Driving DB forward with superior rolling stock
Posted: 6 June 2007 | | No comments yet
Deutsche Bahn AG’s €30 billion core business consists of mobility services around railway transportation as well as a worldwide network of logistics in freight including rail business in Europe. In addition, DB operates a network of approximately 35,000 track-kms and offers further services such as station management, heavy maintenance and energy-supply.
Deutsche Bahn AG's €30 billion core business consists of mobility services around railway transportation as well as a worldwide network of logistics in freight including rail business in Europe. In addition, DB operates a network of approximately 35,000 track-kms and offers further services such as station management, heavy maintenance and energy-supply.
Deutsche Bahn AG’s €30 billion core business consists of mobility services around railway transportation as well as a worldwide network of logistics in freight including rail business in Europe. In addition, DB operates a network of approximately 35,000 track-kms and offers further services such as station management, heavy maintenance and energy-supply.
The railway operators of the DB Group – Railion for freight, DB Fernverkehr for long distance and DB Regio for regional transportation – run almost 35,000 trains per day and own almost 18,0000 vehicles (Figure 1). Most of them are freight wagons, the rest are coaches, railcars, locomotives and, last but not least, 250 ICE trainsets for high speed services which operate up to 320km/h.
More than 300 other railway companies run another 6,000 trains a day on DB’s network. Competition in Germany’s railway business is intensive, but rail traffic in general and at DB is increasing well with also an increase shown in recent years of more rail traffic than on the road.
After restructuring of the German rail business in 1994, a huge investment programme started to reduce the average age of DB’s fleet. In many areas the average age of the vehicles has reached a very good level, only coaches and diesel-locomotives are still in need of initial reinvestment. Thus DB now is at the edge of the comfortable situation to reinvest according to average renewal.
In passenger transportation, the investment-programme of these last 15 years brought a change from traditional locomotive and coach trains to much more modern and fast diesel and electrical multiple units and thus a big change in the way of operating trains. The second general innovation introduced double deck coaches in regional transport, a success story transferred out of the very good experience of former Deutsche Reichsbahn. Today, more than 1,500 double deck coaches dominate regional transportation in Germany’s metropolitan areas. At the same time, the ICE fleet of DB Fernverkehr has grown from 60 to approximately 250 trainsets which now form the backbone in this business. ICE trains are mainly operated in Germany, but also into Switzerland, Austria, The Netherlands, Belgium and – starting on 10 June – to France. Soon, Diesel-ICE’s will run to Denmark.
In freight, multi-system electrical locomotives gain importance according to the rapid growth of the European cross-border transportation volume. By achieving approval for these locos – a partially incredibly difficult, political, time and money consuming process – DB is one of the pace makers of European standardisation in railway technology and operation.
Nevertheless, the European railway business is still far away from a sufficient level of standardisation. It is the key issue of the development of our fleet and purchasing strategy. Only by reducing the number of different rolling stock in our fleet as well as by standardisation of all relevant component interfaces in the railway system do we get the opportunity to reduce costs in every aspect and increase flexibility in operation and quality of the technical solutions. In addition, we need a further standardisation of the approval process with far reaching cross-acceptance. Physique is the same all over the world. Therefore, proofs of technical performance have to be valid all over the world. Today there is still a far too big range of interpretation that makes approval expensive, in respect of time and the cost incalculable process.
The industry in Europe has taken over some of the responsibility from the former national railway companies for designing reliable, highly available, easily maintainable and safe trains. This process of change is not yet fulfilled and is hard work because the industry has to:
- Overcome competitive borders and concentrate on performance as the key parameter for competition, not only for initial design, but for the whole life cycle
- Take over responsibility for the whole life cycle of its product. So far the railway operators are still much too involved in keeping rolling stock technically up to date
Therefore, Deutsche Bahn AG currently invests mostly into standardised platforms of the industry. The latest example is the new fleet of 320 EMUs for regional transport ordered in February 2007. Prices could be reduced remarkably, although these trains can be ordered in a big variety of standardised equipment and are prepared for easy refurbishment and redesign which usually becomes necessary after 10-15 years of extensive operation.
This kind of flexibility based on a common platform is one of the guidelines of our further investments. These will concern:
- 500 yard-locomotives (diesel)
- At least 200 diesel-locomotives for freight
- Further electrical locos for freight and regional transport
- A delivery lot of at least 500 double deck and single deck passenger coaches for regional transport
- Several hundred DMUs on a platform like the new EMUs for regional transport
- Approximately 100 new train sets for long distance traffic to replace the well known and successful InterCity-trains
- A big variety and great number of freight wagons
As rolling stock investments have a lifetime of at least 30 years, railway markets and business in Europe are changing fast. Since the railways have to promote and apply sustainable technology in order to keep their position as the most environmental friendly means of transportation our next purchasing activities are of strategic importance and offer a chance to set milestones.
