Weld registration and acceptance
Posted: 27 September 2008 | | No comments yet
For a long time now, poor weld geometry has been a major problem for railway infrastructure. Due to geometrical imperfections, high dynamic loads could be generated during wheel passage. The only way to control the geometrical quality in an effective way, is by measuring and documenting every weld with an electronic straightedge such as the […]
For a long time now, poor weld geometry has been a major problem for railway infrastructure. Due to geometrical imperfections, high dynamic loads could be generated during wheel passage. The only way to control the geometrical quality in an effective way, is by measuring and documenting every weld with an electronic straightedge such as the RAILPROF1 (see Figure 1).
This device is now widely used on the network in the Netherlands and also in various other countries. The key parameter in the assessment process is the first derivative of the longitudinal geometry in a vertical direction. This value is proportional to the dynamic wheel rail force and therefore also speed dependent. For each speed class, a so-called quality index (QI) is determined, representing the actual inclination divided by the norm value2. The admissible inclinations according to the ProRail standards3 are shown in Table 1.
In a lateral direction, the dynamics are less critical and here the admissible values (expressed as versine) are shown in Table 2.
Weld registration
In order to get payment for the welds produced, the contractors in Holland have to submit to ProRail, the Dutch Rail Infra Manager, various items concerning the weld such as location, work carried out and quality achieved. In fact, when all data is submitted correctly, the contractor then receives his payment for the job.
In the past, the data was collected in paper form, which was filled in by hand, and then the papers were collected and submitted to ProRail. This was of course a tedious job and a process asking for mistakes!
To overcome these problems, Esveld Consulting Services (ECS) has developed a tool to collect data in a pocket pc (PPC) and to then transmit these wirelessly via GPRS to a central server. This system is called WeldRegister. The welder can key in, or select, data such as:
- RAILPROF used
- Project data
- Information about track location
- Switch configuration or straight, and writing on the screen additional information such as internal weld number
- Rail profile and weld material data
- Work information like neutral and actual temperature, tamping, fixing of fastenings
- GPS information via internal GPS receiver
- Camera picture if necessary via internal camera
- Automatically attaching the latest measurement file made by the RAILPROF
- Quality indices
- Remarks, Name and Signature of the officer in charge of the project, if necessary
For the implementation, a Symbol MC35 PPC is used with GSM, GPRS, built in GPS and a camera. The software runs under Windows Mobile 5 or 6.
The PPC software was developed on the basis of building block software produced by Pocket PC Creations in Australia4. In this environment the WeldRegister application was developed. The server runs on a PC with an externally accessible IP address. Information can be sent in both directions between the server and PPC.
In the PPC software, default values can be set and as much as possible selectable items are used via scroll menus. Figure 2 shows an example. Once all data has been keyed in for a specific weld, the information is transmitted to the server via GPRS.
The server contains an internal database by which the same information as on the PPC can be reproduced. However no queries are possible. This is achieved by linking the internal database to an MS Access database, for which special coding was purposely created in Visual Basic. In this so-called WeldRegister database, all types of selections can be made for viewing and printing. Figure 3 shows the items list for the welds in the database. Each weld is assigned a unique number and also the connected items like camera pictures, switch layout, signature and RAILPROF file have this prefix in the file name. These items are not stored directly in the database to avoid increasing of the seize, but they are hyperlinked. When clicking on the link in the database, the file is automatically opened.
When clicking on the GPS coordinates the location is shown in Google Maps, an example of which is shown in Figure 4 on page 103. In this way the weld locations for a particular contract can be shown in a special map created in Google Maps.
Contractors in Holland measure in the order of 10,000 welds per year, and so if no software tools are available, selection and retrieval of welds is a tedious job. In WeldRegister, this is now very simple. Selections can be made, amongst others, on:
- RAILPROF ID
- Welder
- Project
- Time
- GPS coordinates
- Weld properties
For the selected welds, Item Details can be generated as indicated in Figure 5 on page 103. All selected welds can then be printed directly to a pdf file with one page per weld according to Figure 5 on page 103. In fact, the pdf file is submitted to the client for approval and acceptance of the work.
