Thinking outside the box: how an innovative level crossing project encapsulates the future of rail
Posted: 6 March 2023 | Atkins | No comments yet
Rail is changing. While budgets tighten, the expectations of users are growing. To transform the rail industry into one capable of providing a frictionless future of low-carbon travel, we must refine the way we operate, and generate more from less. That’s why Atkins, a member of the SNC-Lavalin Group, in close partnership with Unipart Rail and Newgate (Newark) Ltd, set itself a real challenge to demonstrate that level crossing delivery timescales could be halved. Through an innovative and collaborative approach with real world applications, the result was the successful proof of concept of a cutting edge ‘level crossing in a box’ that can be designed, manufactured installed, tested, and commissioned in under 20 weeks.
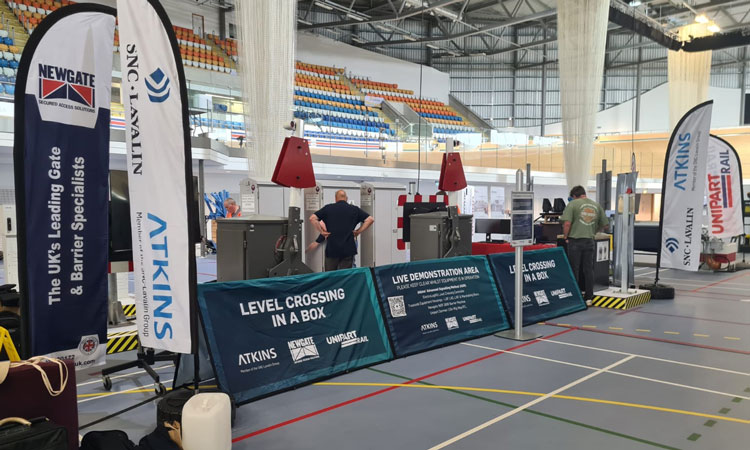
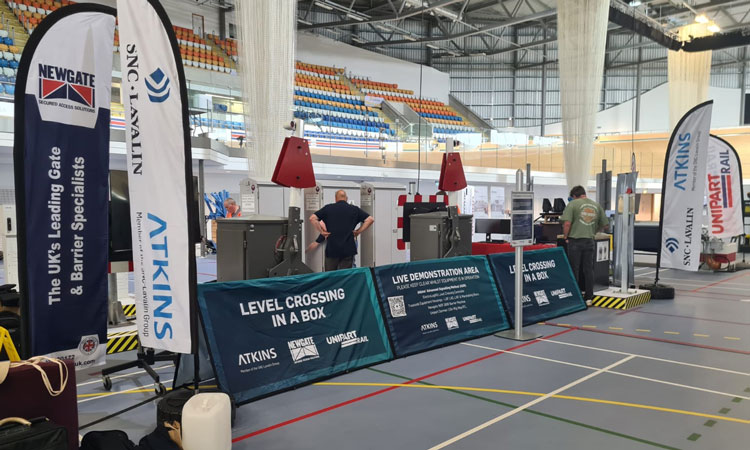
Set up of the level crossing demonstration at the Derby LXI event.
The future of rail is being driven by efficiency. A truly streamlined service demands we optimise our usage of the network, reducing disruption at every level, through design for reliability, improved construction techniques and minimising operational maintenance – to do things more quickly, more safely and more robustly. With growing budgetary constraints and rising expectations from passengers and customers, it has never been so important to do more for less. Yet those efficiency gains are increasingly hard to find and net zero is making the task of transformation ever more urgent.
The answer is to nurture a culture of collaboration and innovation. By encouraging creative problem-solving at every level, by exploring new methods of organisation and by building effective working relationships, we can overcome the technical obstacles to progress. That thinking underpinned our bold ambitions for the Rail Live and Level Crossing Innovation Day (LXI) events in 2022. Atkins, Unipart Rail and Newgate joined forces to form a collaborative project team to build a portable ‘level crossing in a box’ – a fully functioning level crossing barrier and Road Traffic Light (RTL) set-up, comprised of ‘real equipment’ operating from a custom-made control panel. The goal was to showcase a successful proof-of-concept. The result was proof that a determined vision and focus can deliver huge improvements to our methods and processes; something we all need to do to meet the challenges of the future.
