Simulation models in hybrid train design: Issues of fitness for purpose
Posted: 18 March 2022 | David Murray-Smith | No comments yet
For Global Railway Review, David J. Murray-Smith, Honorary Senior Research Fellow and Emeritus Professor at the James Watt School of Engineering for the University of Glasgow, details the flaws in current simulation models for hybrid trains and explores how they can be corrected.
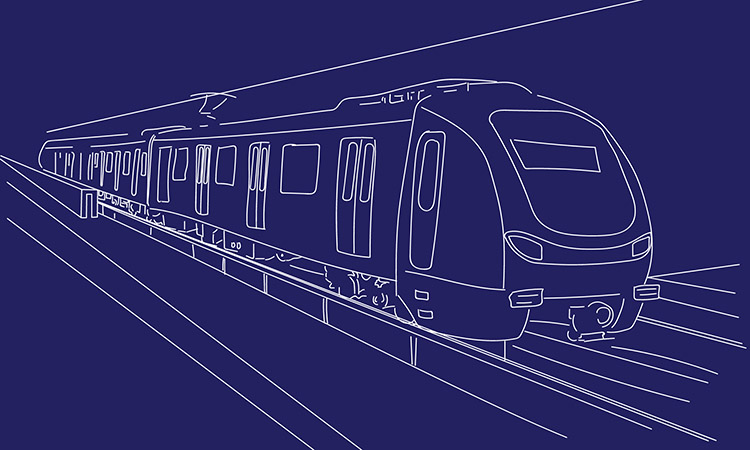
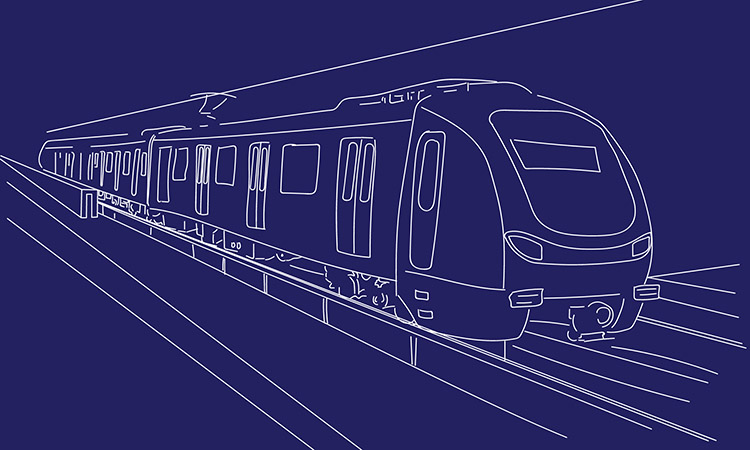
In engineering applications, simulation methods allow for early considerations of design trade-offs and system integration issues before any prototype system becomes available. Eliminating potential problems before hardware assembly starts has clear benefits in terms of cost, safety and timely delivery of the final system, as demonstrated in other fields such as aerospace engineering. However, simulation models are never correct since they always involve assumptions and approximations; they must be proved fit for the intended application. Some attitudes to simulation, such as ‘this is how we always do it in our models’ or ‘it is a standard approach so it must be right’ are now regarded as unacceptable. Models should have an adequate level of accuracy in terms of their predictions, compared with data from the corresponding real system, and must also be capable of being used effectively and conveniently for the application at hand.
The design of hybrid trains involving primary energy sources (e.g., diesel engines or hydrogen fuel cells), energy storage elements, (e.g., batteries, supercapacitors, or flywheels), transmission elements (e.g., electronic power converters) and drive elements (e.g., electric motors) provides relevant examples. The reason for the current interest in this is linked to the de-carbonisation of passenger rail services, especially for long routes in sparsely populated areas where traffic levels may not justify conventional electrification or partially electrified routes. However, the conversion of existing diesel and electric multiple units provides one way forward, with several prototype systems of that kind now under development in the UK.
Simulation models are never correct since they always involve assumptions and approximations; they must be proved fit for the intended application.
