Tunnel, vision: how a robotic and AI solution is transforming tunnel installation
Posted: 4 April 2025 | Alan Worsley, Lee Bateson | No comments yet
Lee Bateson, mechanical and engineering manager and robotics lead at Costain and Alan Worsley, design and project manager at Tunnel Engineering Services (UK) Ltd, share their insight into how integrating AI and data analytics to understand ways to improve productivity, efficiency and safety, could see the realisation of a fully automated system for tunnel services when this software is combined with other technologies, such as robotics and digital visualisation tools.
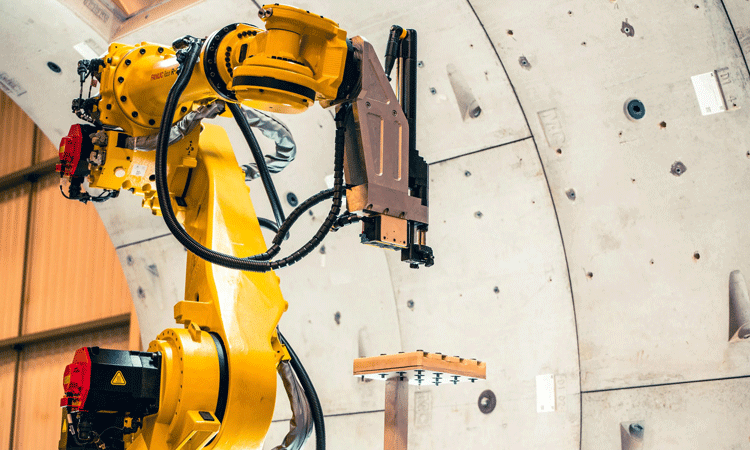
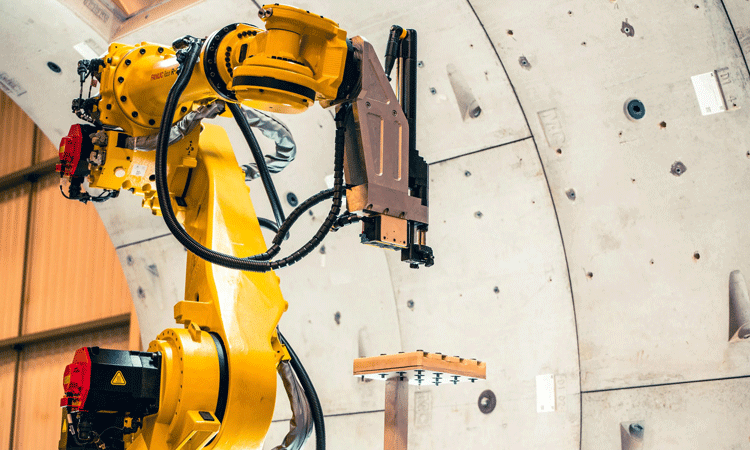
c: Andrei Zota
Tunnel construction and installation is arguably the most demanding civil engineering application for construction equipment and workers. A subterranean construction site requires the use of machines and technology that can be used in highly specific conditions, and are also able to navigate issues such as a lack of space and large volumes of materials.
Whilst the construction of tunnels is now highly automated through the increasingly widespread use of Tunnel Boring Machines (TBMs), the fitting out of tunnels with mechanical and electrical (M&E) services remains a predominantly manual process.
Whilst the construction of tunnels is now highly automated through the increasingly widespread use of Tunnel Boring Machines (TBMs), the fitting out of tunnels with mechanical and electrical (M&E) services remains a predominantly manual process. These processes have generally stood the test of time, but confined spaces present safety concerns for workers operating in those conditions. The work can also be time-consuming, and finding more efficient, safer processes remains a priority for any infrastructure project.
However, technology has simplified and expedited tunnel construction processes, and engineers are increasingly integrating AI and data analytics to understand ways to improve productivity, efficiency, and crucially, safety. When this software is combined with other technologies, such as robotics and digital visualisation tools, the ambition of a fully automated system for tunnel services could soon be realised.
