems to become and remain competitive. Yet whilst this development appears very positive for the sector, it also poses significant problems, especially in densely populated European countries where new lines cannot be easily built and the capacity limitations of existing lines are already heavily exploited.
Swiss Federal Railways (SBB) is faced with precisely this challenge today. A massive increase in demand is expected due to the wide range of services already offered and the network’s reputation for high quality. At the same time, new legislation for the future development of the network (Zukünftige Entwicklung der Bahninfrastruktur – ZEB) will generate additional demand. In this respect, certain lines will be particularly crucial and will require integrated and innovative solutions. The principle of the ZEB concept is to enhance the appeal of the service with introduction of hourly or half-hourly services (S-Bahn Switzerland concept). It is anticipated that increases in capacity will be met through the introduction of double-deck trains with reduced journey times as a result of higher performance and higher curving speeds. This can be achieved through the implementation of a roll compensation system. However, such growth in transport capacity would normally increase infrastructure maintenance costs by up to 60%, reinforcing the economic case that the use of track-friendly rolling stock will be essential over the next 25 years. With years of consistent and systematic development of rail-compliant electronics and active suspension systems, Bombardier offers products that meet these requirements on the basis of well-proven and reliable subsystems and components. The FLEXX Tronic technology from Bombardier, including roll-compensation (WAKO) and active wheelset-steering (ARS) is characterised by its high reliability and numerous benefits in performance and economy. Furthermore, investing in Bombardier rolling stock equipped with an ARS system pays for itself in just two years.
Requirements for active systems
Although nowadays almost everyone relies upon electronic systems (for example, in cars, airplanes, buses or at the doctor), concerns and reservations can emerge prior to the introduction of such systems in a rail vehicle. In spite of these concerns it is far from impossible to develop such systems and to operate them reliably. However, electronics and active systems, which may influence the safety, operation and handling characteristics of a vehicle, necessitate higher performance and quality standards. Bombardier has already been achieving these high standards for more than eight years as a basic requirement for all its electronic and mechatronic developments. Therefore, the systems are production-ready today and available with the performance characteristics described in Box 1.
Increase in transport capacity with FLEXX Tronic WAKO
The optimisation of speed, travel time, vehicle and transportation capacity is shown in Figure 1, using the example of the route of Berne-Lausanne in Switzerland. To fulfill the requirements of ZEB the journey time needs to be reduced from its current 66 minutes to 59 minutes, whilst also increasing capacity to meet growing demand. This goal cannot be realised with one measure alone. With a powerful tilting train, the journey time would be reached with some infrastructure changes, but the capacity would be drastically reduced compared to today, if the existing double-deck trains were replaced by single-deck tilting trains. Route realignments through the hilly landscape as another option would not only create significant costs, but such projects would not be feasible for environmental reasons. Under these circumstances, the most attractive solution is to introduce a powerful double-deck vehicle with roll compensation. For the various transport options, the relationships between shortening of travel time and transport capacity are shown in Figure 1.
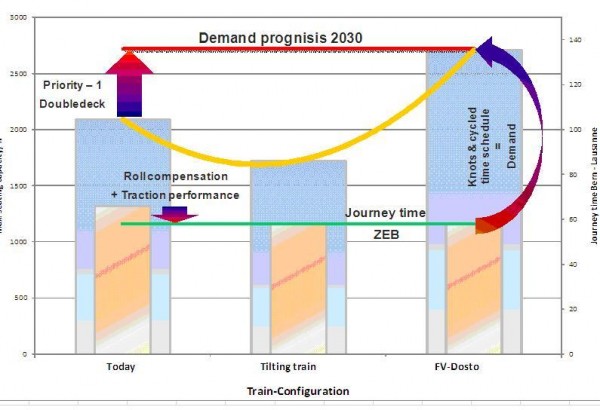
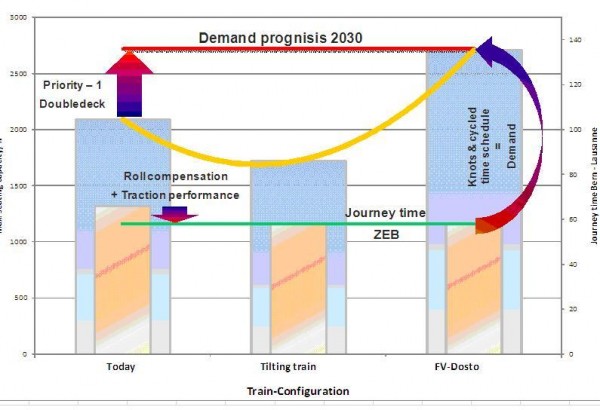
Figure 1: ZEB Requirements and Growth in Demand
To assess potential results, a comparison between IC-2000 double-deck Inter-Regional trains and Single-Deck EW-IV coaches was undertaken. With a speed increase of approximately 13% in curves, a reduction of around 8.5% in travel time can be achieved, using a tilt angle of less than 0.5°. The theoretically maximum possible speed increase is 27.8%, with a travel time reduction of around 13% yet using a tilt angle of about 7°. Considering the curving speed as specified by the SBB, this is feasible with a double-deck vehicle and with a simple roll compensation system instead of a complex conventional tilting system. With a travel time reduction of approximately 8.5% and a capacity increase of about 30% compared to today, the vehicle provides an attractive solution for the realisation of the ZEB concept. Using an integrated approach endorsing the vehicle, infrastructure and timetable concept, the required traveling time can be reduced to 58 minutes with minimal infrastructural investment.
Although the principle of roll compensation is not new, its application in a double-deck vehicle is unusual. Bombardier has particular experience with tilting systems of all kinds. The company’s roll-compensation system, named FLEXX Tronic WAKO, is based on tried and tested components and sets new standards in bogie development. The basic principle of FLEXX Tronic WAKO (see Figure 2), developed in Winterthur, is to compensate the primary and secondary outward roll movement by a tilting of the body inward in the secondary stage, thereby reducing the centrifugal forces acting on the passenger too.
The roll-compensation system is integrated into the secondary stage in a manner that requires neither an additional intermediate bolster nor an additional tilting mechanism as used in the bogies of tilting trains. All lateral and vertical deflections introduced by the roll-compensation system are absorbed by the air suspension systems. Mechanically, the FLEXX Tronic WAKO is realised by generating a fictitious elevated centre of the body’s roll movement. This notional roll centre is achieved through the position and location of the anti-roll linkages. These are inclined inwardly, which results in a theoretical point of intersection of the elongated axes at approximately the level of the upper deck. Since the centre of gravity of the body is located below this fictitious pivot point, due to the centrifugal force, it has a tendency to swing outwards and thus to tilt inwards. With the WAKO system, this movement is supported by an electro-hydraulic WAKO actuator. Figure 3 shows the position of the body and the pantograph relative to the contact wire.