Weld geometry acceptance
With the introduction of this method, ProRail has decided to go for 100% measurement and registration of the welds. Also, the acceptance is based on, in principle, 100% compliance with the standards. Of course, with measurements there are always tolerances which should be taken into account. Besides a minor exceedence of the standards might be a point of negotiation, rather than replacing the weld. Therefore, the author would like to propose the following procedure as regarding the acceptance, based on the quality index QI:
- 0 < QI < 1.15 Accepted, taking into account 15% margin for measuring inaccuracy;
- 1.15 < QI < 1.25 To be negotiated and leading to reduced payment
- 1.25 < QI Rejected
Calibration of electronic straightedge
In the recently developed calibration proposal for electronic straightedges, the straightedge is tested on a precision measured rail with deviations such, that the QI is approximately 1. This is because the discussions will always be focused on whether QI is just below or above one. If the calibration result shows a deviation of 15% of the precision measurement, then the straightedge should be adjusted. For the situation at ProRail, with a maximum speed of 140km/h, the following limits are shown in Table 3.
The 15% used here is the same value as adopted in the earlier discussed uncertainty margin added to the limit value of QI =1, i.e. accepting a QI of 1.15.
The calibration interval is set in relation to the measuring intensity according to Table 4.
Conclusions
Poor weld geometry causes high impact loads during wheel passage and consequently leads to rapid deterioration of track components. Effective control of the weld geometry is therefore inevitable. However, this requires high precision electronic straightedges like the RAILPROF, as the weld geometry standards are in the order of a milliradian (1 mm per meter) and the measuring accuracy should consequently be one order better. This requires strict calibration procedures. With an accepted measuring margin of 15% the admissible standards should also be enlarged with this value to QI = 1.15.
