IN2ZONE: Moving the EU towards the next generation of railway transition zones
Posted: 7 July 2022 | Bruno Zuada, David Connolly, Istvan Szatmari, László Véha, Marta Garcia, Valeria Markine, Vitek Lojda | No comments yet
This article explores the IN2ZONE research project which aims to design and test a prototype next generation transition zone solution that provides a step-change in track support conditions, resulting in a reduction in maintenance interventions.
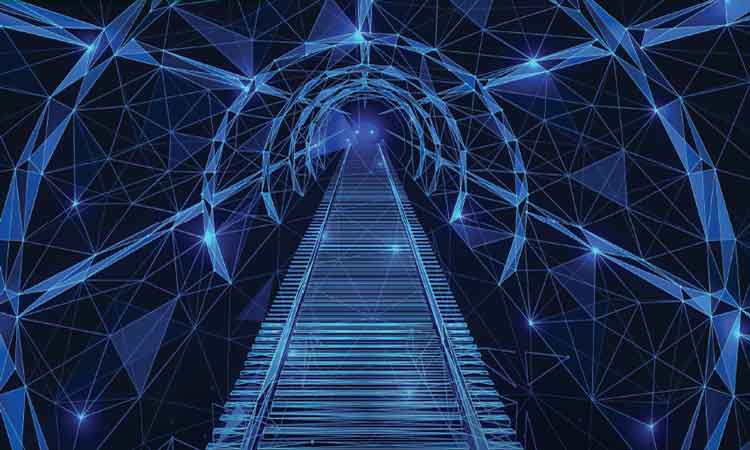
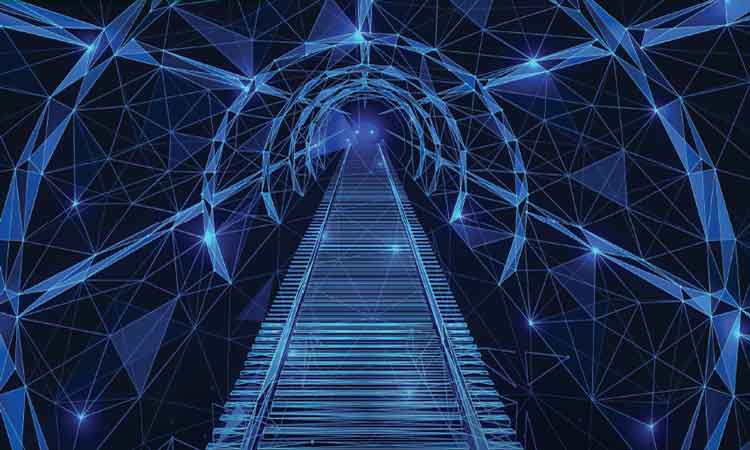
The average cost of building a railway line in Europe is between €13-40 million per kilometre, with high costs post‑construction due to the continued maintenance of the infrastructure. This is because, in some circumstances, there could be high infrastructure maintenance due to heavy traffic, high‑speed, poor quality of construction and poor subsoil, among other factors that require further attention after construction and/or several years of operation. A major source of track maintenance costs are the transition areas; locations with considerable changes in the rail-supporting structure. Typically, they are located near engineering structures, such as bridges, culverts and tunnels, as a high level of maintenance is required here to retain the desired track geometry to ensure passenger comfort and avoid speed restrictions. According to Sasaoka and Davis1, $200 million is spent annually on track crossing maintenance on U.S. railroads, while €85 million is expected to be spent for similar operations in Europe.
Transition areas, therefore, stand to be a great opportunity to significantly reduce both the direct and indirect maintenance costs, such as train delays and capacity losses caused by line interruptions. Transition areas should allow smooth train movement and minimise the effects of changes in stiffness of the track supporting layers. When a train moves from an embankment towards a stiff structure, such as a bridge, tunnel or culvert and tunnel, there is an abrupt change in support stiffness which increases dynamic wheel loads and causes high increased track stresses.