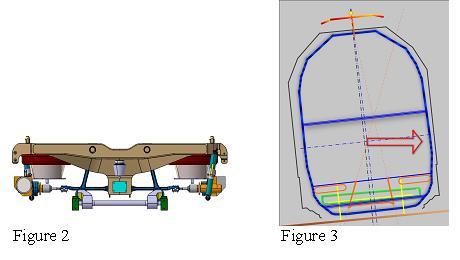
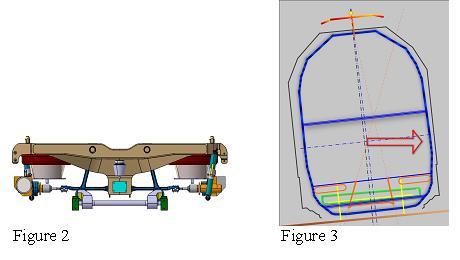
Figure 2 (image of FLEXX Tronic WAKO) and Figure 3 shows the position of the body and the pantograph relative to the contact wire
To achieve redundancy and lateral comfort, two actuators are arranged in each bogie, which exert controlled lateral forces between the bogie frame and the bolster. One actuator (the ‘compensation actuator’) works in the low-frequency range – it provides forces and displacements as required for the roll compensation (compensation angle towards the centre of the curve). The second actuator (‘lateral comfort actuator’ or ‘ALS-actuator’, ALS = active lateral suspension) operates in the higher frequency range and regulates the lateral comfort in the car body. The actuators are easily accessible because they are externally mounted on the bogie.
Regarding the option of FLEXX Tronic ARS, the same actuators can be provided with a second force output (cylinder) in the same housing (duplex actuators). This second output is used to steer the wheelsets. Due to the digital electronic architecture, this does not require an additional input; all functions of FLEXX Tronic WAKO and ARS are controlled via one single CAN bus. The signals required to control roll-compensation and comfort are provided by sensors on the bogie and in the carbody. The actuators are designed as being fail-safe, nevertheless, should one of the compensation actuators fail, the comfort actuator would be switched into compensation mode and assume this role.
Also at the level of actuator control and sensors, redundancy concepts are implemented, which provide over 15 times the reliability of classical tilt systems and hence offer exceptional availability. The WAKO system is also failsafe. Thus, by choosing the parameters which determine the lateral stiffness between the carbody and the bogie, it is ensured that, even in the case of a shutdown or complete failure of the system, the gauge envelope and catenary contact are observed under all conditions. The failed actuators therefore act as hydraulic dampers.
Solution for the infrastructure
Increased transport capacity and performance requirements also result in higher axle loads and consequently equate to increased infrastructure costs and maintenance. Vehicle manufacturers do not tend to have access to this data and with few exceptions, track access charge models, which show the benefits of track-friendly vehicles are not readily available. In the UK, a model has been applied for several years, but the application is not freely accessible. In recent years, however, a similar system was developed and validated in Sweden, which is presented below. For subsequent examination, a study was also carried out by the EPFL (Ecole Polytechnique Federal de Lausanne), within which the validated model of Sweden was adjusted for the situation at SBB.
The Swedish model takes into account the information shown in Table 1 concerning damage mechanisms as crucial to track maintenance.


Table 1: The Swedish model takes into account these damage mechanisms as crucial to track maintenance
The key variables for track damage are the vertical and horizontal forces and the friction energy between the wheel and rail. The latter is expressed in the form of a wear number. The transverse forces only include quasi-static values, the vertical ones static, quasi-static and dynamic components in combination. In the quasi-static forces, the increase in wheel load in a curve through lateral acceleration and lateral displacement of the carbody is included.
The model (see Figure 4) includes the best representations of the damage mechanisms according to the latest thinking.
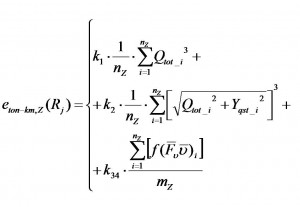
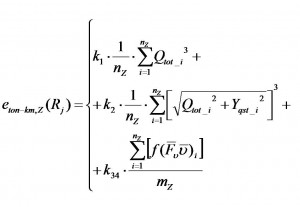
Figure 4
This formula represents the track damage per gross tonne-km and vehicle type ‘v’ in a particular range of curve radii ‘Rj’. The individual parameters are:
- k1 cost coefficient for track fatigue
- k2 cost coefficient for component fatigue
- k34 costs coefficient for wear and RCF
- Qtot Vertical wheel load
- Yqst quasi-static lateral force
- nz number of axles per vehicle
- nb number of axles per bogie function, which determines the energy dissipation in rolling contact for wear and RCF
- mz train mass
For the track and component fatigue, the following references are valid:
a) UIC / ORE D161
b) Newly developed and validated model of Andersson & Öberg (Dynamic vertical load)
c) Jenkins et al: Influence of unsuspended mass & speed
For the curving behaviour, i.e. essentially the wear and RCF, the Rail Surface Damage model (RSD) is used, which was developed by RSSB / AEA in England (see Figure 5).


Figure 5: The Rail Surface Damage model (RSD)
The cost coefficients were calibrated for Swedish conditions. The railway network totals 11,904km. The distribution of curve radii of the passenger versus cargo network is shown in Figure 6 and a comparison of traffic performance shown in Figure 7. According to an international comparison (see Figure 8), the track access charges for passenger services in Switzerland are approximately 2.4 times higher than in Sweden. The charges for freight traffic are around five times higher in Switzerland. This indicates that the cost savings in Switzerland are likely to be higher than expected relative to the Swedish model.
