Grinding and milling are essential to rail quality
Posted: 23 January 2009 | | 2 comments
Rail grinding helps to prevent the dangerous build-up of rolling contact fatigue, and also reduces running noise for line side communities. James Abbott, Technical Editor for Global Railway Review, assesses some developments and significant aspects of this important area of our industry.
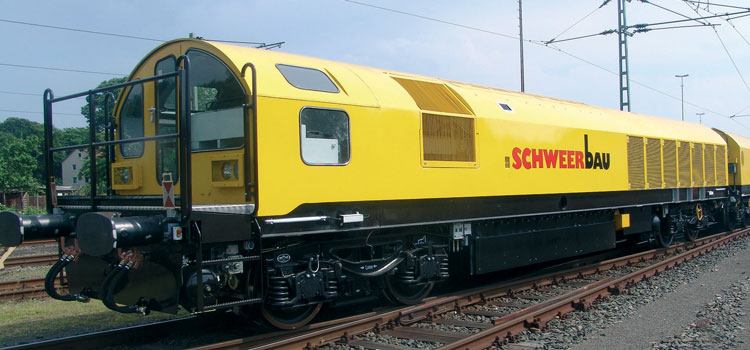
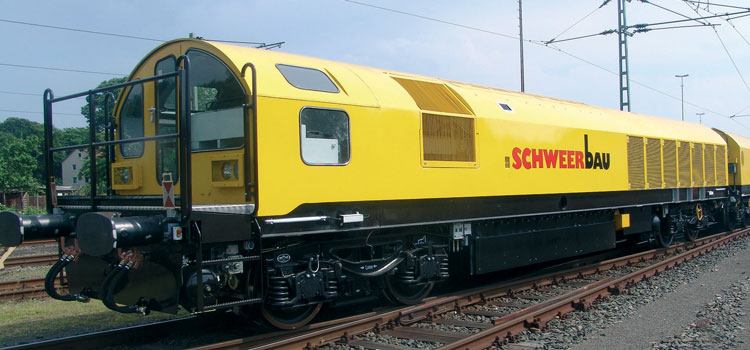
The SFU 04 milling machine from Schweerbau
The Hatfield accident in the UK in 2000 was a wake-up call for railway administrations the world over. The derailment of an express passenger train with passenger fatalities was shown to have been caused by rolling contact fatigue (RCF), in which tiny cracks in the rail head extended down into the body of the rail, eventually causing a break.
Statistics produced by the Federal Railroad Administration in the United States suggest that RCF was strongly implicated in 122 derailments, and may have been a contributory factor in a further 160 incidents, over the period 1995-2002.
As a result of statistics like these, RCF is widely accepted as a problem that has to be managed by railway administrations. Doing nothing is not an option: the UK ceased rail grinding operations a few years before the accident, and it is now accepted that this was not a wise decision. Grinding shaves off the top surface of the rail, removing the cracks before they have a chance to propagate down into the web and thus preventing rail breaks.
A study by the European Commission suggests that RCF management is a costly exercise, with a figure of €300 million mentioned for managing the problem each year on the European railway network. This total includes the activities of inspection, rail grinding, rail replacement and weld repair, along with the negatives of train delay and derailments when these do occur.
Clearly, this is a problem which deserves management time and railway administrations need to keep abreast of the latest technology if they are to minimise the cost of RCF.
Managing RCF
In a study for the National Research Council of Canada, Eric Magel, Peter Sroba, Kevin Sawley and Joe Kalousek say that “many factors interact to influence RCF” citing rail hardness, detailed wheel and rail profiles, and lateral and longitudinal wheelset dynamics among other factors. But they say that “RCF is particularly sensitive to wheel and rail profiles and inappropriate or uncontrolled profiles can completely mask effects of metallurgy.”