Express delivery
In many ways creating the ‘level crossing in a box’ for the Derby LXI Day was a unique project. Alongside the technical barriers to designing, pre-testing, and installing a cutting‑edge, live system for customers on the day, there were a number of other unusual elements to the project. The team consisted of experts who had never met or worked together before, and the deadline was brought forward by one week during the planning phase to display the same proof‑of‑concept at the Rail Live exhibition.
The solution also included sourcing components, equipment, and specialist expertise from three businesses. A temporary space was needed to build and test the equipment, and a bespoke logistical operation was required to safely transport equipment to and from both display venues. To meet these challenges, we created a clear and cost-effective collaborative plan, informed by the marketing and technical expertise of all the partners, and agreed to utilise Unipart’s testing facility in Coventry to test the design solution.
Signal of intent
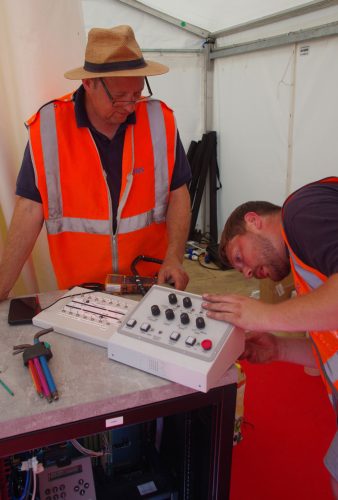
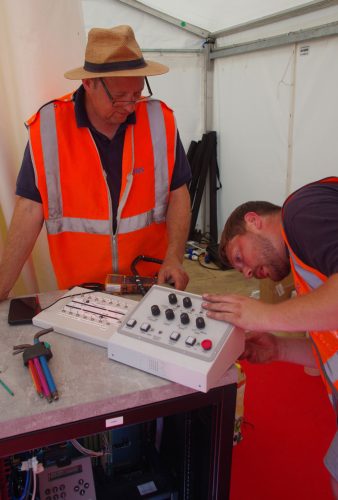
Colleagues assembling the remote control box for the level crossing demo at Rail Live – Andy Marsh and Ashley Shirt.
The events went as planned, successfully demonstrating the proof of concept. But it’s the lessons we learned throughout the design, construction and implementation processes that hold the true value and enables the real‑world improvements the team was seeking. By pushing to deliver efficiency savings across the entire project lifecycle, we reaffirmed where our industry needs to change, and showcased what the future of rail can look like.
First, collaboration can transform a project. Unlike a typical project with siloed responsibilities and different spheres of expertise, we were able to enact a holistic approach with our partners Unipart Rail and Newgate, sharing ownership of the whole task and encouraging cross-pollination of ideas. Through clear information sharing and joined up planning throughout the project, we developed effective and dynamic working relationships that contributed more than the sum of our parts. So successful was our collaboration that our three organisations are bringing this model of working to several other projects.
Second, modularisation demonstrated we can remodel how we undertake construction for railway infrastructure, learning from other industries’ best practice. The techniques employed enabled a reliable and repeatable construction process, reducing time on site (hence disruption to passengers) and the costs of rework and redesign. We will evolve modularisation by moving away from bespoke design to create a ready-for-site product. Software tools will then allow us to design in minutes rather than weeks, in turn allowing us to deploy faster and shorten projects. In setting up the ‘level crossing in a box’ in just under four hours, the team showed just how quickly it could be implemented on a real level crossing. That translates into real improvements in the way Atkins’ Advanced Signalling Method (ASM) can be implemented in future. We estimate that we can now reduce time on-site by up to 20%, causing less disruption to the network and reducing the safety risk to employees.
Lastly, we proved the considerable value of ‘off-site integration testing’ by discovering a previously unknown hardware failure during the off-site set up activities. Ordinarily this would only have been identifiable during the commissioning and would have typically led to hours of diagnosis and delay in the course of the ‘site testing process’. The off-site integration regime significantly helped refine the manufacturing process, feeding back critical functional information from a safe environment and creating a better end result for the installers, clients, and end users alike by reducing the time, cost and disruption of on-site work.