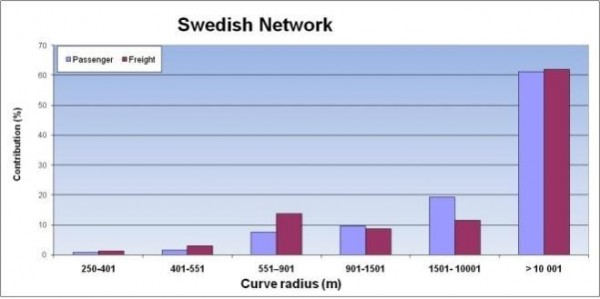
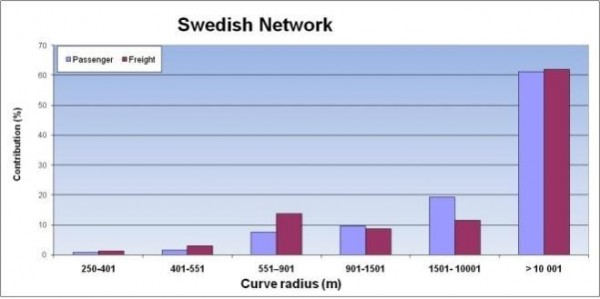
Figure 6: The Swedish network
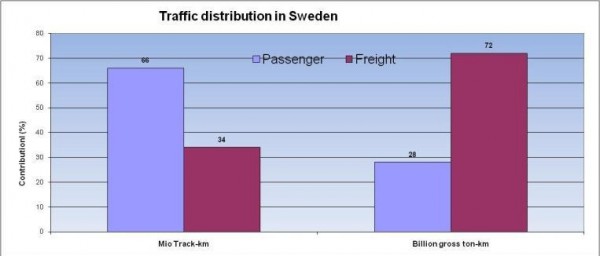
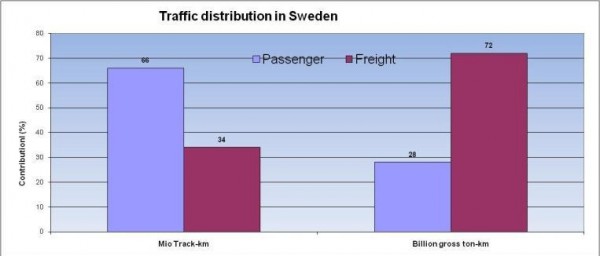
Figure 7: Traffic distribution in Sweden
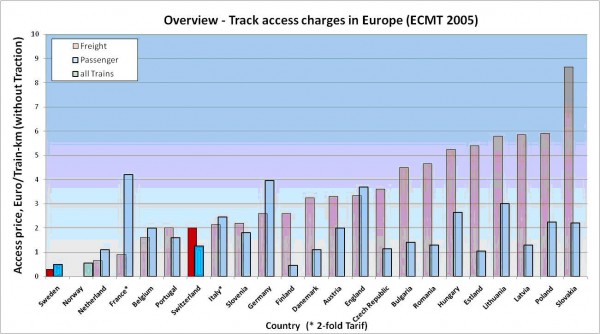
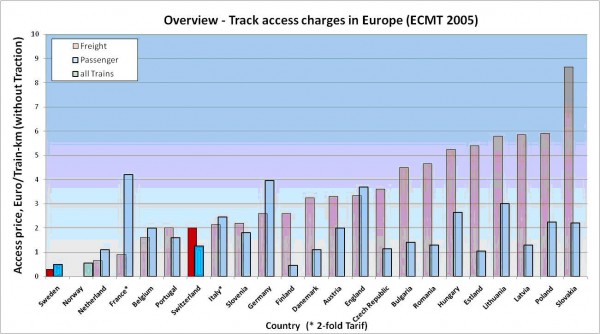
Figure 8: Overview of track access charges in Europe (ECMT 2005)
From this it is also possible to derive requirements for the vehicle design. Banverket has conducted a sensitivity analysis (see Figure 9), from which the following conclusions for critical to track-friendliness are:
- Low axle load
- Short wheelbase
- Radially steering wheelsets (flexible wheelset linkage or active steering control)
- Low unsuspended mass
- Low Speed
- Low centre of gravity of the carbody
Hence the ability to radially steer the wheelsets is decisive for wear and rolling contact fatigue. A bogie with elastically or actively guided wheelsets can produce up to 10 times lower rail damage than one with stiff axle guidance. Optimal radial steering, using both active radial steering and a stabilisation system as supplied by Bombardier, would lead to a substantial reduction of track damage when applied in double-deck coaches. In an attempt to quantify this effect a relative comparison was made (see Figure 10) on a single train on the route from Berne to Lausanne between IC/IR services with IC-2000 and EW1V and the TWINDEXX Swiss Express, both with and without ARS according to the Swedish model.
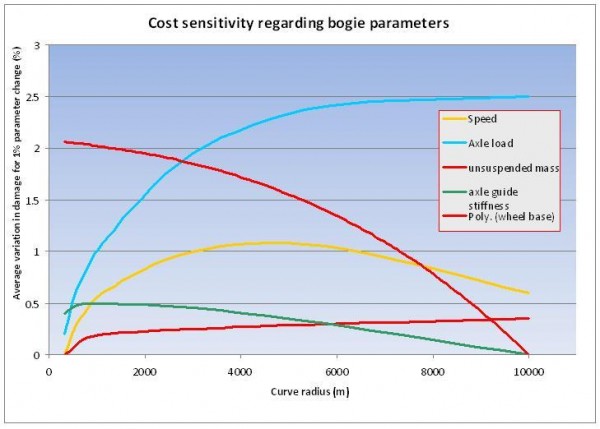
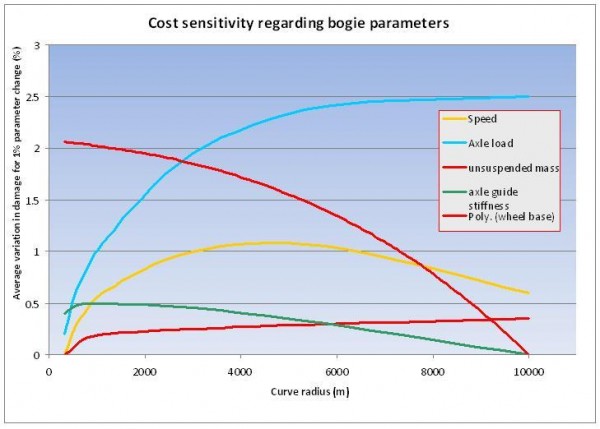
Figure 9: Cost sensitivity regarding bogie parametres
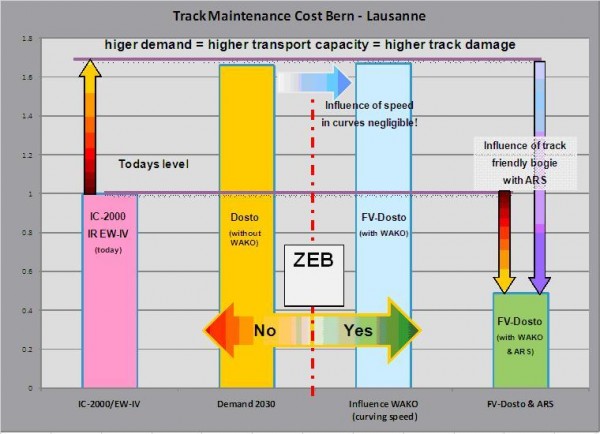
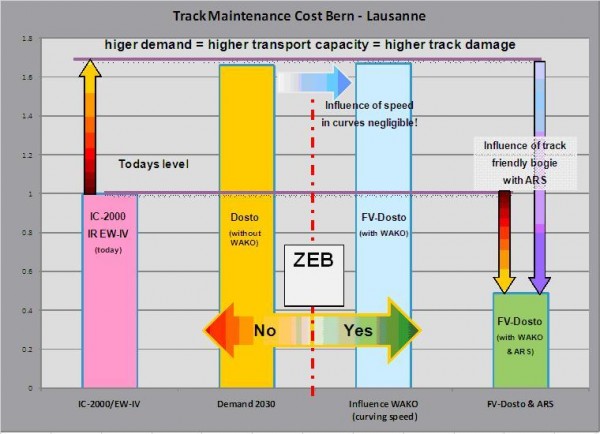
Figure 10: Track Maintenance Cost, Bern-Lausanne
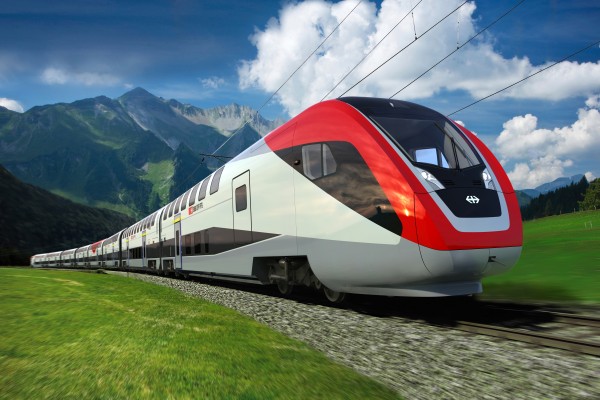
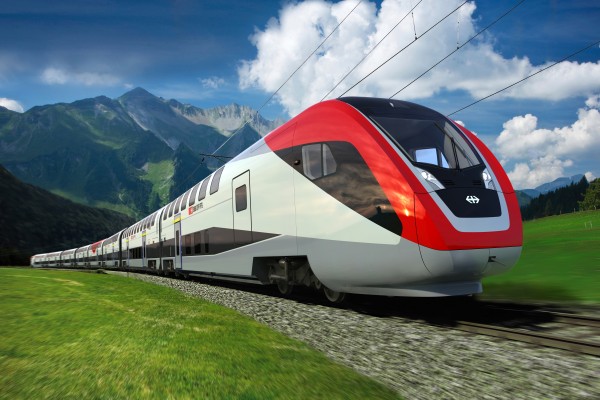
The TWINDEXX Swiss Express
Due to the higher than average axle load created by increased capacity and performance, the double-deck train without ARS yields approximately 65% increased value when compared with today’s IC/IR. The increase in speed in a curve with the help of the WAKO itself causes virtually no, or only minor additional damage to the track. In conventional bogies, an increase of lateral acceleration first of all leads to a more uniform distribution of lateral wheel/rail forces over the axles; an absolute increase in the forces is not produced before the effect of considerably higher lateral accelerations, as is the case with traditional tilting trains. With ARS, track damage for the long-distance double-deck train can be reduced by up to 70% on curvy lines. Compared with the present day IC service, the long-distance double-deck train with ARS on the Berne to Lausanne route achieves around a 50% reduction.
