Making switch machines intelligent: Vital for rail’s digital transformation
Posted: 15 December 2020 | Christian Fritz | No comments yet
Christian Fritz, Vice President for Customer Service & Project Management of the Diagnostic and Monitoring Technologies for Infrastructure Department at voestalpine Signaling Austria GmbH, writes that the development of intelligent switch machines is fundamental in the digital transformation of rail networks.
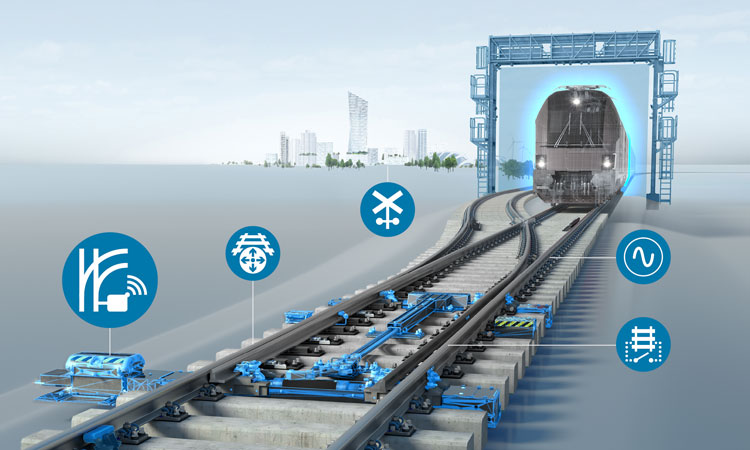
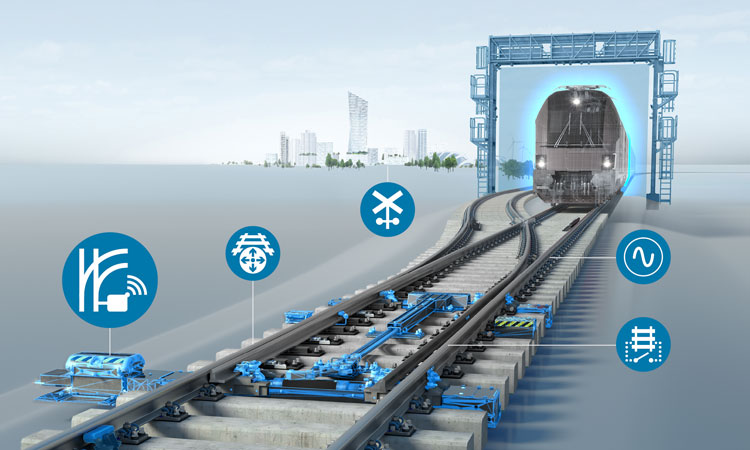
Diagnostic and Monitoring Technologies for Infrastructure – Digital ‘Performance on Track®’
The increasing density of train traffic is placing high demands on reliability, efficiency and availability. In addition, the periods available for maintenance are becoming extremely tight. Monitoring systems have been already used for years now for the preventive detection of issues and in the field of condition-based maintenance. Within the scope of progressing digitalisation, the use of intelligent field elements opens innovative application options for train operators and infrastructure companies. voestalpine Signaling has, therefore, set itself the goal of making switch machines intelligent.
What makes a switch machine smart?
A battery-operated logger is used for data logging and wireless data transmission of extensive status data and is designed for use in switch machines and hydraulic power transmission systems. The compact unit is located directly in the switch machine or in a separate housing. The intelligent, battery-operated and wireless diagnosis system does not need an external power supply nor an additional data connection and is operated using a battery and mobile data transmission technology. It is designed for an energy-saving mode in order to obtain a long battery service life. This means that all of the components and sensors have been designed and implemented in line with a holistic energy-saving philosophy.
Depending on the desired task, the data logger can be operated in various application modes, including:
- Pressure measurement on electro-hydraulic switch machines
- Measurement of the setting force on switch machines
- Pressure measurement for hydraulic power transmission.
The analogue channels of the sensor system are only activated at the time of setting and assessed by the diagnosis software on the data logger. In normal cases, the integrated modem is only activated for data transmission once per day in order to transmit the saved data. Irregularities, on the other hand, are forwarded as soon as they are recorded. This is in line with the concept of decentralised data processing (edge computing).
In addition to internal measured values, such as signal strength and battery voltage, the data logger offers numerous external measurement functions. Measurements of pressure, force, temperature, etc., can thus be easily made with the help of application‑specific external sensors. Three analogue and four digital data inputs are available, which can be used in various analogue or digital operating modes. In addition, a voltage output is available, which can be configured to be turned on by the device itself before a measurement (e.g., to supply power to a sensor). The recorded data is saved on a non-volatile storage medium. This saved data is sent via the mobile network to the central ROADMASTER® server for further processing. The data logger is equipped with an integrated low‑power modem for this purpose. Subsequently, the LTE-M technology, which has been especially developed for the Internet of Things (IoT), is used as an efficient radio technology.
The data logger is configured using Firmware Over The Air (FOTA). As a result, you do not need to have physical access to the hardware to load updates and configurations to a device in the field. After the end of each data transfer, you have the option to reconfigure the logger or change parts of the configuration individually using a configuration file, which is stored on the monitoring server and then transferred to the logger when data transmission is active and automatically installed.