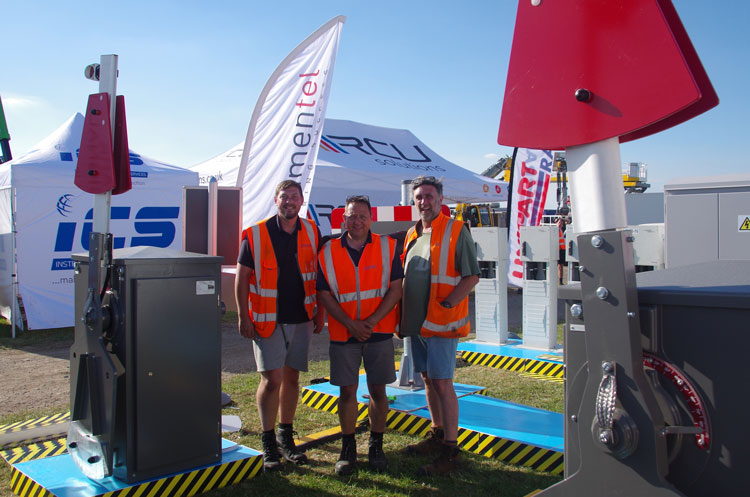
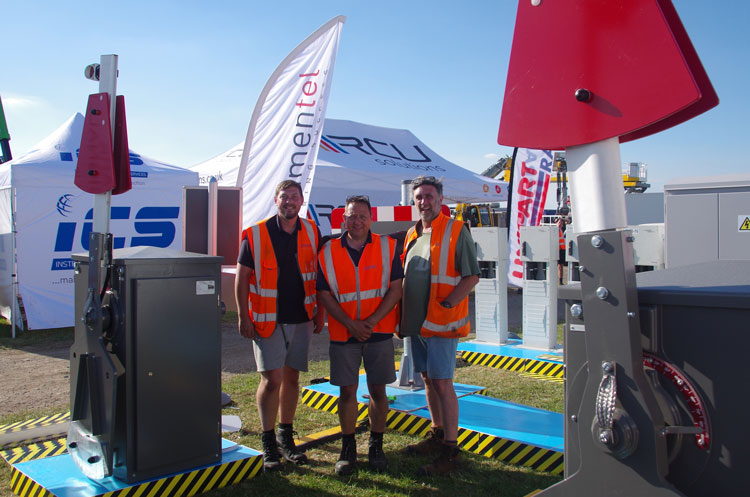
The sun shone on us at Rail Live – Ashley Shirt, Andy Marsh and Tim Hurst.
Fuel for thought
The Level Crossing Innovation Day and the Rail Live exhibition were a chance to embrace the spirit of experimentation. The ‘level crossing in a box’ project offered up a snapshot of what can happen when a group of talented minds are unleashed to rethink established processes. Our next step is now to agree the practicalities of applying what we’ve learned and migrate these methods to business as usual. Hidden inefficiencies do exist; we can find them, and the industry can benefit from them.
Supplier relationships, often overlooked, are a golden opportunity to diversify and widen the industry’s perspective, generating fresh ideas for solving shared problems. Manufacturing processes are ripe for disruption, and the benefits of doing so are enormous. Logistical challenges, observed in a new light, open the sometimes-narrow mindsets of a traditional industry and are the inspiration for new methodologies of pre-construction and remote testing. Following through on these opportunities to change our industry will require vision and integration from all stakeholders, but we should not shirk the responsibility placed on us in the supply chain. To deliver truly outstanding service on our railways, we must embrace the pioneering and innovative thinking to drive performance and attract passengers back to trains. The future of rail depends on it.
For further information, please reach out to the team:
- Atkins: Ian Martin, Win Work Director, Signalling ([email protected])
- Unipart Rail: Andy Little, Business Development Manager ([email protected])
- Newgate (Newark) Ltd: David Truman, General Manger ([email protected])
Issue
Related topics
Related organisations
Atkins, Newgate (Newark) Ltd, SNC-Lavalin Group, Unipart Rail