A determining factor for the overall economic view, however, is the comparison between the different trains on their respective lines of operation. The following indicative calculations have been carried out to illustrate the results:
- Calculation of track access charges for the lines:
- Lausanne-Berne
- Berne-Zurich
- St. Gallen-Geneva
- Calculation for the following train configurations:
- IC-2000 composition (St. Gallen-Geneva) with
- 10 IC-2000
- 4 EW-IV as a reinforcement
- 1 Loc Re 460
- EW-IV with 10 coaches and locomotive (Lucerne-Geneva)
- Long-distance double-decker with 16 cars
- IC-2000 composition (St. Gallen-Geneva) with
- The trains operate in the following cycles:
- 9 units EW-IV with 2.2 cycles per day
- 8 units IC-2000 with 2.5 cycles per day
- 17 units long distance double-decker with 2.4 cycles per day
Lausanne to Berne constitutes the curvy routes, Berne-Zurich the proportion of straight high-speed lines, and St. Gallen-Geneva represents the main application area. The track access charges are normalised to the current IC of EW-IV/IC-2000 trains; the results are shown in Figure 11.
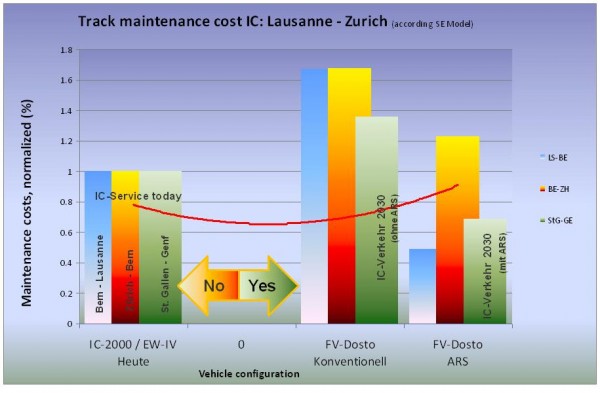
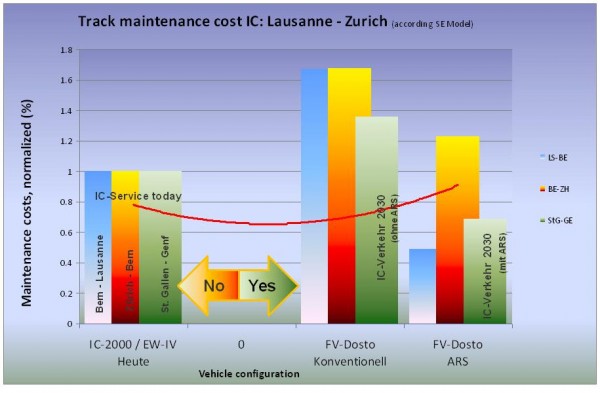
Figure 11: Track maintenance cost IC: Lausanne-Zurich (according to SE Model)
Results suggest that by using long-distance double-deck trains, the track impact without ARS increases by about 35%, but will be reduced to approximately 70% of today’s values with the inclusion of ARS. The reduction of track impact caused by ARS is, as anticipated, lower on the Berne to Zurich route than on the curvy Lausanne to Berne route. As an additional comparison, the lifetime of the rail for various curve radii can be simulated. If the rail life for every individual curve radius is known, the new rail life can be derived assuming use of a track-friendly bogie simply by considering the lower forces and lower wear for a correspondingly larger curve radius. According to such a table, extension of the rail life by up to 2.7 times can be expected with ARS, which is equivalent to performance on a straight track, yet in a 600m curve. In addition to cost savings generated by extension of maintenance intervals this also substantially reduces costs involved in maintaining the quality of the infrastructure.
