Consistent and positive ballastless track systems
Posted: 26 November 2007 | | No comments yet
The international increase in transportation volume throughout the world over recent years has led to a revival in railway traffic. This has in turn resulted in an appreciable number of technical innovations and an enhancement in railway technology in the areas of rolling stock, train control and track engineering.
One example of such developments has been the establishment of ballastless track, not only for niche applications, but also as a standard product alongside conventional and more
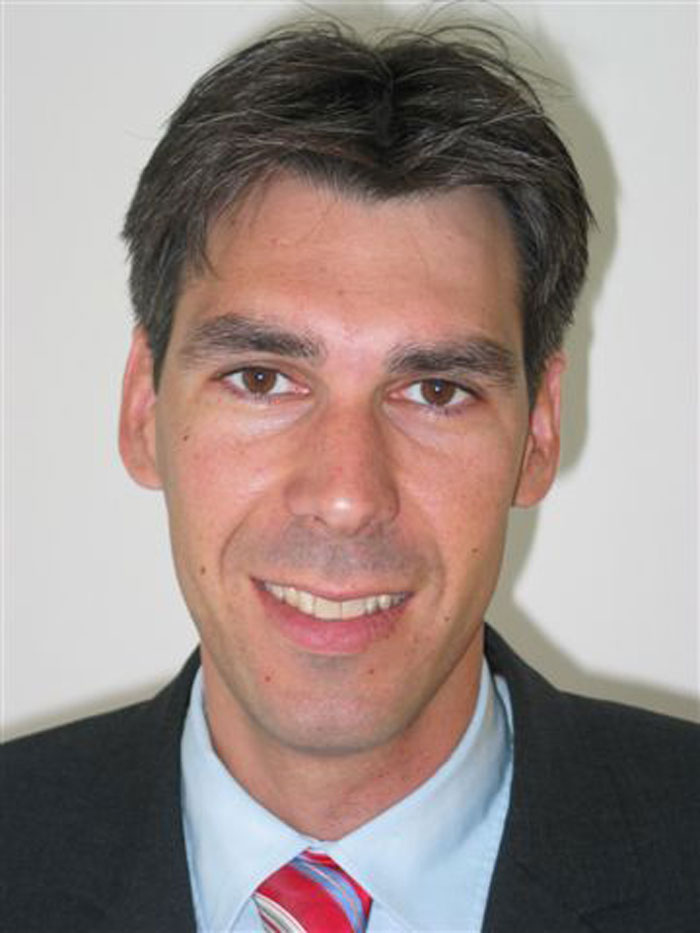
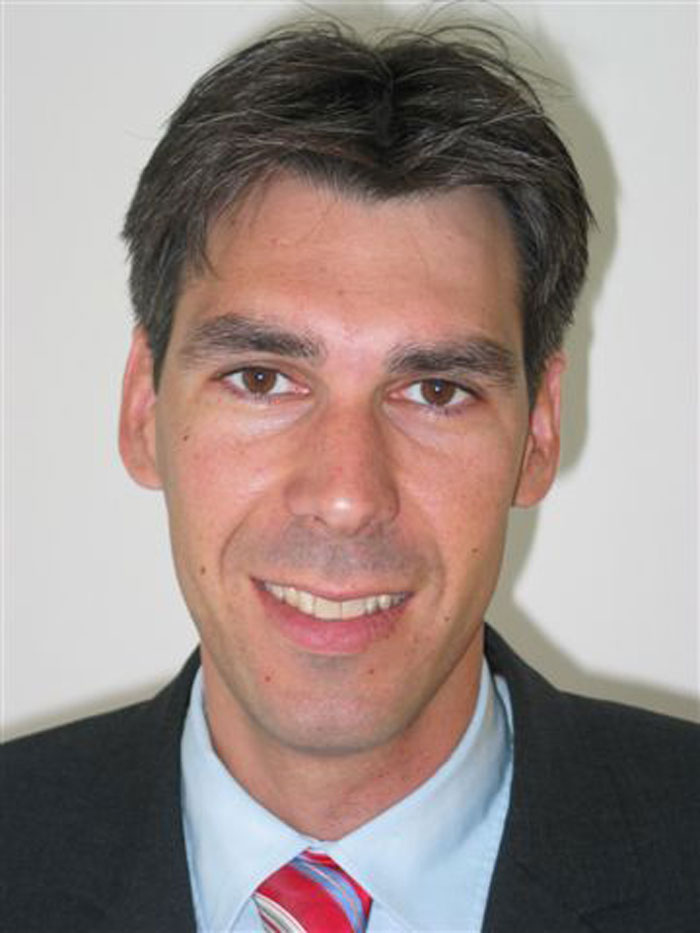
Jens Kleeberg, General Manager for Track Design, RAIL.ONE International GmbH
innovative ballasted tracks. Throughout the world today, new track projects and infrastructure expansions are being planned and engineered from the very beginning as ballastless track systems, which have proved to be safe, reliable and cost effective.
