Rail steel grades in track
Posted: 1 August 2013 | | No comments yet
Since 2002, track strategies at the Austrian Federal Railways (ÖBB) have been based on life-cycle cost calculations1. These basic strategies have been adopted due to new technologies – for example the use of under sleeper pads, changing price levels, and the phenomena of rail contact fatigue2 (RCF).
The basic data for defining life-cycle cost based strategies are so-called standard elements. These standard elements are track sections with a set of defined parameters (traffic load, alignment, type of super-structure, dewatering system, sub-layers, sub-soil quality). For all relevant standard elements, working cycles have been worked out defining the demand of maintenance for the entire life-cycle and the economic service life. These cycles exist for different types of super-structure taking into account rail profile, rail steel grade, and the type of sleepers as there are concrete sleepers with under sleeper pads, conventional concrete sleepers and wooden ones (see Figure 1).
These standard elements are cross-checked with real track sections facing these parameters and with the information provided by a data warehouse showing the deterioration function of track over time based on time periods of 12 years.
Since 2002, track strategies at the Austrian Federal Railways (ÖBB) have been based on life-cycle cost calculations1. These basic strategies have been adopted due to new technologies – for example the use of under sleeper pads, changing price levels, and the phenomena of rail contact fatigue2 (RCF). The basic data for defining life-cycle cost based strategies are so-called standard elements. These standard elements are track sections with a set of defined parameters (traffic load, alignment, type of super-structure, dewatering system, sub-layers, sub-soil quality). For all relevant standard elements, working cycles have been worked out defining the demand of maintenance for the entire life-cycle and the economic service life. These cycles exist for different types of super-structure taking into account rail profile, rail steel grade, and the type of sleepers as there are concrete sleepers with under sleeper pads, conventional concrete sleepers and wooden ones (see Figure 1). These standard elements are cross-checked with real track sections facing these parameters and with the information provided by a data warehouse showing the deterioration function of track over time based on time periods of 12 years.
Since 2002, track strategies at the Austrian Federal Railways (ÖBB) have been based on life-cycle cost calculations1. These basic strategies have been adopted due to new technologies – for example the use of under sleeper pads, changing price levels, and the phenomena of rail contact fatigue2 (RCF).
The basic data for defining life-cycle cost based strategies are so-called standard elements. These standard elements are track sections with a set of defined parameters (traffic load, alignment, type of super-structure, dewatering system, sub-layers, sub-soil quality). For all relevant standard elements, working cycles have been worked out defining the demand of maintenance for the entire life-cycle and the economic service life. These cycles exist for different types of super-structure taking into account rail profile, rail steel grade, and the type of sleepers as there are concrete sleepers with under sleeper pads, conventional concrete sleepers and wooden ones (see Figure 1).
These standard elements are cross-checked with real track sections facing these parameters and with the information provided by a data warehouse showing the deterioration function of track over time based on time periods of 12 years.
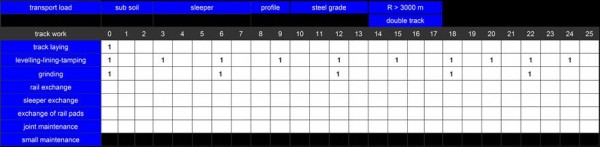
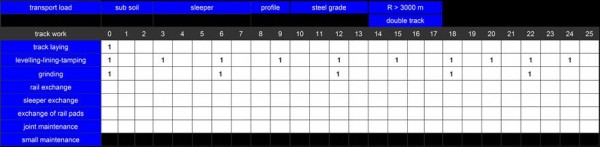
Figure 1 Working cycle for a specific standard element (no RCF taken into account)
Within the basic strategies (1998-2001) RCF was not taken into account as it was not a real problem in Austria in those days. Therefore the calculations resulted in a track investment strategy using the standard steel grade R260 for track sections with radii bigger than 500m, while head hardened rails R350HT were proposed in smaller radii targeting an increase of rail service life by reducing the side wear of the rails.
Due to the density of the network, heavier traffic loads and more powerful traction units using higher slip, the phenomena of RCF, mainly head checks, increased within the entire Austrian rail network. Research carried out by rail producers, German Railways and ÖBB3 depicted the relationship between rail steel grade and the growth rate of head checks. At the same time the tests showed the different appearance of head checks due to different radii.
The tests were carried out with rail steel grades R200, R260, and R350HT. R200 was tested to check if the head checks would be worn out automatically due to this soft rail steel grade. However, this expectation did not come true. The measurements showed the softer the rail steel grade the deeper the cracks and the wider the distances between the cracks. The tests proved the growth rate (given in mm per 1,000,000 gross tonnes passed) of the cracks to be doubled for R260 compared to R350HT. Moreover, the test showed that head checking is a phenomenon for radii wider than 500m with a maximum at radii of 1,500m and very low importance for radii of more than 3,000m.
As the operation density, the power and the slip of the rolling stock cannot be influenced by the infrastructure and three possibilities remain to react on head checks. Firstly, to change rails more frequently is a very uneconomic solution and should therefore be avoided wherever possible. Secondly, is to implement higher steel grades in order to reduce the growth rate of head checks and thus the demand on grinding. And finally, to implement cheaper standard rails R260 but to intensify grinding.