FLEXX Tronic ARS: tested and certified for 200km/h
The basic principle of the ARS system is longitudinally soft guidance of the wheelsets, which allows the wheelsets to align to the track curvature without high reactive forces, in conjunction with a highly dynamic active steering device and an electro-hydraulic actuator (see Figure 12 and Figure 13).
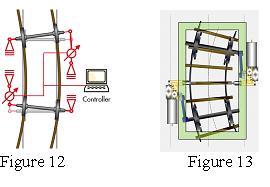
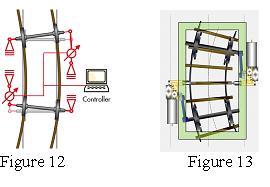
Figure 12 and Figure 13: A highly dynamic active sterring device and an electro-hydraulic actuator
The control of the actuator is performed in real-time depending on the disturbance of the wheelset movement caused by a lateral track deviation. The core of this control scheme is its separation into two frequency bands with very different behaviour. While in the low-frequency range – which is adapted to the entry and corresponding exit section of the curves – the system generates a radial adjustment of the wheelset – that is, the wheels follow the transition arc and the circular curve of the track – in a higher frequency range each track deviation will be compensated by counter-steering the affected wheelset which modifies the wheelset movement. This ensures the harmonic motion of the bogie, which can lead to instability, cannot develop. When negotiating curves, both control procedures are complementary, i.e. curving performance is free of interference from the imperfect track position.
The first series-ready version (see Figure 14) was tested in the framework of the Gröna Taget project in Sweden for a Regina train and certified according to UIC for 200km/h. At that time, an electro-mechanical actuator was used which exerts its forces and movements to the axle box via a leaf spring. In FLEXX Tronic WAKO & ARS (see Figure 15) an electro-hydraulic duplex-actuator is used, which provides an optimum combination of actuation functionality together with WAKO. This actuator is longitudinally mounted on the bogie frame. In the case of a combination of ARS and WAKO, the WAKO actuator is extended using a second output for ARS to form a duplex actuator. A steering rod is joined to this second output, which transfers the output force of the actuator as a longitudinal force to the respective axle box and thus turns the wheelset around the vertical axis. Each wheelset is independently controlled within the same bogie.
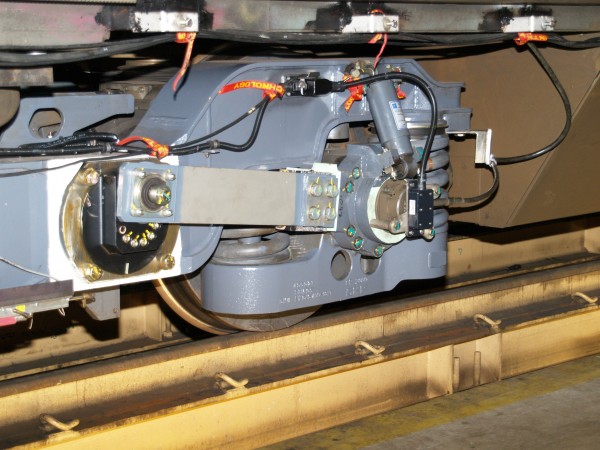
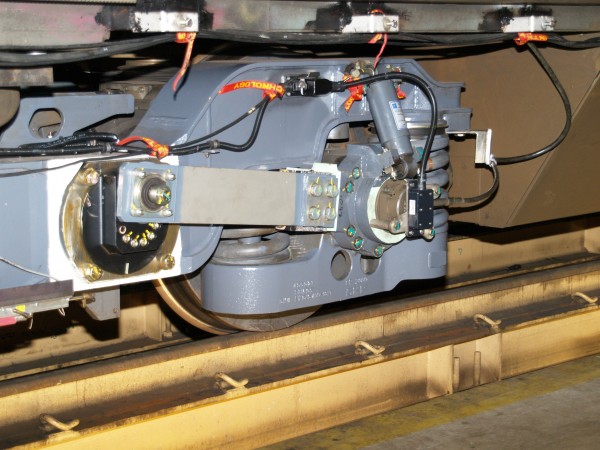
Figure 14
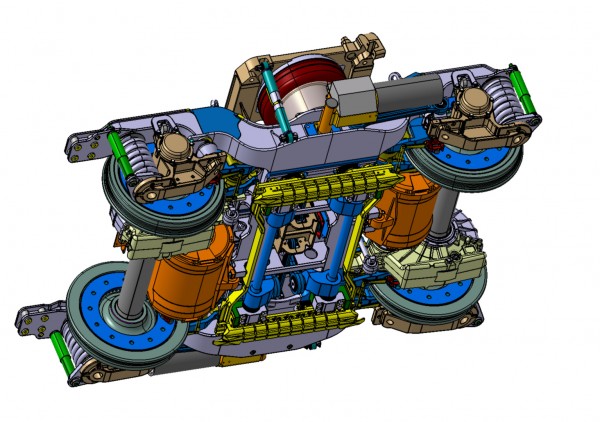
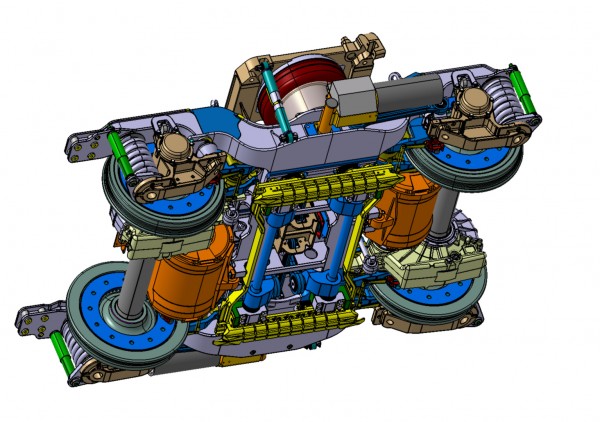
Figure 15
Benefits of FLEXX Tronic ARS
Using active stabilisation of the wheelsets negates the need for switchable or non-switchable yaw dampers or respective friction yaw damping systems between bogie and carbody, which, in the case of conventional bogies are required to stabilise the sinusoidal movement of the bogie. This eliminates a significant noise and vibration bridge between the bogie and the carbody. In addition, lower weight design is possible due to potential elimination of intervehicle dampers, and less material required for structural reinforcements, or noise isolation in the carbody.
