‘Fingerprint’ measuring project helps to ensure WESTbahn’s fleet availability
Posted: 16 August 2021 | Christian Pettauer | 1 comment
Christian Pettauer, CIO at WESTbahn Management GmbH, tells Global Railway Review about the modular maintenance that it believes is the secret to its high fleet availability, and how invaluable, real-time measurements of rolling stock components and tracks from the ‘Fingerprint’ project is key in pinpointing the right maintenance at the right time.
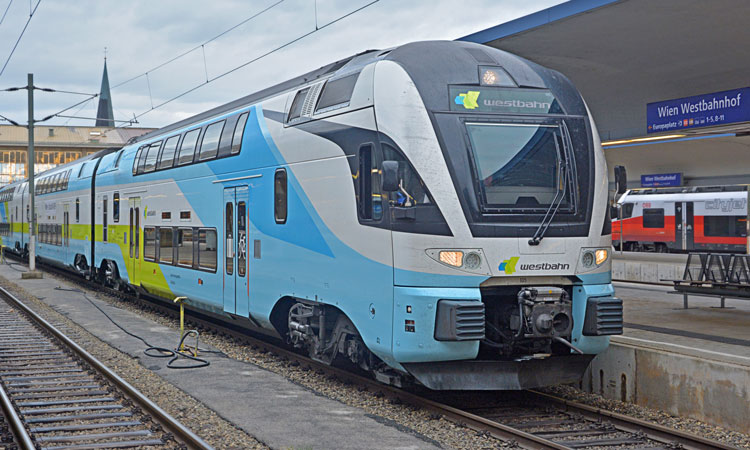
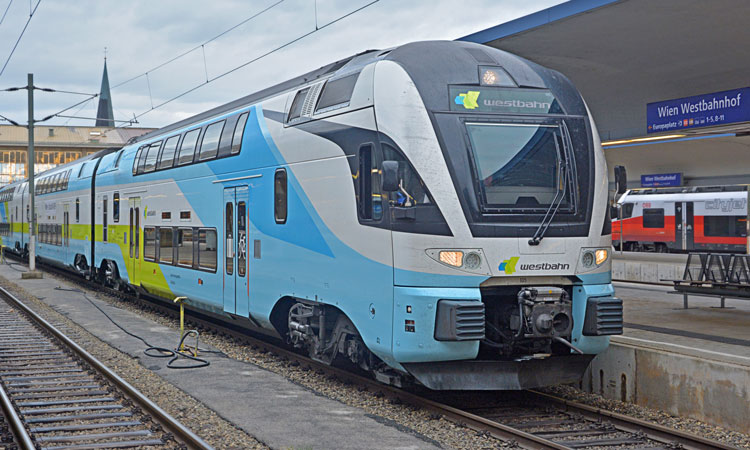
In December 2011, WESTbahn took up its Vienna–Salzburg Intercity service using a fleet of seven Swiss Stadler KISS 1 locomotives. We dared to do this without any operational reserve and, with great success, have continued to apply this concept of the daily use of all trainsets when we temporarily increased our fleet to 17 KISS 1s in December 2019. We, of course, hope to successfully continue doing so with the brand-new 15 KISS 3 trainsets that we are expecting in autumn 2021.
‘Fingerprint’: Extending the lifecycle of wheelsets
Apart from the fact that our KISS trains are very high-quality rolling stock, we believe that one of the main secrets behind our high fleet availability is the modular maintenance that we do during the night with our maintenance partner ÖBB-Stadler Service GmbH. Together, we learn and optimise – for example, concerning wheel mileage. When WESTbahn started, wheels had to be replaced every 1,000,000km; today, we do it after 1,500,000km. We were able to shift this goal backwards because we also had help from outside: ÖBB-Infrastruktur AG – the organisation that plans, develops, maintains and operates rail infrastructure in Austria – set up their ‘Fingerprint’ project about three years ago. In the course of this project – together with the companies Mermec and Hottinger and Brüel & Kjær (HBK) – ÖBB Infrastruktur established several Argos® wheel force and wheel shape measurement systems all over Austria. In real-time, this system can provide information about horizontal and vertical wheel forces, wheel cross profiles and wheel out-of-roundness.
As we all know, the rounder the wheel, the better for the train, customers and the railway superstructure. An overall cost efficient and safe railway system is only possible if we have detailed knowledge of the current condition of both rail and vehicle at any given time. Therefore, it is indispensable to permanently measure vehicles and tracks – and this is exactly what ‘Fingerprint’ does.