Hydrogen fuel cells tend to be sluggish in their response to changes of demanded power and, in hybrid powertrains involving fuel cells, stored energy from the battery pack provides additional power when accelerating and ascending steep gradients. The sizing of powertrain components is therefore important and design calculations must also allow for critical constraints, such as those on battery pack weight, the volume and weight of hydrogen storage tanks and cost.
Conventional simulation models for the longitudinal motion of a train usually involve an input variable which is a time-history of power or tractive force, with output variables that may include records of acceleration, speed or distance travelled. However, it is also possible to work backwards, using a time history of required speed or distance travelled as inputs to produce tractive force or power values as output. This inverse simulation approach, first developed for aircraft flight dynamics applications, allows power requirements to be investigated for a given train schedule and is useful when considering energy management and control issues in hybrid powertrains. Where a hybrid design is being developed to replace an existing train type, such as a diesel multiple unit (DMU), a time history of distance versus time obtained from data recorded on the train on a specific route or from simulation, is potentially useful. Simulation time-scaling methods allow for a reference schedule of this kind to be adjusted to investigate possible performance enhancement.
Simulation models of hybrid trains
The longitudinal motion of a single train for a specific route is considered here, involving variables such as distance travelled, speed, acceleration, tractive force, power and energy used. For powertrain control and energy management applications the dynamics of the train itself, together with the characteristics of the route such as gradients, curvature and speed restrictions, are vitally important. Powertrain component models must therefore be integrated with a model of the train dynamics, along with constraints such as allowable charge and discharge rates for battery packs, the maximum and minimum allowed battery charge state and conditions for efficient engine or fuel-cell stack operation. Figure 1 is a simplified block diagram showing powertrain components, the longitudinal train model and the route model in the case of a fuel-cell/battery-electric unit. Regenerative braking is allowed, with arrows indicating possible directions of power flow.
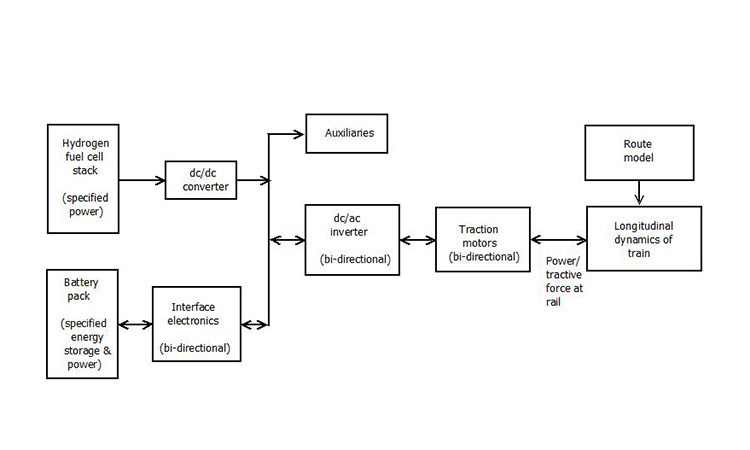
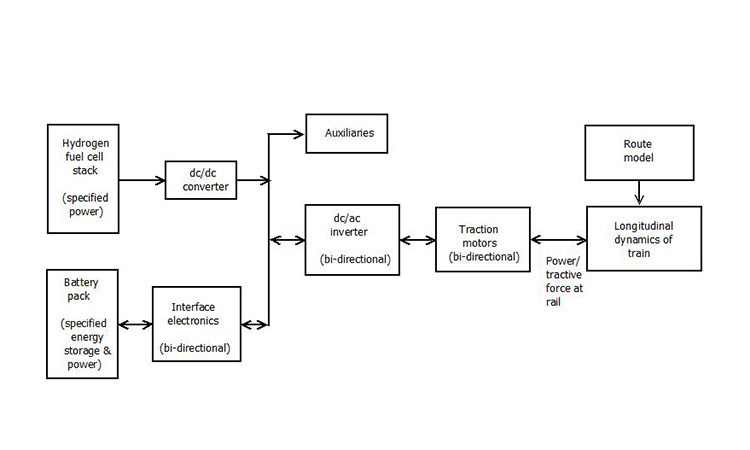
Figure 1: Block diagram structure for dynamic model of hydrogen fuel-cell/battery-electric train.