The RAIL.ONE Group (formerly ‘Pfleiderer track systems’) was involved from the earliest days in a leading role for the development of ballastless track systems for high-speed, heavy-haul and commuter traffic. Recently, the company has succeeded in profitably exploiting its experience in numerous projects for various countries and railway authorities.
This article provides an overview of the achievements of RAIL.ONE engineers during the planning and official-approval stages and also of the difficulties involved – with an example of a project in northern India.
The project – Udhampur Srinagar Baramulla Railway Link (USBRL)
The most ambitious railway project currently underway in India is the connection of the Kashmir region to the area at the foot of the Himalayas and the rail lines ending there that lead to Delhi and other metropolitan areas. The line is 290km long and runs through topographically very difficult terrain. This calls for the provision of numerous civil constructions such as bridges and tunnels that can withstand the extreme demands placed by climate changes and earthquakes.
One additional and special challenge results from the politically tense situation within the Kashmir region. A unique monitoring system has been planned for this line to prevent terrorist-motivated attacks. In addition to many TV cameras and barriers, the security system also includes the construction of ballastless track in five tunnels with a total length of approximately 10km. One purpose of the ballastless track is to reduce to an absolute minimum any access by unauthorised maintenance staff who are considered security risks. As a result, it is hoped to achieve a maximum of security against potential attack. Now, after the award of the contract for planning and construction of the ballastless track to a German-Indian consortium, RAIL.ONE plans to implement the line on the basis of its RHEDA 2000® ballastless track system, in collaboration with its Indian partners IRCON International Ltd. and the Patil Group of Industries.
The contract
The stated consortium is responsible for planning – especially for approval procedures and preparation of construction drawings and for construction of the ballastless track for approximately 10km in five tunnels, including delivery of the bi-block concrete sleepers required. Within the consortium, RAIL.ONE performs all planning tasks, up to and including official approval of the system and its components by the local Indian authorities. RAIL.ONE, together with a local producer of sleepers – the Patil Group of Industries – is furthermore responsible for production and delivery of the necessary bi-block concrete sleepers, produced in a plant set up exclusively for this purpose near Jammu, in India. The Indian construction Group IRCON International is responsible as prime contractor for execution of construction of the RHEDA 2000® system. Within the context of the project, furthermore, IRCON also took part in the planning and construction of numerous bridges.
Planning and official approval of ballastless track systems outside Germany
With the exception of a number of European countries and Japan, ballastless track systems have been installed only to a limited extent. In addition to the lack of practical experience, an additional difficulty is the fact that there are only very few accepted specifications and regulatory frameworks for the construction of ballastless track. This especially represents obstacles for official approval of such track systems, since authorities often expect that ballastless track systems should fulfil alternative stipulations from the field of conventional track construction and concrete engineering. These expectations, however, do not harmonise with the actual character of these innovative track systems – or are in actual contradiction thereto.
Furthermore, ballastless track systems must often be examined and approved by various and different public offices. Bridge engineers are frequently responsible, for example, for approval of the concrete track supporting layer – and railway engineers, for approval of the track components. The interfaces resulting from this situation often require additional documentary evidence of conformity that is usually extraordinarily difficult to provide and that have no relevance to actual practice, since the ballastless track acts as a total system.
In official approval of an existing, proven system such as RHEDA 2000®, the methodology of the so-called cross-acceptance procedure is principally advantageous. Cross acceptance enables official approval of an existing, proven system on the basis of evidence of conformity provided to show conformity only with those requirements that are different from already existing official approvals. The first step is therefore to compare the specifications of the current project with those on which the original approval had earlier been based, to establish any relevant differences. Achievement of approval for a current project requires only evidence to show conformity with the additional or differently formulated requirements posed by the present project.
Unfortunately, cross-acceptance procedures are recognised only in very few cases by public approval authorities within Europe and by even fewer outside Europe. This is primarily a result of the fact that, as mentioned above, there are practically no uniform international bodies of regulations for ballastless track systems. Frequently, authorities refuse to accept the regulatory framework on which the existing official approval had originally been based – which means that the system is formally considered to be a new development.