The remaining two possibilities are either to invest additional money into higher steel grades or to go for more intense grinding. This is a pure economic question. As head checking depends on the traffic load, the radii standard elements for different rail steal grades and different radii had to be developed taking the respective grinding demand into account. However, there is one more input data required: the maximum accepted crack depth. In case of the discussed analyses this threshold value was set to 1mm. This assumption defines the number of grinding passes and thus the costs of grinding. The rail steel grade and its growth rate of head checks allows calculating the demand of grinding. But grinding is executed not only to reduce RCF but due to other reasons as there are corrugation waves in straight sections and corrugation of inner rails in sharp curves. Furthermore, depending on the alignment, rails need re-profiling – a possibility to steer the equivalent conicity and thus the riding behaviour of rolling stock. Last but not least, some grinding might be executed to reduce the noise level. In Austria, new rails are ground in any case within track relaying as well as after rail exchange.
The life-cycle costs for these working cycles can be figured out in calculating all track work described within the working cycle. The service lives within the different standard elements are, in general, long but nevertheless differ. The dynamic average annual cost were calculated, taking a rate of interest of 5% net into account. This allows choosing the option with the least annual costs in order to formulate an investment strategy (see Figure 2).
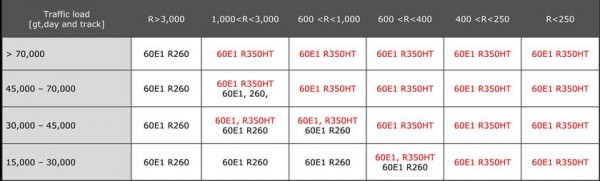
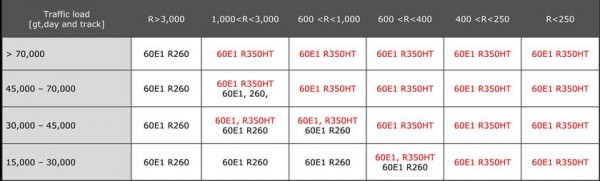
Figure 2 Rail Investment Strategy taking head checks into account
The results clearly show the new fields of implementation for higher steel grades on heavy loaded sections, while sections facing little transport volumes remain areas for implementing standard steel grade R260 in radii bigger than 500m. In some areas, both rail types are mentioned, showing that the cost differences can be neglected in these cases.
However, it must be stated, that an investment strategy must always be based on the assumption of the execution of the demanded maintenance. If this maintenance would not be executed for one reason or other, the investment strategy might be foiled.
Unfortunately there keeps some space even for the first option, to change rails more frequently. In the past grinding was executed mainly in sharp curves to reduce the corrugation of the inner rail. This maintenance action was required in order to reduce the accelerations and thus the wear of the fastening system and the sleepers. On the other hand, little grinding was executed in bigger radii or straight sections. Therefore there may be rails in service having not faced the required grinding actions taking head checks into account. This may lead to crack depths of more than 1mm. The maximum crack depth in regard to safety is approximately 2.3mm. Therefore rails showing crack depths close to this limit need to be exchanged. However, in executing the new rail strategy this demand must disappear in future.
Currently, similar track tests are carried out for bainitic rails showing very promising results. However, these tests have not yet been finished and therefore are not yet incorporated into the rail investment strategy.
Head checks are increasing the life-cycle costs of track, either by additional investment into higher rail steel grades or in increasing the demand of grinding. On the other hand the effect of more grinding has a positive impact on track quality. Maintenance always tries to minimise the dynamic forces in track in reducing all kind of track failures as these failures lead to additional dynamic forces. For example, tamping is reducing the track errors with wave lengths longer than 3m. So grinding is reducing the dynamic forces caused by corrugation. Executing tamping and grinding within some weeks must minimise the dynamic forces altogether. As track deterioration is not linear but can be described by an exponential function, a minimum level of dynamic forces in track must lead to its least deterioration.
Therefore, Austrian Federal Railways implemented the so-called ‘integrated main – tenance’ bundling tamping and grinding in a short period of time, sometimes even in the same track possession. The maintenance action itself is caused by a tamping demand and tamping is executed first, the grinding cycle is fitted to the tamping cycle. In general this does not mean additional demand of grinding, as grinding is executed more frequently anyhow, compared to the past. After tests started in 2003 this strategy has already been implemented for the new high-speed lines since 20114. The results will be analysed in detail and if expectations will be fulfilled this maintenance action is going to be spread over more track sections in future.
References
1. P. Veit: Projekt Strategie Fahrweg ÖBB, zev rail 09/2004
2. P. Veit, St. Marschnig: LCC Gleise Aktualisierung Gleise, unpublished; 2010
3. G. Girsch, R. Heyder: Head-hardened rail put to the test, Railway Gazette International; 2004
4. M. Wogowitsch: Stopfstrategie der ÖBB, unpublished; 2011
Biography
Peter Veit is Head of the Institute for Railway Engineering and Transport Economy at Graz University of Technology in Austria. He studied civil engineering and economics in Graz and started working at the Institute in 1987. In 1991 Peter graduated to Doctor of Technical Sciences and finished his habilitation 1999. In the 1990s Peter developed a life cycle cost model for the permanent way of railways. In cooperation with the Austrian Federal Railways (ÖBB) he formulated life-cycle cost based track reinvestment and maintenance strategies. Peter was a member of the ÖBB from 2000 to 2002 when he was asked to implement these new strategies. After being Associate Professor in Graz from 2002 to 2010, Peter was appointed to a professorship in June 2010. His institute cooperates with European infrastructure companies as the Austrian, the Swiss and the Norwegian one as well as the Austrian railway industry.