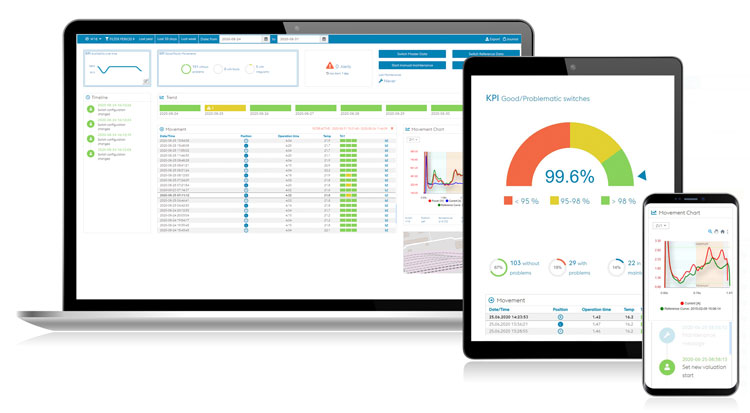
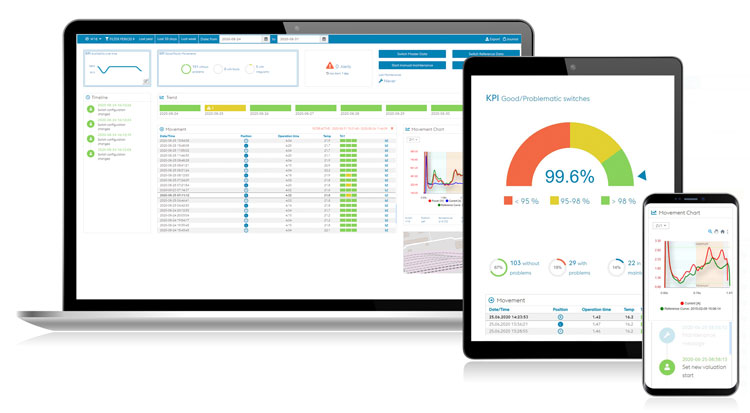
Integration in the diagnostic and monitoring system ROADMASTER® for condition and future oriented maintenance.
Sensor and system components
During diagnosis of electro-hydraulic switch machines, the compact data logger and the compact sensor system are integrated directly into the switch machine. Using two pressure sensors, the differential pressure for the force progression is determined during setting. Additional sensors are used for the filling level measurement (oil tank or hydraulic unit). Moreover, one phase of the four-wire supply is guided via the split core current transducer in order to monitor the setting duration and as a trigger signal for recording the setting force curve. The split core current transducer is used for contactless measurement of the setting current of a switch machine motor. The design of this split core current transducer provides the galvanic separation between the primary side (motor current) and secondary side (data logger), which is required from a safety perspective.
If the diagnosis system is retrofitted in electro‑mechanical or electro-hydraulic switch machines, the setting force can be measured using a force transducer bolt. The existing mechanical connection bolt between the switch machine and locking system is replaced by an electronic force transducer bolt, which records the mechanical setting forces during the setting process. The use of system pressure monitoring should detect pressure drops in a preventative manner and prevent resulting turnout issues.
The energy-saving system set-up presents a‑crucial aspect here. The data logger is powered by two 19Ah lithium batteries connected in series. The battery life (in consideration of self-discharge) is heavily influenced by the number of data recordings (number of settings and setting duration), and the number of irregularities recorded. Data from correct operations is transferred to the monitoring server once per day. However, irregularities are forwarded as soon as they are recorded and require higher transmission volumes. Under normal conditions, you can expect a battery life of up to five years.
Standards and regulations
The system has been developed and approved with the consideration of the following standards:
- Electromagnetic compatibility: EN 50121‑1:2105-03 / EN 50121-4:2015-03
- Vibration and shock: EN 50125-3:2003
- Temperature: IEC/EN 60068-2-1, IEC/EN 60068‑2-2 (-33°C to + 70°C).
Benefit and practical experience
The data logger has already been successfully implemented in Austria, Germany, Romania, China and Thailand.
Data connection and power supply play a key role in the integration of monitoring systems. Conventional monitoring systems require often complex cabling for the power supply, as well as the measurement process itself. In addition, data transmission is also done via cable or an additional external modem. With the battery-operated data logger and the integrated M2M- (Machine-to-Machine) communication, no additional cabling is needed, and commissioning on‑site is reduced to approximately 15 minutes.
Outlook
The data logger can also be retrofitted in existing turnout installations and can be used in other interesting rail sectors. The system is presently used for the monitoring and forecasting of system pressure in hydraulic power transmission. During forecasting, an outlook of short and medium-term changes of system pressure is provided, which qualitatively supports the planning of service and maintenance measures.
Switch machines with integrated monitoring systems are a key step in the direction of reliability optimisation through digitalisation. In this day and age, cost-effective and reliable sensor systems are readily available. In this context, the next logical step is the intelligent turnout, with which, in addition to the switch machine, any critical components used in the turnout are monitored and unnecessary tasks on the turnout are prevented.
Issue
Related topics
Artificial Intelligence (AI), Big Data, Digitalisation, Technology & Software