This is what makes the recent successful trial of ATRIS – Automated Tunnel Robotic Installation System – so significant.
ATRIS is an integrated robotic and AI solution that can autonomously select brackets, locate where they need to be mounted along a tunnel wall, and install them. It has the potential to revolutionise the installation of mechanical and civil services in tunnels.
Earlier this year, a consortium of mechanical engineering, civil engineering and robotic automation industry leaders launched a prototype of ATRIS.
Earlier this year, a consortium of mechanical engineering, civil engineering and robotic automation industry leaders launched a prototype of ATRIS. Hosted and led by Manchester-based Tunnel Engineering (UK) Services (TES), the consortium includes the Manufacturing Technology Centre (MTC), experts in robotics and automation to spearhead the design and manufacture of the robot’s end effectors, and i3D robotics, which developed crucial visualisation software to allow for the robot’s precise navigation. Costain, along with VVB Engineering, provided industry knowledge and expertise in tunnelling and fit-out requirements.
The key objective of the 22-month project, part funded by Innovate UK’s Smart Grant, was to demonstrate and validate the real-life benefits of using robotics and AI to automate the installation of M&E services within a tunnel environment.
The project undertook a feasibility study to review the existing M&E techniques and find a robotised solution to enhance and innovate the manual installation methods currently used within tunnels. This confirmed the need for a robotic system, and from here, a scaled working prototype was developed.
The subsequent successful testing of ATRIS at the special-purpose TES facility – which sees two robots (colloquially known as ‘Pick’ and ‘Fix’) run through a full cycle of bracket installations within a purpose-built 4m diameter mock-tunnel – has paved the way for further implementation.
There are five distinct benefits its application will bring to the process of installing mechanical and civil services in tunnels.
The biggest benefit is the significant progression in safety standards that ATRIS can deliver. Prolonged use of power tools in the tunnelling environment can increase the risk of developing Hand Arm Vibration Syndrome. The use of ATRIS, and indeed robotics and AI more broadly, will reduce the number of access platforms at height in confined spaces, and improve safety at the tunnel workface. Once rollout reaches its potential, overall robotic automation using ATRIS will aim to reduce the number of construction operatives in the tunnel by 70%, redeploying these operatives to other roles with a higher degree of safety.
Carbon reduction
Like all sectors, tunnelling is targeting net zero requirements and is seeking long-term, sustainable methods of decarbonisation.
The rollout of the technology is expected to result in a 40% reduction of carbon emissions. This is due to a forecasted reduction in the use of construction plant, generators and diesel as a result of the ATRIS system. At the same time, fewer workers operating in the tunnel will reduce the volume of travel emissions to and from site.
Worker fatigue continues to be an industry-wide challenge and the physically demanding conditions in tunnelling can exacerbate issues such as low productivity. Automating processes has the potential to dramatically increase the speed of installation, with models estimating a 40% improvement in overall productivity, whilst fewer workers on site is also expected to produce a 30% reduction in installation costs for M&E systems.
ATRIS pioneers the use of visualisation software for precise navigation. By combining 3D vision and AI mapping, the robot has been taught to continually adapt its position and function, guaranteeing the precise, accurate placement of bolts on curved surfaces within tunnels. Creating this seamless interaction between robotics and the environment it operates in was a significant challenge from a software perspective. Overcoming these challenges required new learning and techniques including teaching the robots to learn seemingly simple tasks, such as how to avoid cross-threading the bolts that go into sockets.