Depending on the system under investigation and the modelling objectives, model boundaries may be extended to include external energy supply and distribution systems, as would arise in discontinuous electrification schemes. The timescale for the simulation model also must be considered carefully. For example, events on a millisecond timescale may be unimportant if the aim is to estimate the onboard hydrogen storage requirements for a specific journey. However, fast transients may have to be considered if the detailed performance or control of powertrain components, such as power-electronic converters, is of interest. The model structure, model boundaries and model timescales must therefore all be tailored carefully to the intended use.
The type of mathematical description affects the computational methods used. For example, powertrain models for hybrid road vehicles are often steady-state or quasi-steady-state descriptions, involving simplifications that neglect most dynamic effects. Such models might also allow approximate estimation of the energy or fuel consumption of a train on a specific route, but dynamic descriptions are needed for more detailed train performance investigations, for the design of energy management and control systems and investigations of interactions between trains and their electrical supply systems on electrified railways.
Dynamic models are based on ordinary differential equations derived from Newton’s laws of motion. In models of longitudinal train motion, the tractive force at any time instant is balanced by an inertial force involving the train mass and acceleration, plus forces which include aerodynamic and other resistive characteristics of the train, and terms depending on the route (e.g., gradient values, curvature and additional aerodynamic effects when a train is travelling in a tunnel). This gives a generic description, often involving a point mass approximation which is convenient and often considered appropriate for modelling short multiple-unit passenger trains. However, multi-mass models may be needed for longer locomotive-hauled passenger or freight trains.
Hybrid train applications will require a dynamic model to allow for the continuous assessment of the energy required from the fuel cell and battery pack for given constraints in terms of power ratings and route characteristics.
Fully tested and well-documented sub-models of the powertrain and drive system components are normally available from manufacturers, any uncertainties may often be eliminated through the dynamic testing of the integrated powertrain system before the final installation. The important uncertainties in hybrid train models are associated mainly with the train resistance characteristics, together with the effects of track curvature and gradients. Accurate modelling of train braking may also present difficulties, especially where blended regenerative and friction braking is used.
Inverse models have been used in the design of automotive powertrains, but these generally involve steady-state or quasi-steady descriptions. Extending these ideas to hybrid train applications will require a dynamic model to allow for the continuous assessment of the energy required from the fuel cell and battery pack for given constraints in terms of power ratings and route characteristics. Inverse simulation methods can also provide useful insight in investigating regenerative braking systems, with a given profile of acceleration or speed versus time as input and braking force as an output.
Getting the right balance between fuel-cell stack size and battery pack size can be a complex design process. In general, it can be said that hillier routes lead to configurations involving larger batteries to cope with the frequent changes in demanded power level. Inverse simulation methods are potentially useful for such investigations, as discussed in a report published in 2020 and a more recent publication that outlined some simulation activities linked to the conversion of the former ScotRail Class 314 electric multiple-unit (EMU) shown in Figure 2. A consortium of companies led by Ballard Motive Solutions (formerly Arcola Energy Ltd.) is involved in that conversion project, with funding from Transport Scotland and Scottish Enterprise. The Hydrogen Accelerator group at St. Andrew’s University also has a central role in the management of the project.