At high running speeds, minor changes in the wheel or track profile and track alignment, in combination with the utilisation of component tolerances in the running gear and wheels, have a strong effect on the running quality of the vehicles. Even if all parameters are within the permissible tolerance, a combination of these circumstances can cause unstable vehicle running, poor running comfort or, in the case of freight wagons, freight shifts. Such vehicle behaviour also leads to a negative development in track quality and rail surfaces in the long-term, which increases maintenance costs and reduces track availability. Aside to this, out-of-round wheels are a major cause for high noise emissions that affects the passenger travel experience and the environment.
With the ‘Fingerprint’ system powered by HBK, it is now possible, for the first time, to objectively measure and evaluate the real running behaviour (hunting) and the influencing parameters and, as a consequence, give an overall picture of all wheel force and wheel form parameters for every vehicle passing by under real conditions at a velocity of up to 250km/h – in real time and with peak accuracy. This is a completely new approach that helps to generate the basis data for reliable predictive maintenance reports for vehicles.
Monitoring is different to measuring
Several geometrically based thresholds are given in European standards (e.g. EN 15312). In many cases, European infrastructure providers and railway undertakings use a simple indirect approach of measuring dynamic impact forces to just monitor those thresholds. Monitoring, of course, is something quite different than measuring. However, the velocity and the maximum dynamical wheel load are subject to non-linear principles and do not always correlate to actual wheel defects and their size. Simply knowing the dynamic forces in a certain case is, therefore, not reliable enough for maintenance decisions.
To mitigate that problem, a new method (EP 1883 565) was developed. In this method, signals are derived from the measuring element, which measures rail acceleration in the vertical direction. After that, an information array is formed in the evaluation device from the signals, which corresponds at least to the periphery of the wheel. The periodic signal of the wheel’s shape is evaluated with the aid of a Fourier development. The system is designed in a way that at least measures two wheel blanks (two overruns) for each wheel.
There is a ‘Fingerprint’ measurement site in the Tullnerfeld area, where WESTbahn services runs on a daily basis. The installation there provided us with a dataset including the so-called wheel roundness Delta R factor, initially during a test period from February 2018 to autumn 2019. Its patented method delivers the progression of Delta R through the circumference of the wheel in the contact point. The system measures the wheel’s deviation compared to an ideally round wheel with a Delta R resolution better than 0.01mm, repeatability 0.05mm as a trend function and 0.1mm as an individual measurement. Measuring is accurately possible, starting from a speed of 40km/h and going up to, as mentioned before, more than 250km/h. The big advantage is that the measurement results can be directly used for maintenance purposes through the ‘Fingerprint’ application.
Every Monday, WESTbahn gets the summed measured data from the previous week, which includes vehicle number, Delta R, number of measurements, location in the vehicle and data evaluation as an indicator. For every measured wheel, additional detail data is sent to the operator. This additional data includes the velocity at the measurement and graphs for the Delta R in the whole circumference, which helps to find any failure very quickly.
In order to fit into our modular maintenance system, as a company, we decided long ago that every wheel coming to a value of 0.20 should be reprofiled. Since we perform reprofiling at that very early stage, the milling will remove only little material. As a consequence, we can use the wheel for a much longer period. This also helps to maintain WESTbahn’s high standard of ‘smoothness’ when operating on tracks. Because of this underlying attitude, we were extremely happy to receive real time information about our wheel roundness from the ‘Fingerprint’ system in order to be able to react quickly and send the bogie in question to the reprofiling facility as soon as it is necessary.
Summary
WESTbahn’s experience so far with ‘Fingerprint’ has been very good. The system works reliably, each single coach is precisely identified and the report tells us which wheel exactly is the one with an upcoming problem. Despite the velocity of our train, the information delivered from the ‘Fingerprint’ installation with the special measuring devices and data analysis from HBK is characterised by extremely high reliability.
This service helps railway undertakings to optimise costs, since deviations can be detected at a very early stage. At the same time, it helps the infrastructure provider to minimise maintenance needs, as the ‘moving components’ are in a good condition and thus put little strain on the infrastructure. Less maintenance needs on the infrastructure side not only mean cost-savings in general, but also less construction sites and – in the end – a higher overall availability for the railway undertakings and their customers.
Issue
Related topics
Bogies & Wheelsets, Rolling Stock Components (Interior/Exterior), Track/Infrastructure Maintenance & Engineering
so you mean if the roundness goes below .2 you will reprofile the wheel??