For new official approvals, it is advisable, before preparation of the documented evidence of conformity, to coordinate with the responsible examining authorities as to which criteria must be checked and in which manner. Otherwise, the considerable danger exists that the evidence will not be accepted because it does not satisfy expected standards. Especially for pilot projects, it is therefore advisable to elaborate for the investigating engineers, the special criteria of a ballastless track system – i.e., in the advance stages of a project and with acceptance of increased costs arising from meetings, explanatory reports and often also inspection tours of existing rail lines. It is possible only in this way for planning engineers as well as approval engineers to achieve a level of knowledge that can serve as sufficient basis for collaboration in the sense of mutual trust.
After achieving official approval, the track design must be presented in a form that allows the construction company to install the system on the construction site. For foreign projects, the construction-document phase as well must be adapted to local customs. Later in this article, salient differences here will be covered in greater detail. In general, however, representation of the entire line has proved to be of less concern than increasingly expected detailed depictions showing the complexity of individual track components. This means, above all, that details such as transitions, connections and other interfaces must be shown clearly and at the required scale. In comparison, the usual line sections can be explained with only a few cross-sections and views.
Planning of the RHEDA 2000® ballastless track system
Point of departure
The RHEDA 2000® ballastless track system was installed for the first time in India in 2006, on a rail-station track section approximately 500m long in Bhubaneswar, in the south of the country. The construction documents prepared for this project and the public approval provided, by no means coincided with Indian requirements for planning of a mainline track. As a result, there was practically no reference basis for later ballastless track systems in India. In addition, neither the bi-block concrete sleepers nor the highly elastic System 300-1 rail-fastening system by Vossloh accorded with specifications for state-of-the-art in India and likewise required discussion within the framework of the overall process.
For the Kashmir project, the track was intended to be installed in five single-track tunnels with lengths of 1 to 2.5km. At the time of track planning, the tunnels were already completed, but had been designed for ballasted tracks. It was therefore no longer possible to modify or otherwise adapt the tunnels. The tunnels had been constructed on the basis of mining technology, in an inverted ‘U’ cross-section. The floor of the tunnel was poured as a type of lean concrete, onto existing rock or other sub-grade. Additionally, numerous IPB beams were installed laterally into the tunnel floor, at intervals of 1 to 3m, for stabilisation of the tunnel cross-section. The track planning team did not have access to tunnel planning documents; it obtained only longitudinal and lateral cross-section representations, as well as a local inspection tour before award of contract. One special challenge that proved to be a major problem during the course of the project was water management and drainage in the tunnel. Deep drainage was not provided: tunnel designers intended for the water to collect on the tunnel floor and to drain out to the tunnel exit along the natural tunnel slope.
Planning
At the beginning of the approval process, it is initially necessary to clarify which parties will be called in for the approval procedures and which requirements must be satisfied. In India, the Research Design and Standards Organisation (RDSO) is responsible for such approval actions. This institution, however, does not include a department for overall track systems. Rather, it is broken down into a department for track components (e.g., rails, rail fastenings, sleepers, etc.) and a department for track substructures (e.g., tunnels, bridges, earthworks, and embankments).
Ultimately, the project dealt with two offices; one for the track components, and another for bridge construction for approval of the concrete components (e.g., the concrete track supporting layer). This dual organisation complicated the approval process significantly, since these two departments operate in accordance with different specifications and dimensioning criteria. It was consequently necessary to prepare two practically independent sets of approval documents, which required mutual, overall harmonisation. For the track components, it was fundamentally possible to resort to European standardisation, with the result that the approval authorities accepted existing research and test reports as basis for their approval. Additional documentation in verification of requirements was requested only for the sleeper shoulders of the System 300-1 rail-fastening system, which were slightly higher than for the W14 track. Furthermore, it was expected that the rail stress in the transition area between the ballasted and ballastless track would be investigated. For the ballastless system, the authorities required evidence that no significant additional effects would arise in the rails that would require the application of a rail expansion joint.
Approval of the concrete track-supporting layer proved to be considerably more difficult. Here, it was expected that documented verification would be provided that a concrete track would remain safe and reliable over a period of 100 years – under consideration of Bridge Standards<sub>1, 2</sub> as prepared by the RDSO, and of the safety concepts for bridges set forth therein. The application of these bridge standards to railway tracks entails two disadvantages. Firstly, confirmation is required that cannot be provided without artifice for a track that in fact has a technically effective design. Secondly, this approach neglects documented evidence of conformity essential for the permanence of a ballastless track.
