Using innovative track diagnostics for data-driven decisions
Posted: 16 December 2022 | Goldschmidt Group | No comments yet
Stefan Damm, Head of Business Field Inspection Solutions at Goldschmidt, discusses the evolution of track inspecting technologies and details the benefits that come with detailed track diagnostics.
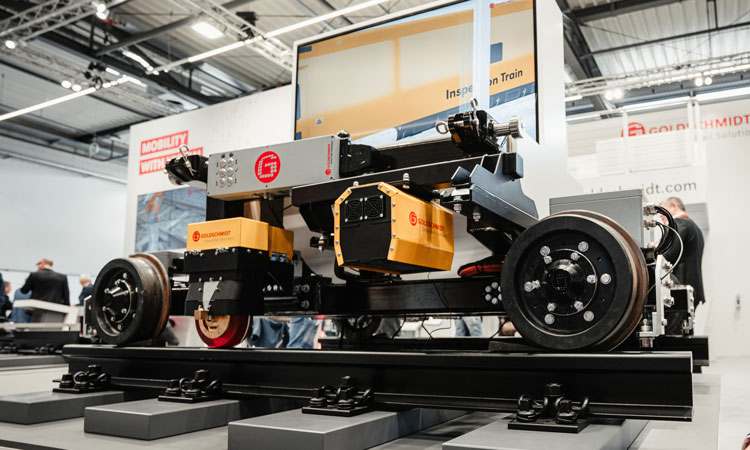
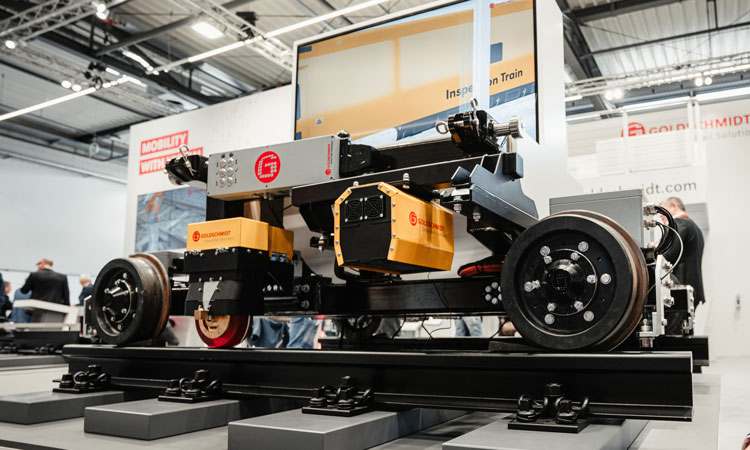
Measurement bogie
Why do you think infrastructure managers are now looking for more innovative ways to inspect their tracks?
The demographic change, which most first world countries are already facing, will be a major challenge in the coming years to railway systems around the world. The shrinking and over aging population will accelerate the lack of skilled resources for both inspection and maintenance outside in the field while the available engineers focus their activities onto remote supervision from office desks. In this framework, technology is becoming a prerequisite to keep or increase the level of inspection with a shrinking workforce.
In addition to these challenges which drive technological development, regulatory bodies and public entities supervising rail network operators also show growing expectations: as they know what technology can do, they update inspection frequencies and parameters accordingly. Keeping up with this demand is forcing network owners to break new ground in infrastructure maintenance.
At the same time, modern and automatised inspection technology is the enabler to keep tracks safe while traffic and thus wear increase and track possession times for maintenance and inspection shrink to a few hours per night. Here, state of the art technology can reduce the human factor and avoid errors that can happen under stress and bad environmental conditions.
What information can detailed track diagnostics give an infrastructure manager?
Many industries consider data the new crude oil. When applying this thesis to railways infrastructure, surely data, simulation and digital twins can help in making smart decisions on good timing for maintenance interventions.
We differentiate between track irregularities and safety relevant alerts.
Maintenance measures, such as grinding or milling, take care of irregularities like profile wear or corrugation. They require attention as they might lead to rail defects in the long run but corrective maintenance can be planned with some notice.
On the other hand, the repair of rail flaws, such as volume defects, need to be taken care of timely in order to safeguard a secure and not interrupted operation.
A segmentation of a scanned network in green, yellow, and red sections – with or without prediction of the deterioration – can support smart maintenance planning. This can help to avoid costly and unplanned network shutdowns based on data that supports the scheduling of maintenance activities and triggers immediate safety measures.
The infrastructure manager takes advantage of both a general map view, that gives an overview of critical areas, and a detailed view on the single defect. Such information is essential for decision making between immediate actions and long-term maintenance or replacement measures.