The active steering of the wheelsets reduces or even eliminates the creep between wheel and rail compared to a conventional chassis, thereby addressing the principal contributors to both rail surface damage (rolling contact fatigue RCF) and rail wear. In addition, curve squeal noise is virtually eliminated. With the relatively stiff axle guidance of conventional bogies, the wheel/rail forces vary significantly between the leading and trailing axle of a bogie. Through the free adjustability of the wheelsets in curves, this effect is significantly reduced with active radial steering and the wheel/rail forces become more equal for both wheelsets. With an optional control algorithm, the difference in lateral forces between both wheelsets can be eliminated, especially for applications with particularly high creep characteristics, such as locomotives.
The reduction of wear-generating creep between wheel and rail reduces roll resistance, which also contributes to a reduction in the train’s energy consumption. As a result of the reduced wear and RCF of the tread, the wheel life also increases – reducing maintenance costs. These are all effects that lead to a sustainable reduction of the life cycle costs for the operator of the vehicle. Furthermore, significantly reduced rail surface wear and RCF has a favourable effect on the track maintenance and thus represents a significant bonus for the network owner.
Benefits of vehicle operation and maintenance
In summary, the principle benefits of ARS in terms of vehicle, operation and maintenance are:
- Approximately 1.5% of total energy savings of the train
- Up to 4 dB (A) noise reduction in the carbody (depending on vehicle type)
- Around 25% longer wheel life
- Approximately 3t reduction in train weight
The individual factors are briefly outlined as follows:
Energy
The decrease in rolling resistance results in a reduction of the total train energy consumption by about 1.5% on the lines of the long-distance double-decker. On lines with a higher percentage of curves, energy consumption can be reduced by as much as 2-3%.
Wheel life
The decrease in wheel wear increases the turning interval of the wheels respectively. To predetermine the amount using computer methods is expensive and also requires specific knowledge of the track geometry. Therefore, the extension of wheel life is based on estimates only. Assuming conservative estimates, wheel life can be extended by around 25%, with wheel changes reduced by around two times. To further increase the wheel life and to prevent local signs of wear on the wheel, an optional wear management program can be implemented. This software system uses the active steering ability to create even wheel wear, preventing for example local abrasions and material hardening.
Vehicle Design
By eliminating the yaw damper, a very stiff linkage between the bogie and carbody is removed. The yaw damper is responsible for vibrations of the carbody structure as well as structure-borne noise transmission; hence by removing the damper, comfort levels in the carbody will therefore be improved, as follows:
- Lower vibration
- Less noise
Figure 16 shows the noise level in the carbody with and without yaw dampers in a test situation. ARS can lead to noise reduction in the carbody of up to 4 dB (A). Alternatively, by keeping the noise level in the carbody at the same levels, use of noise isolation material can be reduced, creating a corresponding weight reduction of around 19 kg/m2. Eliminating the yaw damper additionally leads to a weight reduction of the train of about 3t for the long-distance double-decker, as the heavy yaw damper brackets are not required and a less complex carbody structure design becomes feasible.
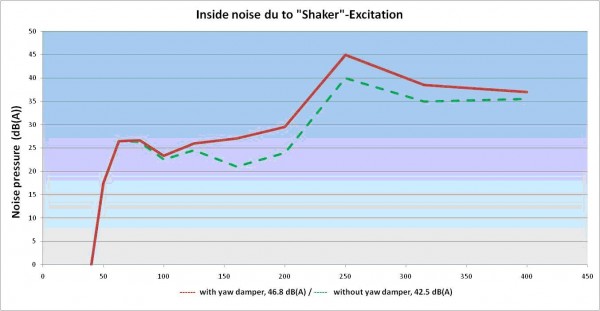
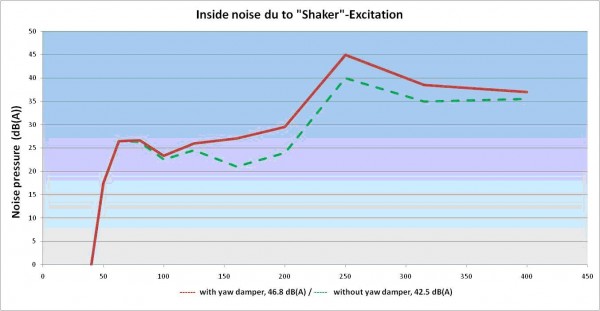
Figure 16: Inside noise due to ‘shaker’-excitation
Mechatronic architecture of the FLEXX Tronic bogie system
The basic principle of mechatronics is the introduction of a multi-functional, active system, which reduces mechanical complexity, as well as integrating the components within an information network. With FLEXX Tronic WAKO and ARS, Bombardier has introduced a very simple and easy-to-maintain system within the bogie. This design is based on the actuator concept, which combines a total of four different functions in one duplex-actuator, namely roll-compensation, comfort control, radial steering in curves and stability control at top speeds.
Electronics form an essential part of the system, which is the result of over eight years of intensive and consistent development of rail-compliant, reliable and maintenance-friendly electronics at Bombardier. For cost and availability reasons, mainly commercially available electronic components are used and specially commissioned by Bombardier for the demanding environment of bogies and axle boxes. The systems automatically configure themselves, sensors are automatically calibrated and the configuration management is continuously updated and recorded. With the additional features of redundant functionality and self-diagnostics, this leads to smooth operation and maintenance. This electronic architecture and functionality is described by Bombardier as ‘plug-and-play’ electronics.