The researchers add that in the UK, the general experience has been that high strength steels are more prone to forming RCF – “a finding that can be explained by the high stress rail section employed and the failure of the hard steels to wear or flow to a lower stress shape.” It has also been the British experience that if the rail is initially ground to a lower-stress shape, then it is much more resistant to RCF than the softer steels. This emphasises the importance of initial grinding of rails.
The Canadian researchers explain the significance of the ‘Magic Wear Rate’, the process of removing just the right amount of the rail surface to prevent crack propagation. “In track with RCF, the natural wear rate should be supplemented by grinding to achieve the Magic Wear Rate”, they say. The Magic Wear Rate is generally higher in curves than on straight track, with North American experience on heavy tonnage lines showing that the lower rail in curves has to be carefully managed through grinding to achieve the Magic Wear Rate.
Speno at the forefront of innovation
Some years ago, Speno International started to investigate the possibility of detecting surface fatigue cracks during grinding. A joint development with Deutsche Bahn AG resulted in a recording system able to measure defect density and damage depth.
After intensive in-track testing with a prototype device, six Speno grinding machines have been fitted with the company’s ‘Headcheck Grinding Scanner’. The system allows operators to check the reduction of fatigue defects during each grinding pass and to document the achieved result with respect to metal removal of the fatigued rail surface. The system has entered commercial service with several European railways, including those in Austria, France, the Netherlands and Poland.
The advent of the ‘Headcheck Grinding Scanner’ is the latest in a long list of innovations from Speno. In the 1980s, the company introduced a grinding train with remote controlled tilting grinding motors. This was followed by the first switch grinding machine, the first on-board measuring equipment for the rail cross section and the introduction of dust collection systems.
Speno is working with railway infrastructure managers on ways of dealing with specific rail defects and problems generated by heavy rail traffic. The firm is participating with the European research project ‘Innotrack’, which is bringing together experience and know-how from several railway organisations and the industry.
Speno is chairing the working project 4.5 ‘Rail Maintenance’ within the Innotrack programme. Information is being prepared for infrastructure managers on how to establish an appropriate maintenance strategy that will combat rolling contact fatigue, including suggested target rail profiles.
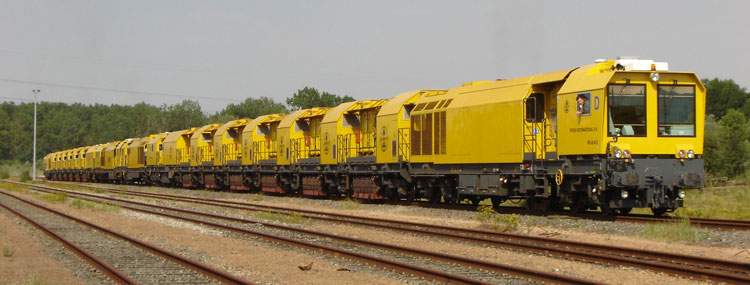
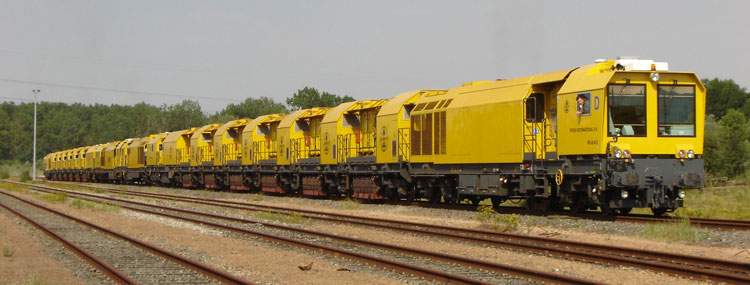
Speno’s 2 xRR 48 M synchronized grinding trains working in France
Speno has been designing, building and operating rail grinding trains for the last 40 years. The company says its 30 rail grinding units in operation in Europe in 2009 comprise by far the largest fleet of grinding trains under one roof. “Long time experience in design, manufacturing and exploitation of grinding trains provides excellent performance, combining high output per shift and a consistently controlled quality day-by-day”, says Speno.