To solve these longstanding transition zone problems, the Shift2Rail European R&I project IN2ZONE has been tasked with designing and testing a prototype next generation transition zone solution that provides a step-change in track support conditions and results in a drastic reduction in maintenance interventions. To achieve this, new self-levelling sleepers will be designed, formed from synthetic material, with optimised geometry and stiffness for transition zones. This will enable the transition zone solution to self-correct minor track geometry irregularities or faults, meaning fewer and less frequent maintenance activities. These novel sleepers will be part of a holistic design, which also considers novel ballast stabilisation, soil improvement and resilient elements to optimise the change of stiffness across the transition. An advanced resilience‑based monitoring specification for transition zones will also be designed, one that combines track, vehicle and satellite sensors. The new solution will combine the latest existing transition solutions with technological advances from other fields, including recent advances in materials science.
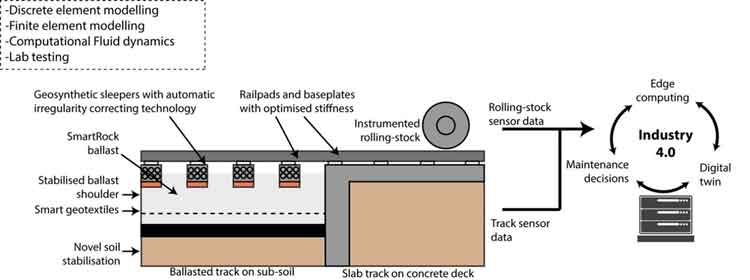
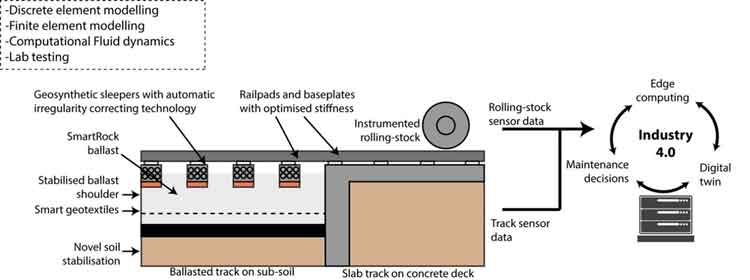
Figure 1: Vision of IN2ZONE’s holistic next-generation transition zone solution.
The IN2ZONE project will be using, as a baseline, a timeframe of 40 years beyond the current state-of-the-art. The new design will be optimised with the latest advances in discrete and finite element numerical simulation tools coupled with Computational Fluid Dynamics. The transition zone concept will then be built and tested in a controlled laboratory environment. To add value, Hazard Identification (HAZID) (risk analysis), Life-Cycle-Costing (LCC) and Reliability, Availability, Maintainability, and Safety (RAMS), used to characterise the railway system, will also be investigated as part of the project. Elements will include:
- Develop a technical specification for next generation transition areas that is not limited to current practices while retaining key railroad functions. The development of the specification will focus not only on technological advances from other sectors, but will also consider the latest existing transition solutions
- New approaches will be identified that provide a step change in performance through sustaining the continuous contact between a sleeper base and ballast, even if higher ballast settlement occurs and both uniform and optimal stiffness of the overall system from the natural subgrade to the rail head
- Design of a modular architecture for the next generation of transition zones. This will allow for ease of installation, maintenance and decommissioning, especially when upgrading existing transition zones
- Develop a self-correcting design for transition zones. It will be able to self-correct minor vertical track geometry errors. Research new materials for each major transition zone component and holistically optimise their properties to maximise performance. The new materials investigated will reduce maintenance and environmental impact while ensuring resilience of the system to climate change
- Development of a Common Safety Method for Hazard Identification and mitigation for all phases of the system lifecycle. This includes the use of novel materials, optimised design for reliability, manufacturing techniques, installation methods, maintenance requirements and decommissioning
- Development of advanced numerical simulation tools to support the validation of final transition zone designs for a range of applications. This includes discrete element (i.e., grain-level) modelling to understand the behaviour of various transition types such as switches and crossings underpasses and track changes
- Developing a resilience-based monitoring specification for transition zones. This will allow the selected solution to be fully self-inspecting. Combined with the advanced design, it will be relatively maintenance free but, if maintenance is required, it will be just-in-time
- Validation of the new transition zone solution through full-scale laboratory testing
- Develop LCC and RAMS performance models for the transitional solution and carry out a full cost-benefit analysis. This will include consideration of the impact of increased rail infrastructure capacity due to increased train speeds in the transition zones.