The system can be divided into three functional levels (see Figure 17):
- The top tier is formed by the bogie controller, which controls and monitors the complete system (system management, control algorithms and diagnostics)
- The middle tier includes the sensor control boxes and the actuator controller, where the latter are already integrated in the actuator
- The lower tier contains the sensors and actuators
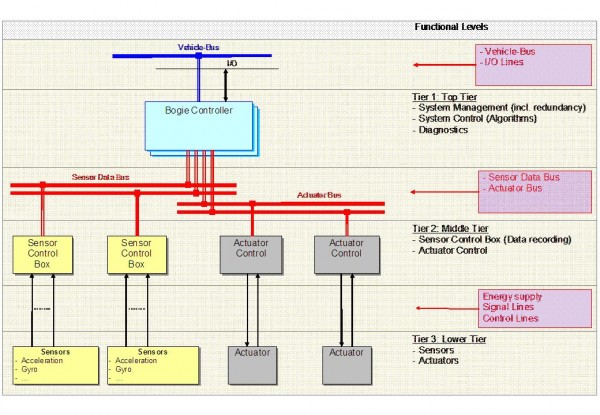
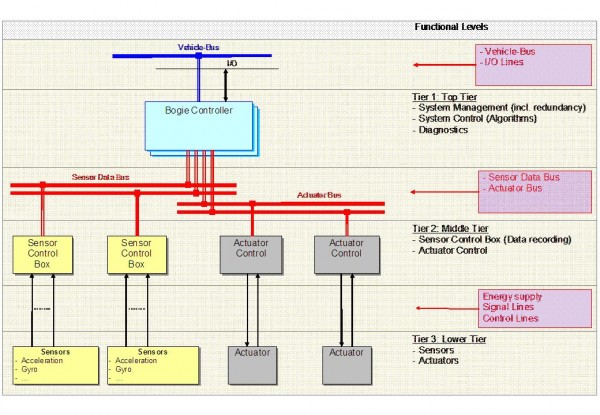
Figure 17: Simplified schematic diagram of the electronic architecture
Each part of the system is designed in a redundant manner. The Sensor Control Box is a data acquisition system, which reads the sensor data and transmits them through a digital CAN box to the bogie controller. The actuator controllers are also directly connected to the bogie controller via a digital CAN bus. With the digital CAN bus, minimal cable connections are required, resulting in much higher reliability of data transmission than with analogue connections. The bogie controller is further connected to the vehicle bus to receive train specific data (e.g. speed etc.) and to transmit diagnostic data.
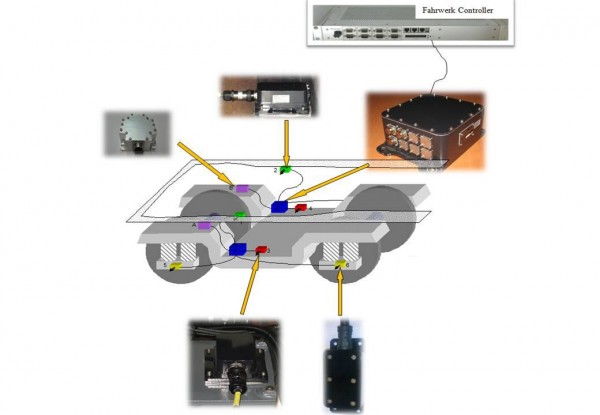
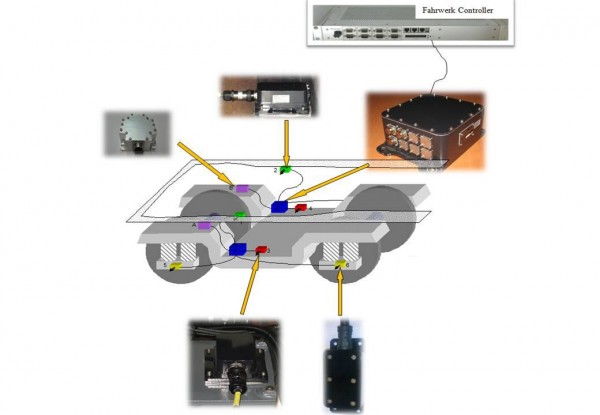
Figure 18
Designed for reliability
The consistent mechatronic design with fail-safe functionality means that components are kept to a minimum, leading to a good base reliability. This, together with the unique concept of redundancy for such systems – even extending to the actuators – means that about 15 times higher reliability is achieved compared to traditional tilting systems. This leads to virtually no operational restrictions due to failure of individual components, and the timetable can always be adhered to. Implicitly this leads to very high availability as all corrective maintenance can be carried out following completion of an operational cycle during scheduled vehicle downtime. To achieve these results, a different approach to design for maintenance and reliability is required. Active systems require an intelligent architecture (diagnosis, TEDS sensors, etc.), so that the driver and maintenance team are always informed of the condition of the system and maintenance activities and operating status can be changed according to the condition of the systems. In the case of a safety risk, the system switches off automatically and moves into a safe operational condition. The architecture allows the systems to configure themselves automatically (in a ‘plug-and-play’ mode), so that skilled experts are not required for the daily maintenance of any relevant component; the expertise required is therefore limited to component replacement. All critical components such as actuators, valves, sensors, electronic components, connectors etc. are easily accessible, ensuring they can be checked and replaced as necessary. With WAKO and ARS, the actuators are fully primary suspended, and therefore not exposed to the high accelerations and vibrations of the axle that have a tendency to significantly reduce the life and reliability of such components. As hydraulic pipes and fittings in a bogie are hard to access in terms of reliability, operation and maintenance are very complex for service and maintenance. The compact design of the WAKO and ARS duplex actuator completely avoids such issues and an actuator can be replaced with minimal effort at the depot during routine maintenance.
Profitability
Although the details of the track maintenance costs of SBB are not known by the vehicle manufacturer, an economic assessment has been made on the basis of generally available information, such as the published Annual Report of SBB Infrastructure, together with an adjustment of the Swedish model for Swiss conditions. For this, the track maintenance costs have been calculated based on specific lines and vehicles using the Swedish model and compared with the relevant data from the annual report. A so-called NPV calculation (Net Present Value) has been made, which identifies the benefits of ARS at the vehicle level. As illustrated in Figure 19, this results in a ROI of less than two years.