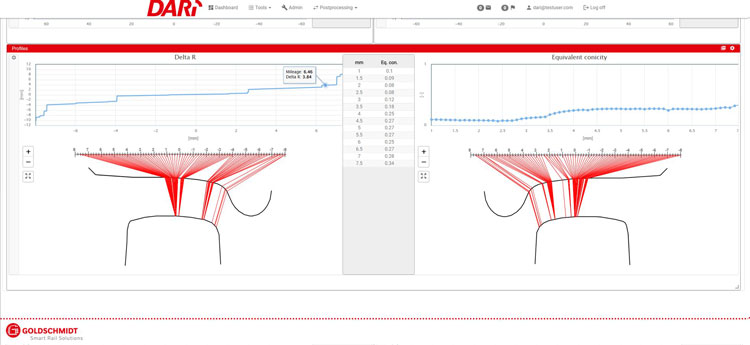
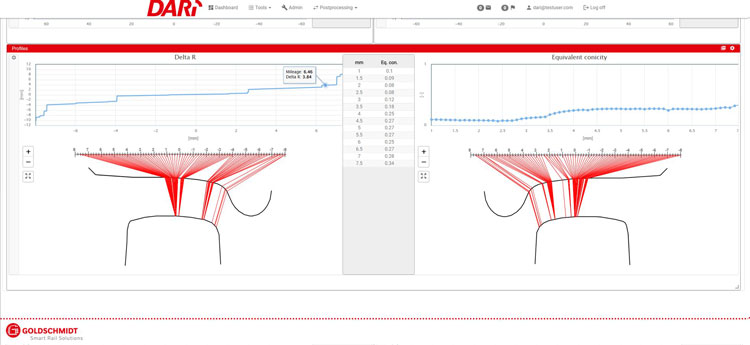
Analysis of results using Dari® software.
In what ways does track inspection play a part in the sustainable reduction of lifecycle costs of railroad infrastructure components?
Thresholds based on experience or regulation and defect classes allow for extensive lifecycles without compromising safety. Comprehensive assessments of data on deterioration over time, are essential for projecting future network conditions and maintenance vs. replacement planning.
While preventive maintenance risks to grind, mill or exchange still good components based on simply programmed maintenance and exchange schedules, reactive maintenance is expensive due to unscheduled line shutdowns and risky in terms of operational safety.
Smart and data-driven maintenance decisions are neither preventive nor reactive but make the most efficient use of your components that stay throughout their effective lifecycle.
Can inspection technologies be tailored for different demands and requirements?
Relevant parameters are nearly identical to all networks, even though types of components might vary, or regulations set different definitions of measurement points, for example in switches or along the individual rail profile. What really differs are the applied thresholds and defect classes, which in parts are defined with international standards but also follow national or local regulation and best practices. Implementing a wide range of measurement points, units and standards is a no-brainer with state-of-the-art software. However, there might be very different environmental conditions which require intense engineering and custom-tailored solutions: while inspection trains need to operate ideally at commercial speed, slow-running grinding- or milling trains are exposed to dust, flying metal parts and sparks. Both type of trains might perform the same inspection though with the same precision requirements.
As our customers operate from -50°C to +50°C – needless to say – there is no one-fits-all solution. Temperature compensation in systems and software, as well as a smart material selection requires different solutions for different applications.
What would you say makes your products and solutions stand out for your competitors?
At the turn of the century large infrastructure operators and their substantial engineering teams still acted as systems integrators, or at least set very precise design requirements. This led to extensive project durations. Such type of approach has already come to an end in commercial train manufacturing. Instead, the operators specify their needs and let it up to the specialists to design and build a vehicle that suits these needs. This turn-key approach is also being adopted more and more for complex special vehicles like inspection trains. Rather than doing a cherry picking from several individual suppliers and integrating them onto a vehicle from yet another supplier, we see that the preferred option is to specify the needs, find a single source which will deliver a fully integrated solution, and turn the key after a defined period of time.
Smaller networks used to outsource complex inspection tasks while they sent out their own track experts for visual inspection tours. Nowadays they combine both approaches with integrated inspection vehicles that perform automated AI-supported video inspection with precise measurements and flaw detection. In the end, all systems performing a variety of inspection and measurement tasks can be supervised by only a single engineer.
How do you think track inspection technologies will evolve in the future?
Customers want to get rid of dedicated vehicles and special solutions, hence, they would like to have everything mounted on one or more commercial trains which circulate frequently and ideally travel to every corner of the network. There is a realistic option to get there sooner or later for systems that do not need the contact of the rail, such as track geometry, profile assessment, corrugation measurement or video inspection. Safety-relevant crack analysis for head checks, squats or volume defects requires ultrasonic or inductive systems. Their sensors are guided along the rail, following the sinus run of the vehicle at a precise distance of about 1mm or even touch the rail. Such mechanical guidance along the rail needs to be constantly monitored and it is not foreseeable that such contact systems for trains carrying passengers at the same time will be accepted any time soon.
For the near future though I can imagine that semi-autonomous vehicles are pulled or pushed through a network just by a train driver with the entire inspection session being monitored by a skilled engineer from his office desk.
Related topics
Big Data, Digital Twins, Digitalisation, Technology & Software, Track/Infrastructure Maintenance & Engineering