With the WeldRegister software, not only is the data transfer achieved efficiently via GPRS, but the data storage and retrieval is also performed in seconds – resulting in a significant cost reduction for data management.
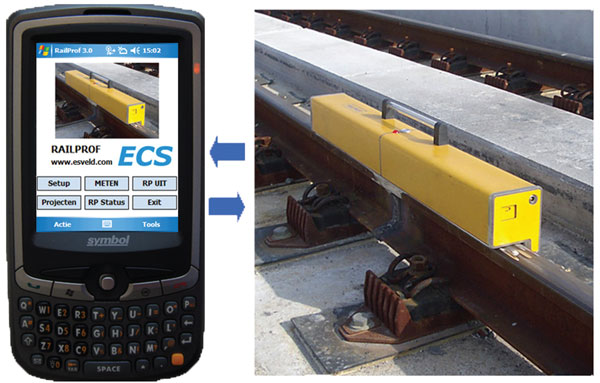
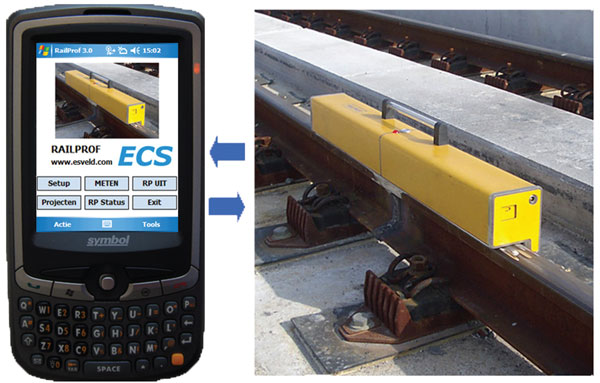
Figure 1: RAILPROF
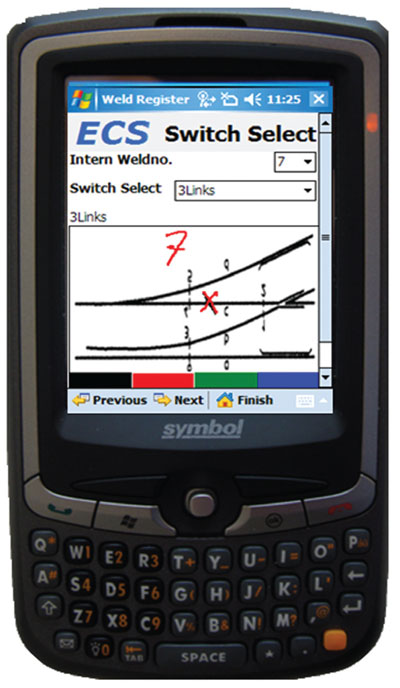
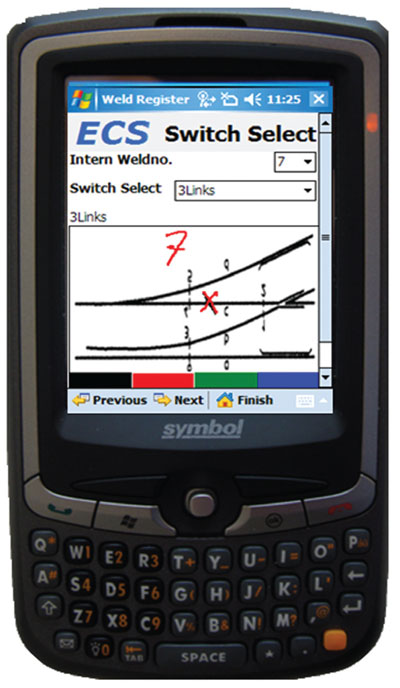
Figure 2: Example of PPC screen
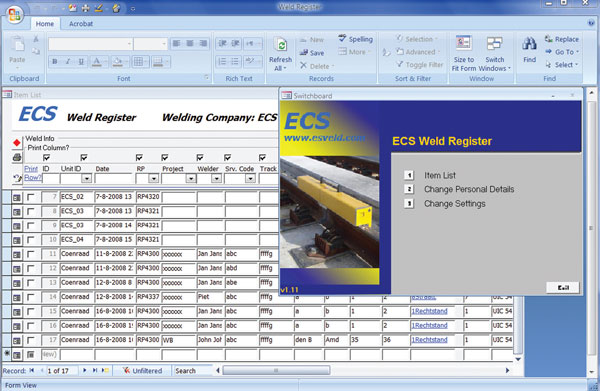
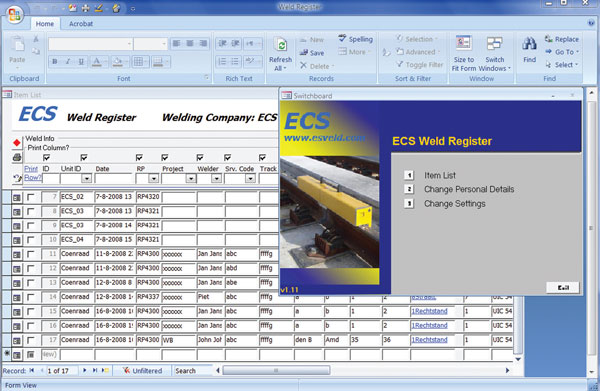
Figure 3: Item list
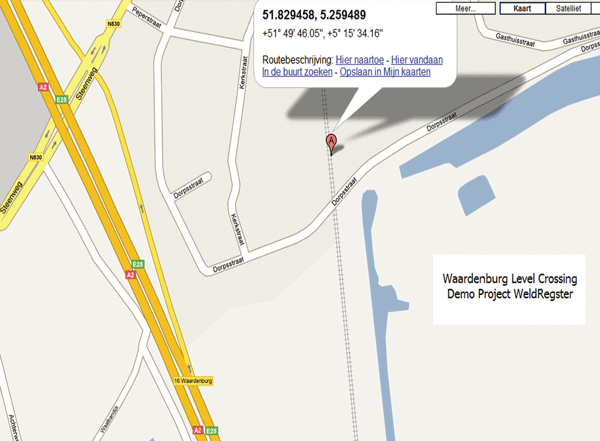
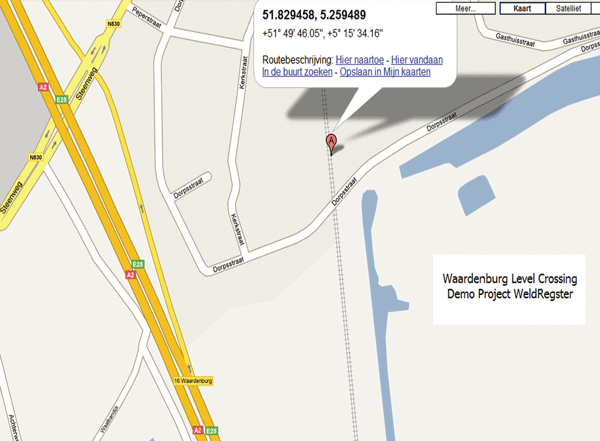
Figure 4: Example showing weld location in Google maps
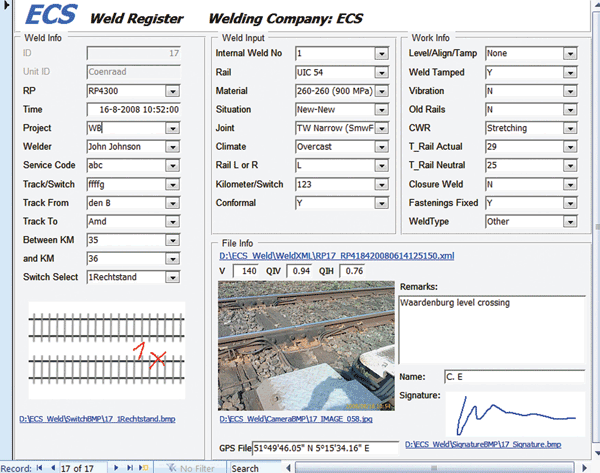
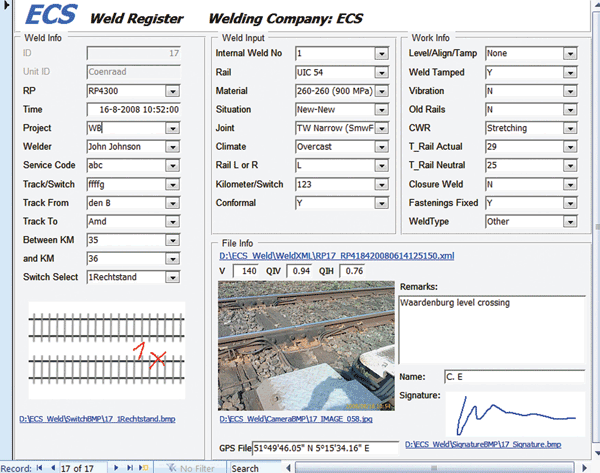
Figure 5: Item details
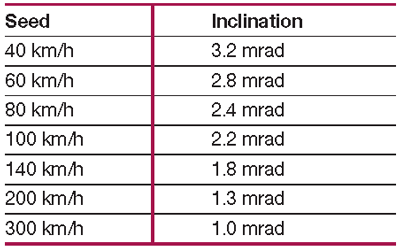
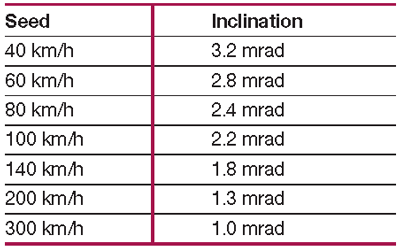
Table 1
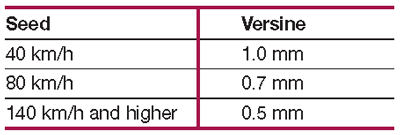
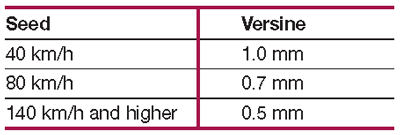
Table 2


Table 3


Table 4
References
- www.esveld.com
- Global Railway Review, Industry Focus 2008
- Steenbergen, M.J.M.M.: Wheel-Rail Interaction at short-wave irregularities, Dissertation TU Delft, ISBN 978-90-8570-302-0, June 2008
- www.pocketpccreations.com