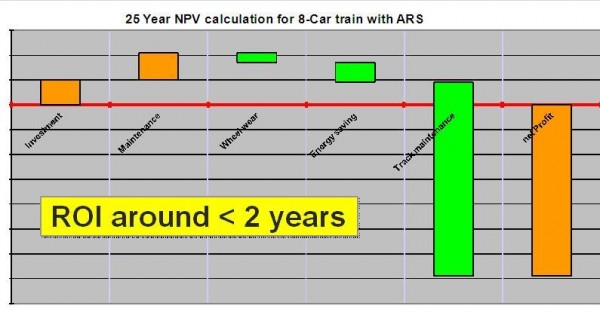
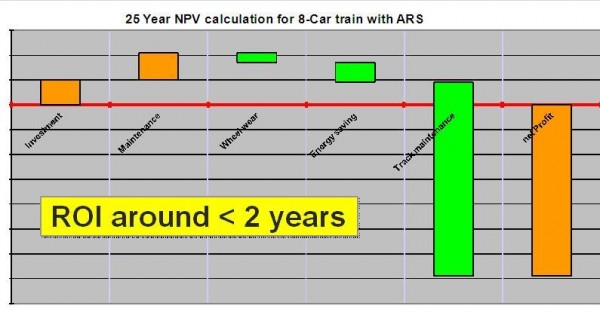
Figure 19: 25-year NPV calculation for 8-car train with ARS
For an overview economic assessment of the transportation performance, further cost factors need to be evaluated. Equivalent seat prices for an Intercity fleet would be approximately 48,000 CHF (assuming IC-2000/EW-IV), approximately 87,000 Swiss francs for a tilting train fleet and approximately 50,000 Swiss francs for the long-distance double-decker fleet. In order to obtain a realistic comparison, only publicly available data of current vehicles were used for this assessment. Thus, the ÖBB Railjet and the Austrian Western Railway double-deck train were used as a reference for today’s intercity traffic and the ETR 610 as a reference for the tilting train service. The calculations also assume that each fleet would be procured at today’s values. A total of 17 trains were set, which would allow the half-hourly cycle on the east-west axis to be achieved. For a transport service at the present level, about 1060 million CHF of investment would be required, retaining the vehicle types, but achieving the ZEB concept. The long-distance double-decker would cost about 1090 million CHF with the same transport performance and about 1150 million CHF with increased transport capacity of approximately 130%, corresponding to 100% replacement of all intercity trains by long-distance double-deck trains. With the inclusion of ARS, an additional investment of 1.5% would be required. This differentiation is striking by comparison with tilting trains. Only 57% of the price per seat of a tilting train would be required for the long-distance double-decker, i.e. a reduction of approximately CHF 123 million for approximately 74% more transport capacity. If these savings are added towards investments in the infrastructure of approximately CHF 200 million, then those investments are already more than compensated and the seat price for this service decreases with a net investment of approximately CHF 950 million to about 41,000 CHF (see Figure 20). One can clearly conclude that the transport performance can most economically be realised with this vehicle and transport concept. Together with the yearly savings in infrastructure maintenance, thanks to ARS, a sustainable improvement in profitability can be realised.
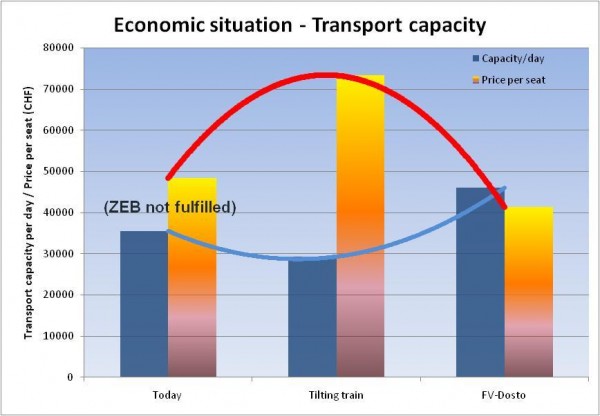
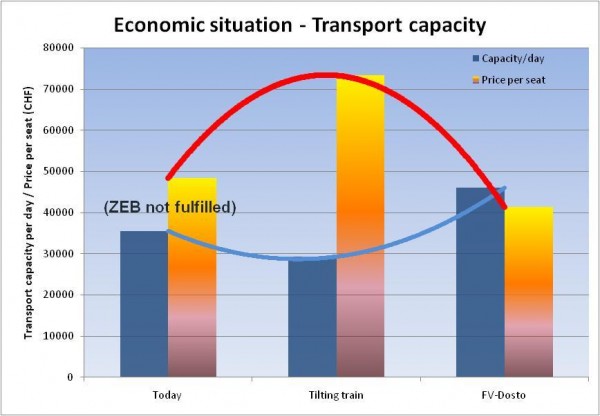
Figure 20: Economic situation – transport capacity
Conclusion
Without a shift towards macroeconomic considerations, and their consistent incorporation within the business models of operators and infrastructure owners, the general development of the railway market will, in certain areas, inevitably lead to the disintegration of the infrastructure. Nevertheless, the requirement for performance dictates that capacity levels will continue to rise, resulting in higher axle loads and extended operating hours. In turn this means that less time will be available for infrastructure maintenance, although more time will be needed. Moreover, finance for this maintenance will not necessarily be available. The FLEXX Tronic WAKO and ARS systems offered by Bombardier provide a viable solution, whilst providing a sustainable contribution to the preservation of the infrastructure. In combination with double-deck vehicles, WAKO provides a transport capacity increase of up to about 30%, and ARS results in up to 50% reduction of track maintenance costs for the long-distance double-decker itself and about 30% reduction from the present state, which in addition, leads to a prolongation of the maintenance intervals of the track of approximately 2.7-fold. The alternative scenario would be additional track damage, generating around 35% higher track maintenance costs with correspondingly shorter maintenance intervals over the next 30-50 years. Taking into account all cost factors for ARS, one can expect a return on investment (ROI) of around 2-3 years, a very attractive option for a company’s long-term strategic plan. Nevertheless, systematic procurement of track-friendly vehicles would require wide-scale changes in policy with a full commercial and monetary evaluation of the benefits which result from this technology. This would create additional incentives for the development of track-friendly vehicles resulting in sustainable solutions to the problem of long-term infrastructure maintenance.
About the Author
Dipl. Ing. Richard Schneider
After working as an apprentice and studying Mechanical Engineering with a Diploma, Mr. Schneider’s career has seen him taken many positions including Development Manager in the Railway Department of SIG Schweizerische Industrie-Gesellschaft, Director of Engineering in the Business Unit Bogies of Adtranz and Vice President of Engineering in the Business Unit Bogies of Bombardier Transportation. Throughout his career, Mr. Schneider has achieved many milestones including, among others, the development of the bogie and titling system for the ICN train from SBB and the development of the first Mechatronic Bogie.