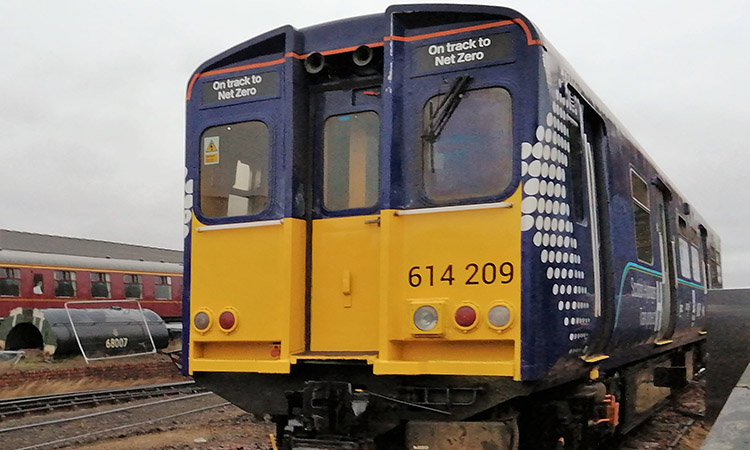
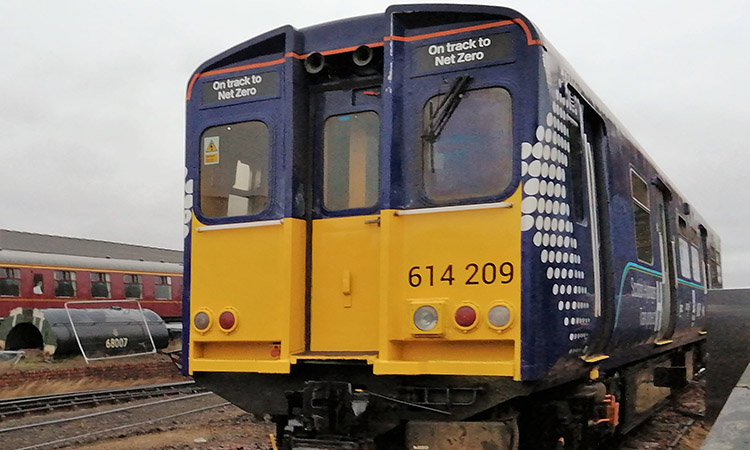
Figure 2: The hydrogen fuel-cell/battery-electric hybrid unit converted from a ScotRail Class 314 EMU, as seen at Bo’ness during a COP26 showcase event in November 2021.
Issues of testing, validation and verification
The investigation of accuracy issues into the simulation models of trains involves assessment of the correctness or otherwise of the mathematical description (a process of model validation) and detailed examination of the simulation methods and numerical techniques applied (model verification).
For models of existing trains, data gathered on the train (e.g., speed, distance travelled, power or tractive force applied at each time instant over a specific route) allows for quantitative investigation of predictive accuracy.
Experts familiar with the real system can examine the simulation behaviour and assess the effects of uncertainties through repeated simulation runs with different values of relevant parameters. For models of existing trains, data gathered on the train (e.g., speed, distance travelled, power or tractive force applied at each time instant over a specific route) allows for quantitative investigation of predictive accuracy. Global positioning system (GPS) data can be used but care is needed due to possible errors or inconsistencies. For example, gradients can be estimated from altitude data but inherent errors in the GPS altitude channel can give misleading results. Conventional gradient profiles are therefore usually preferred in route modelling. However, GPS data could be useful in obtaining estimates of other uncertain quantities within train models, such as train resistance parameters, using methods of system identification that are well-established in other fields. This is an interesting area of research for future industrial/academic collaboration and could have practical benefits in terms of better modelling of train resistance, one of the main limiting factors in current train models.
Discussion
The fitness of any model depends both on decisions about model boundaries (i.e., what features of the system are included) and on how the model is used. One must also be able to provide estimates of the accuracy of simulation results. Modelling is iterative and model updates are needed whenever changes are made to the corresponding real system. Repeated model testing and careful model management are therefore essential, raising issues that are not yet recognised by everyone within the rail industry. Model limitations must be fully understood by users and formal procedures for model version control and the updating of documentation needs to be in place to avoid unrecorded changes in a model. Ideally, simulation models need to be maintained throughout the life of the systems that they represent. Not only does this ensure that a model remains fit for its original purpose but also means that a model developed during one design project may provide a useful starting point for future developments.
Conclusions
Models used to represent the longitudinal dynamics of a single train have many potential applications in design, but uncertainties mean that simulation results should always be used with caution. Sound procedures for model testing, along with good documentation and processes to record all changes made in a model, are essential in ensuring adequate model quality and fitness for purpose. In addition, how simulation models are used, whether in forward or inverse fashion, should always be central to discussions about model fitness.
Related topics
Electric/Hybrid Rolling Stock, Hydrogen Trains, Operational Performance, Sustainability/Decarbonisation