Trenitalia’s approach to introducing Additive Manufacturing to accelerate spare parts availability
Posted: 14 May 2020 | Daniele Rossi | No comments yet
Daniele Rossi, Trenitalia’s Head of Logistics, explains why Italy’s main rail transport company has turned to using Additive Manufacturing (AM) as a transformative approach to manage spare parts availability.
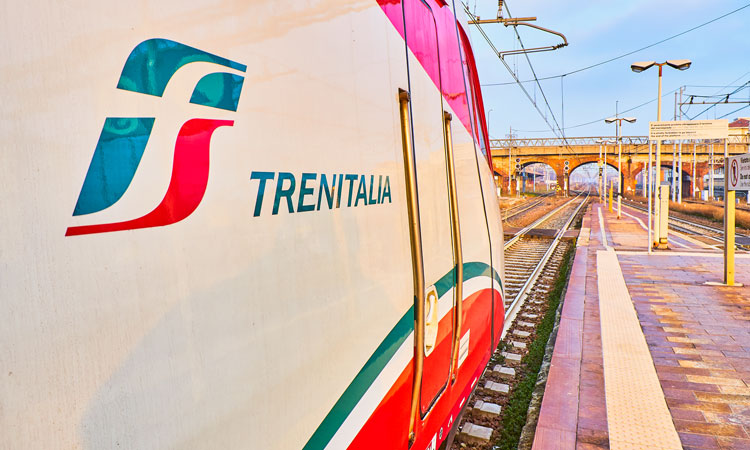
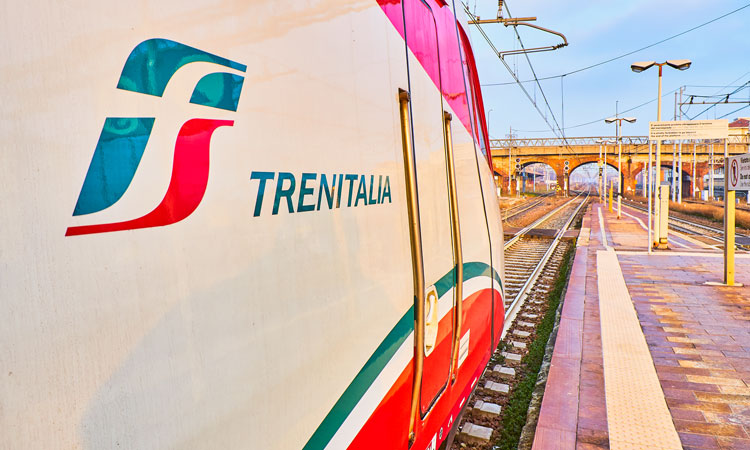
For Trenitalia, the procurement of spare parts amounts to €200 million a year, but the lack of availability of some components can halt regular train operations and cause significant financial damage. This might be the case for components of trains built more than 25 years ago, but which are still operating efficiently today.
In order to support business development, in 2010, Trenitalia merged parts of its Technical and Purchasing Departments to create an autonomous department committed to the logistics of spare parts and repairable components maintenance. The Logistics Department was established and oversaw 80 per cent of economic value of the spare parts business, managing a relatively low number of spare parts (approximately 10,000).
First steps
At the end of 2017, the main KPI of the spare parts service for rolling stock maintenance was 97 per cent; that is number of spare parts delivered on the amount of spare parts required from maintenance plants. Naturally, our focus centered on the missing three per cent as we strive to reach the top level of service.
We analysed the issues of unavailability and identified two main causes: spare parts not formerly required and spare parts already negotiated in framework contracts, but with suppliers who had unexpected problems of reliability. In one simple word: unpredictability.
Trenitalia soon realised the challenge created by the asymptote of needs satisfaction and, as a result, traditional strategies (increasing safety stocks, negotiating agreements with suppliers for shorter-term deliveries, etc.) failed to deliver results at reasonable costs. What we really needed was nearly impossible: framework contracts for spare parts before knowing their lack of availability. This was, surely, impossible to achieve without a time machine – or, impossible to achieve without Additive Manufacturing (AM).