Major technical achievements and forthcoming work
A track section with the new self-levelling sleeper design is being built and tested at a large-scale accelerated testing facility. This approach allows observers to simulate the effect of a train loading over several years in just a matter of days. The experiments are performed to assess the short and long-term performance of a ballasted track section resting on a compacted substructure. The testing box is 0.93m wide, 3.8m long and 0.685m deep; it is supported by thick composite base. The testing rig utilises hydraulic actuators which are individually capable of loading 150kN at loading frequencies up to 15Hz, and up to 200kN statically.
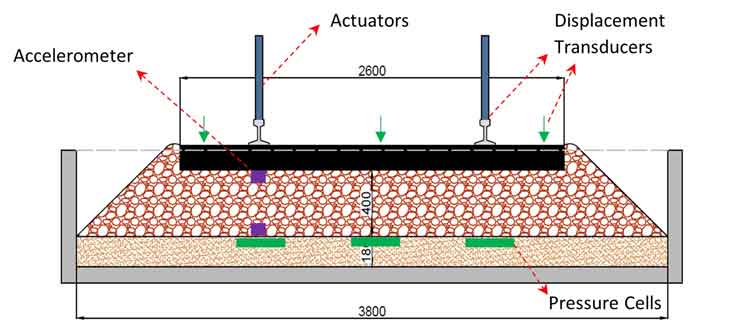
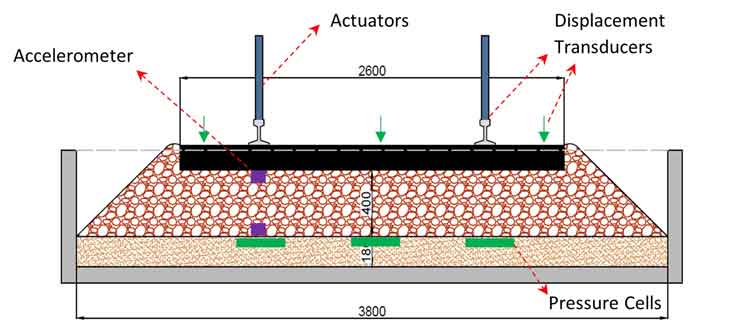
Figure 2: Sensor positions on a cross-section of the facility.
Pressure cells under the ballast, displacement transducers on the sleeper and rails, accelerometers in the ballast and on the sleeper, will also be positioned within the design. A 17-tonne axle load is applied statically and cyclically after calculating the load on the middle sleeper, based on the beam on an elastic foundation method.
In the present project’s framework, a robust monitoring system will be developed, explicitly designed to serve special functionalities of the transition zone monitoring based on existing railway onboard and wayside monitoring systems. Emphasis will be placed on it, given the expected harsh environmental conditions in railway field applications that require high reliability and availability. The system will be composed of various sensor modules, installed at different track positions (i.e., track line, sleepers, ballast, etc.).
Due to the various structures and materials used for transition zone construction, the monitoring system shall provide a flexible, modular, and scalable approach to fulfil different physical, timing, and application aspects and requirements. As a general approach, the monitoring system will fuse measurements from multiple sensors, collect and aggregate data through field communication devices (edge computing) and apply different cloud-level processing and evaluation in a digital twin framework.
Reference
1. Presentation on implementing track transition solutions for heavy axle load service at the AREMA 2005 Annual Conference
The work presented in this paper has received funding from the Shift2Rail Joint Undertaking under the European Union’s Horizon 2020 research and innovation programme (grant agreement no. 101014571). The contents of this publication only reflect the authors’ views and the Joint Undertaking is not responsible for any use that may be made of the information contained in the paper.
Issue
Related organisations
Coelho, Deltares, Evopro Innovation Kft, IN2ZONE, Lankhorst, MÁV, SHIFT²RAIL, UNIFE (the European Rail Supply Industry), University of Leeds
Related people
Bruno Zuada, David Connolly, Istvan Szatmari, László Véha, Marta Garcia, Valeria Markine, Vitek Lojda