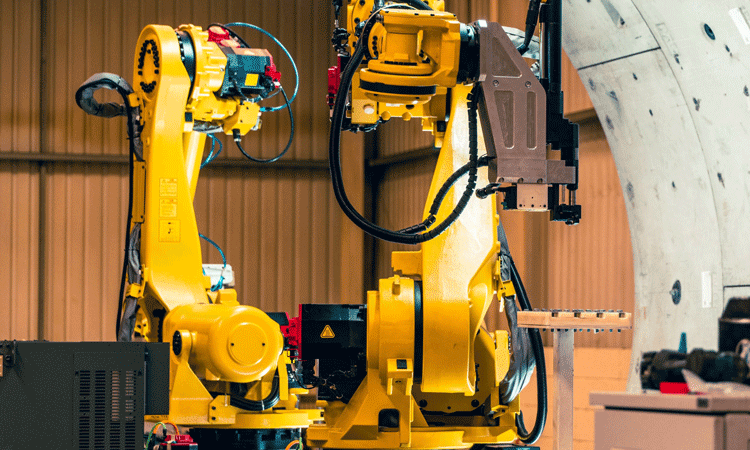
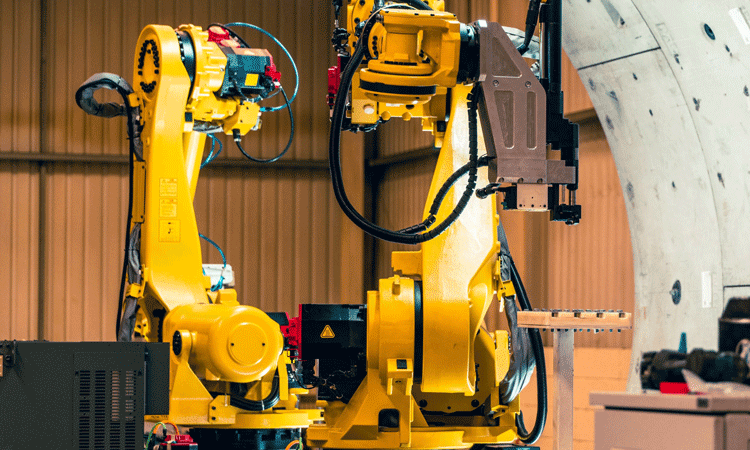
c: Andrei Zota
Future-proofing the workforce
All technology introduced into the industry should aim to complement the workforce. The rollout of ATRIS seeks to fulfil this objective by catalysing the upskilling of construction operatives at the tunnel workface. It will mark a significant step towards increased use of robotics in tunnelling, serve as an important proof point of how the sector is embracing the technology, and ultimately make it more attractive to future generations. It will allow more people to see the opportunities that could be realised for businesses, projects they’re delivering and the communities they’re serving.
Following the successful launch of the ATRIS prototype, all parties are working on ensuring its commercial viability and the eventual production of a system that can be deployed in tunnel construction for a variety of sectors including transport, water and energy.
But while ATRIS is geared towards increasing on-site productivity, the project is also developing technologies to find efficiencies off-site.
The consortium has successfully delivered a Digitally Assured Tunnel Assets Installation System (DATA-IS).
The consortium has successfully delivered a Digitally Assured Tunnel Assets Installation System (DATA-IS). DATA-IS will offer greater accuracy in the data gathering and recording for M&E fit-outs in a tunnel environment. It is the first technology of its kind in the industry and will use real-time data from ATRIS to digitally assure each bracket at the point of its actual installation.
Achieving technical assurance at the point of installation is a major development. Its use has the potential to dramatically speed up delivery and reduce costs traditionally associated with the return of major infrastructure projects to a customer, ultimately avoiding delays which have beset such projects in the past. The consortium is running a series of end-to-end demonstrations of ATRIS & DATA-IS with prospective project partners and customers.
It’s no secret the industry needs to be smarter in its use of AI and robotics to solve industry challenges. We’re still only scratching the surface, but the successful trials of ATRIS and DATA-IS collectively mark a watershed moment for the industry. The technology’s vast potential to solve perennial productivity shortcomings – testing has indicated that ATRIS can bring a 40% improvement – is no mean feat, and the rail and construction sectors should be taking note.
Perhaps most important of all, however, is the potential of the technology to provide both a new window of employment throughout the UK and a safer, more secure working environment – critical to the success of any infrastructure firm and its people.
Issue
Related topics
Artificial Intelligence (AI), Big Data, Digitalisation, Infrastructure Developments, Safety, Sustainability/Decarbonisation, Technology & Software, The Workforce, Tunnelling