We got in touch with Mobility goes Additive, an international network of companies, institutions and research institutes that pushes 3D printing applications for professional use in several sectors. After joining the network, along with other European railway companies, we founded a restricted group focused on railway applications. The cooperation resulted in the signing of a Memorandum of Understanding (MoU) in March 2019, during the AM forum in Berlin.
In the RAILiability group, major railway companies have teams dedicated to AM implementation. Some of them decided to develop in-house skills through the acquisition of printers, others decided to close partnerships with service providers to develop joint products suitable for railway application. In short, we learnt a lot from sharing expertise and experiences, and we thank our colleagues at Angel Trains (with DB-ESG), DB, ÖBB, SBB and SJ for the knowledge exchange we openly share. By joining forces, each company sped up the introduction of AM in its process.
The introduction of Additive Manufacturing
Trenitalia’s approach to introducing AM was to drive the process through its Logistics Department in close collaboration with our Engineering Department. We knew that our focus was the missing three per cent and we didn’t expect significant cost reduction or inventory turnover ratio improvement.
We started considering the full cost of purchasing. We began paying higher costs for spare parts in return for prompt availability for maintenance, taking into account the benefit of full availability of rolling stock as a saving directly achieved by purchasing with a short lead-time.
AM technology fits our aim exactly: just a few days for delivery, no problem for low volume production, suppliers keen on new technology and ready to solve obsolesce issues through reverse engineering.
We found many service providers were interested in extending their customer portfolio to the railway industry. Since the very beginning, the new AM technology hit against the strict safety regulations of the traditional rail industry: almost every supplier was able to produce everything, but not one of them could demonstrate compliance with any of our standard technical requirements. We decided then to split our full AM implementation focus: for non-safety items, we sped up towards first purchasing, while, secondly, delaying safety items and evaluating every single case with our Engineering Department.
We set milestones: we wanted to have the first printed parts in 2019 and be able to start solving problems in 2020. The ultimate goal is getting a full operating framework agreement by 2021.
We began by analysing our logistics data and grouping our non-safety items by consumption behaviour registered in the last 10 years: regular or not in terms of quantity and time. Then, we used a semantic software to group spare parts in terms of technology in order to exclude unprintable items, such as cables or lamps. From 50,000 possible items, we created a relatively restricted list of 1,000 spare parts which we typically required irregularly: our probable unforeseen unavailability.
Finally, we crossed the resulting list with our historical data of materials causing rolling stock unavailability and our buyers’ obsolescence issues and defined a really short list to submit to the market.
Current benefits and uses
We intended on purchasing the first spare part in 2019 and to start solving some of the unavailability issues in 2020. Right now, work on the Trenitalia AM train is currently on-time – in fact, a little bit in advance – since our first spare part is an electric motor shield for a D445 locomotive for which we couldn’t find any possible supplier before, thus effectively solving a problem of rolling stock availability.
The majority of Italy’s railway lines are electrified – more than 12,000km – while less than 5,000km are non-electrified lines. Over the last few decades, locomotive D445 has been in service on non‑electrified lines: the locomotive was produced in the early 1980s, and now is progressively substituted by new EMU trains purchased in recent years. A relatively small D445 fleet composed of 30 locomotives is currently in service and will be used until 2022, when it will be completely dismissed. Of course, volumes of spare parts for maintenance are not at all interesting for suppliers; nevertheless, the Logistics Department must keep the supply chain efficiently running.
The electric motor shield that has been produced using AM was formerly manufactured by a company no longer present on the market, and no other supplier was interested in starting up a new production for so few pieces. Thus, the Logistics Department decided to engage the Trenitalia engineering team to create a 3D model through a 3D scanner and in-house post‑processing. A prompt to use a 3D model has been ready to explore the market, and Trenitalia found many suppliers willing to print the spare part in just two pieces and with a lead time of only 10 days.
Intentions for the future
Since we established a relationship with different service providers, we are now ready to face any unpredictable issues which can be solved by AM technology. Our focus for 2020 will be the classification of a catalogue of possible printed parts and the definition of a framework agreement in order to avoid negotiation time and to exploit all AM technology short-lead time potential in 2021.
In the next few years, we expect that AM technology will mature towards standardisation in the rail industry and, at the same time, will be fully implemented within Trenitalia’s supply chain. Then, further steps in the introduction of AM within Trenitalia’s maintenance processes will hopefully lead to the direct installation of printers in workshops.