In Europe, locomotives are already the most standardised vehicles in railway business. Therefore we are going to expect well proven, low cost and highly reliable locomotives offered by the industry. Wherever possible, the new locomotives – both diesel and electrical – will have to have common spare parts with our existing fleet of modern electrical locomotives in order to reduce costs for maintenance work and materials as well as for spare-parts-logistics. Of course the diesel-drives will have to fulfil future demands concerning noise, exhausts and energy consumption.
Future passenger coaches for regional transport will need to become less expensive and as flexible in equipment as the recently ordered EMUs. For short trains we are looking for an alternative solution to the high performance and therefore too expensive locomotives. This could become a motor-unit, combinable with coaches.
We intend to set the cornerstone for the platform of the next generation of ICE-trains with the new trains for long distance traffic. These must be fast, flexible, highly reliable and modern at lower costs than before. Of course these trains must be built on an industrial platform for approval in different European networks.
Purchasing freight wagons is in many aspects a very special subject. Freight transport is more than ever a cross border business with freight wagons running all across Europe. Competition is very intensive, both between road, waterways and rail as well as among railway operators themselves. Therefore cost effectiveness is by far the most important issue. Running gear, brakes, couplers and buffers of the freight wagons are standardised. Due to the increasing variety of goods to be transported on rail and to further integration of freight wagons into the manufacturing process of our clients, the specialisation of freight and thus of freight wagons drives their costs. A new initiative of functional and technical standardisation was started in order to be able to increase delivery lots. The result: lower prices per wagon as well as load-kilometres in relation to deadhead-kilometres. Another subject is technical and functional quality of freight wagons. There is a high potential for improvement.
This big purchasing programme for rolling stock is a chance but also a challenge for both DB and the manufacturers. With each contract we will prod the industry into further standardisation of their array of products and their interfaces to the supply industry. Progressing standardisation enables the manufacturers to promote competition between their suppliers by creating alternative solutions for each component. Thereby operators gain an advantage too: we will have alternative competing suppliers of spare parts, maintenance will be easier and obsolescence becomes less of a risk during the long life of our vehicles.
To promote this big change in railway technology we – together with SNCF, Trenitalia and UIC – participate in the EU-project MODTRAIN which aims for overall standardization of technical functions and interfaces. At the same time we need to restructure the railway operators´ standards and regulation process in order to be able to take an active part and to find a better way to cooperate with the industry and the European institutions.
Why do we need to cooperate between industry and railway operators?
Vehicles are not commodity but capital equipment. Therefore, development and innovation have to be part of a continuous improvement process and an integrated life cycle management. Exchange of know-how is a key issue of this life cycle management. The flow of know- how and experience needs to be guaranteed from operation and maintenance back first to development, design and manufacturing of vehicles and second to optimisation of the existing fleet. Because many partners are involved in this vehicle life cycle, the biggest challenge is to keep up the exchange of know-how between them: from clients to operators, from operators to maintenance-managers, from operators to manufacturers, suppliers and researchers.
At Deutsche Bahn AG, the ‘Purchasing and Technology of Rolling Stock’ unit is responsible for monitoring the technical performance and costs of DB’s fleet using key data, for organising this exchange of know-how and for managing the continuous improvement process both of the existing fleet as well as for purchasing new vehicles. The improvement process is one part of Deutsche Bahn AG’s story of going to the stock market. Soon DB will become a privatised company, fit for the liberalised railway, mobility and logistics market in Europe with even more drive to optimise business.
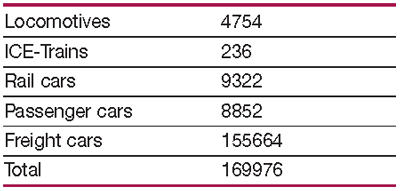
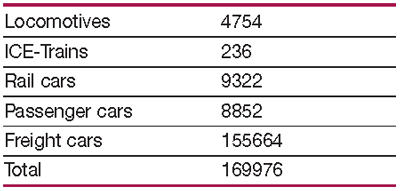
Figure 1: Rolling Stock chart of Deutsche Bahn AG (as at 31 December 2006)
About the author
Joachim Mayer has a Diploma in Civil Engineering of specialized traffic and studied at the Universities of Stuttgart and Zürich. Mr Mayer has worked for German Rail since January 1986 in many different positions for divisions including the Corporate Planning Division, the Test- and Planning Company for Maglev-Systems (MVP) in München, the R&D Centre in München and DB Systemtechnik. Since January 2005, Mr. Mayer has been Head of Rolling Stock, Technology & Procurement at Deutsche Bahn AG.