Speno recognises that routine grinding work today comprises of:
- Initial grinding of new rails, cyclical preventive and corrective grinding
- Application of special profiles to reduce high rail wear, mitigate gauge corner fatigue and improve running behaviour, including gauge widening
- Anti-noise grinding to minimise noise generated by rail traffic
The execution of one-pass-grinding using heavy-duty machines is currently implemented on high speed lines. “Experienced and knowledgeable staff are very important”, says Speno. The firm says the trick is not only to remove a certain amount of metal in one pass, but to assure the minimum metal removal rate.
New Linsinger milling vehicle for LRTs
Also aimed at the light rail sector is the SF 01 F Rail Milling Train from Linsinger of Austria. This first came out a year ago, early in 2008, and the company says it has achieved some very good results on light rail systems in Asia.
The concept of profiling the rail with milling by single pass processing is already well known from earlier machines from Linsinger, and the SF 01 F builds on this experience. Linsinger says its rail milling technology combines rail milling and grinding in a single operation with a high degree of accuracy and performance, adding that light rail systems can achieve a significant reduction in maintenance costs by use of this technology.
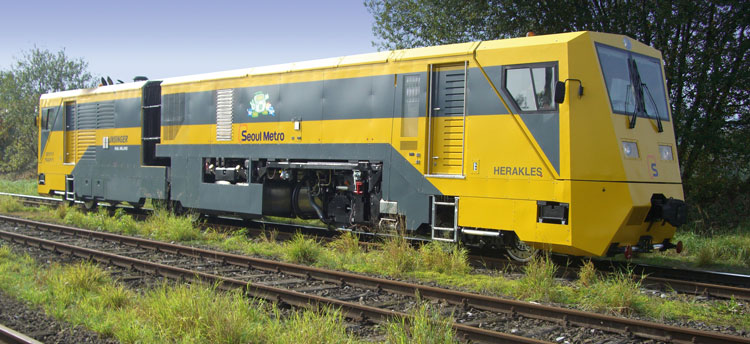
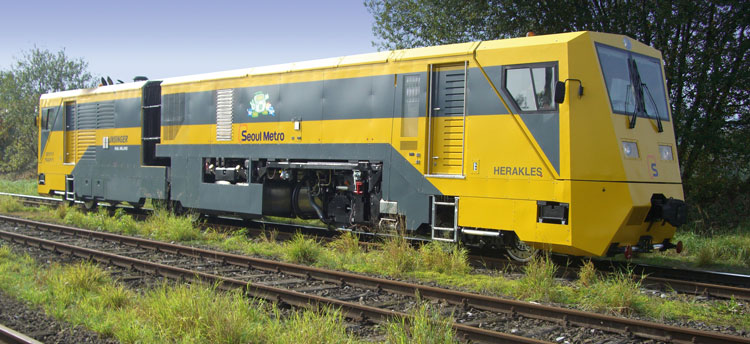
SF 01 F Rail Milling Train from Linsinger
Linsinger are proud to point out that the advantages of the SF 01 F include the following:
- Single pass processing of the complete rail surface
- Environmentally friendly: no emissions, no dust, no dirt
- No flying sparks, no risk of fire
- Safe and smooth operation
- Dry processing
- Very high output
- Controlled metal removal rates
- Any required rail profile, with high surface quality
- Noise reduction of rolling stock
- Low running costs
Issue
Related topics
Milling & Grinding, Safety, Track/Infrastructure Maintenance & Engineering
When “new ” rail is mentioned for grinding, does this include new rail just rolled and installed in a commuter rail operation? Or new rail installed and operated over for a determined amount of time/trains tonnage? We plan on installing new 136Lb. rail then put track in service. Is there any prescribed time before grinding should be performed. Tangent track thank you
I am interested to know from the author about a comparative of grinding versus milling and guiding factors for the selection.