In view of the many standards and exception solutions to be considered for the project, the initial step here was preparation of a new complex of standards to be applied to this project; the so-called ‘Design Specifications’. The fundamental contents of Indian bridge standards were incorporated into these specifications and were supplemented by coordinated processes for documented evidence that would otherwise be difficult to provide. Also, parts of these supplements were essential criteria for ballastless tracks, such as those required in the relevant German standards<sub>3</sub>. Preparation of these ‘Design Specifications’ proved to be highly effective, since numerous insights from Indian standards and from ballastless-track technology were exchanged among the project participants, in constructive collaboration beginning well in advance of the design process. This procedure is by all means highly advisable for other projects as well, since it extensively prevents unproductive basic discussions during the further course of the design process that could endanger on-time completion.
In the following, two fundamental criteria will be explained in greater detail. These criteria have been shown to lead to extensive discussions in all foreign track projects and for the approval of ballastless track systems abroad. By application of the process described above, it is possible to handle such discussions in a more controlled manner.
The criterion for a maximum permissible crack width of 0.5mm, as defined in AKFF3, conflicts, without further elaboration, with practically every normal standard for reinforced-concrete components. It is also not in agreement with the Indian bridge standard that allows a maximum of 0.2mm. Numerous expert presentations made by RAIL.ONE engineers and concrete technologists, however, succeeded in confirming that the two criteria are not entirely contradictory, after more detailed consideration of the definitions involved. These definitions included the following: design and actual values, the location and techniques of measurement, and the selection of additional requirements to be satisfied by the concrete mix design and the concrete cover. Above all, however, this approach showed that the required permanence of the respective track components could satisfactorily be achieved with application of both sets of criteria.
A second example involved stipulation in the ‘Design Specifications’ of the procedure to be followed in confirming the permanence of the concrete layers, by verifying conformity with the permissible tensile (and compressive) stresses in concrete. Here as well, it was possible to achieve permission for a deviation from the Indian Bridge Code: i.e., because here – as is usual for bridges – it was shown to be permissible to transfer the flexural stress exclusively by appropriate reinforcement. Only in such a way was it possible in this project to preserve the basic principle of the ballastless track system, with its load-distributing slab and its crack-limiting reinforcement. On the basis of careful handling of the above-stated details, it was ultimately possible to achieve preliminary approval of the RHEDA 2000® system, analogous to the design as it had already been satisfactorily implemented in many earlier processes.
In the area of the tunnel floor, however, it was discovered during the course of project execution that there were significant deviations from original assumptions with respect to stability and water management. There were, for example, numerous leaks at which great quantities of water entered though the tunnel floor into the tunnel itself. This situation gave rise to serious doubts as to the stability of the tunnel floor and the overall structure. Finally, RAIL.ONE succeeded in convincing the customer to have the dimensioning and construction of the tunnel investigated by highly qualified European experts – an examination that has not yet been concluded. Although this investigation was not part of the contract for RAIL.ONE, and did not constitute the core areas of track work, preservation of the reputation of RAIL.ONE as a comprehensive and competent partner in all matters of a track project demanded that these issues be properly addressed.
Conclusion
RAIL.ONE has by now developed and applied numerous ballastless track systems for mainline and urban transport. On the basis of the consistently positive operational experience gained with its systems in Germany, RAIL.ONE has increasingly succeeded most recently in having these systems approved and in implementing them in foreign countries as well. As a result of its collaboration with many European and Asian approval authorities, public offices, and railway organisations, RAIL.ONE is furthermore in a position to realise the planning of a railway track system, up to and including official approval, within stipulated time-schedules and budgetary constraints. In addition to offering high-quality track technology, RAIL.ONE is therefore able to provide a service that reduces to a minimum the approval risks associated with application of an innovative track system. The RAIL.ONE portfolio profile is rounded off by consulting services within track technology: e.g., for tunnel and bridge design, which can be additionally rendered under prime contractorship by RAIL.ONE in collaboration with its partners of long years’ affiliation.
References
- Indian Railway Standard; Code of Practice for Plain, Reinforced, and Prestressed Concrete for General Bridge Construction (Concrete Bridge Code); Government of India / Ministry of Railways, Research Designs and Standards Organisation; 2003
- Indian Railway Standard; Rules Specifying the Loads for Design of Super-Structure and Sub-Structure of Bridges (Bridge Rules); Government of India / Ministry of Railways, Research Designs and Standards Organisation; 2005
- Anforderungskatalog zum Bau der Festen Fahrbahn [Catalogue of Modifications for Construction of Ballastless Railways]; Fourth Revised Edition; 01/08/2002