New developments in on-track machines for narrow gauge track
Posted: 25 July 2016 | | No comments yet
MATISA Matériel Industriel SA has unveiled its two latest on-track machines (OTM), demonstrating new opportunities for narrow gauge track maintenance.
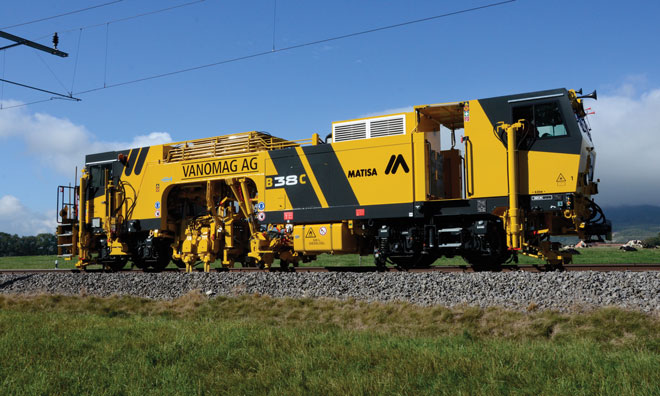
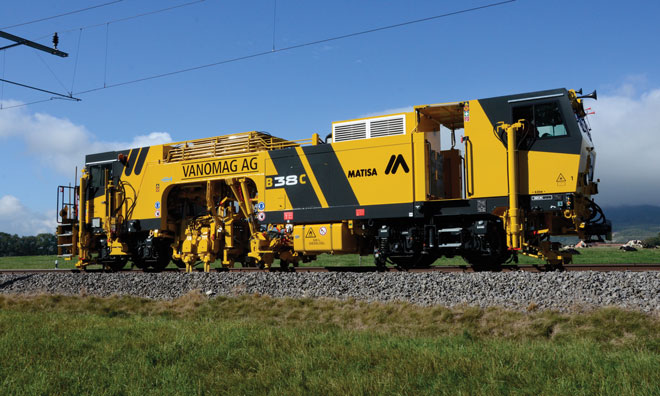
With experience in developing Swiss alpine railways for more than 100 years, engineers have built masterpieces that today, for some of the lines, belong on the UNESCO world heritage list. Some route sections, with radiuses of 45m (49.2 yd.) and gradients up to 70‰ (or over 100‰ rack gearing) combined with small clearance gauge and low axle load (160 kN), request high engineering skills and expertise. To meet these challenges MATISA has introduced two modern optimised machines to its narrow gauge fleet with the B 38 C Tamper and the R 20 RD Ballast Regulator with compaction units. Thanks to close cooperation with operators during the design and manufacturing stages, both machines are the product of extensive experience within the railway maintenance sector. In Switzerland the narrow gauge track is called the metre-gauge since it is exactly 1m from rail to rail.
B 38 C – the compact universal tamping machine
The B 38 C is a compact 4-axles tamping machine for plain line tracks and switches and crossings (S&C). As with their standard gauge sister fleet, they feature MATISA’s C-type tamping units which have proven themselves for their high quality tamping, durability and low maintenance costs. The tamping units are positioned to enable operation to up to four different gauges – in other words, tracks built on a mix of standard and narrow gauges. The four integrated lifting jacks enable the B 38 C to be raised and shifted sideways for an easy load onto a trailer (see Figure 2). The machine can then be easily moved to another location with narrow gauge tracks.
The B 38 C is equipped with the latest operating system from MATISA. The driver and tamping operator have all the important information displayed on the graphical human machine interface (HMI) which is always available at a glance.
Thanks to multitasking joysticks with ergonomic and tactile functions, the operator can keep focus on the track operation. During design and development of the control system, MATISA has enhanced the machine diagnosis feature, easing potential fault detection. This considerably shortens the potential immobilisation time.
The HMI is featured with touchscreen technology; the operator needs only two or three touches to obtain access to an element that is causing a disturbance. The element is then identified physically and tagged, locating the elements in the documentation (pneumatic, hydraulic, electronic, electric drawings, etc.). At this stage the operator can deal with the potential problem directly; contact their maintenance entity; or get in touch with MATISA’s technical and support centre. Our electronics are featured with a remote access device in which remote engineering staff can access all machine parameters and commands to fully understand and analyse situations. This feature significantly reduces intervention times and potential travel needs. In addition to this, with the full diagnosis of the machine being available to the remote engineer, the root cause of the problem can be narrowed down and repair procedures and potential spare parts identified. The maximisation of machine availability is then guaranteed.
Absolute measuring base with total station
The guiding and measuring system is based on a guiding computer CATT and the three reference points transmitted by MATISA’s unique NEMO optical measuring base. This measuring base has been specially developed for track radiuses of 40m (43.7 yd). The light source is a pulsed LED technology which ensures a reliable reading that is immune to external disturbances. MATISA’s newly developed MATS Absolut-measuring-base is now also available as an option. The total station (Trimble S8) first determines its absolute three dimensional position through fixed reference points (typically catenary poles). It then continuously measures the position of the active prisms located on the machine’s measuring trolley A. It regularly communicates via radio transmission to the MATISA CATT computer. The B 38 C Tamper knows its absolute position and processes the effective track guiding correction on each point, should any deviation occur. CATT also accepts different geometry data file formats, for example Toporail, Bentley, etc. Whilst the total station is able to deal with lengths of several hundred metres, it usually works on a 120m length with Toporail (131.2 yd). In order to optimise the sighting distance in curves, there are two mounting positions for the active prism on the trolley A; one placed to the right-hand side and the other on the left-hand side of the trolley and track axis.
The R 20 RD – a ballast regulator and compaction machine in one unit
A newly designed compaction unit and central pivoting plough are the main new developments of the R 20 RD that can be fitted within the wheelbase. This allows the machine to regulate and compact the ballast in one pass, despite its short wheelbase of only 5m (5.5 yd.).
The crib compaction frame is specifically shaped to enable simultaneous compaction of both sides of the rail. The specific design and assembly of these units allows a simultaneous two-sleeper compaction providing the appropriate output. MATISA’s state-of-the-art integration of the compaction device onto the machine frame in addition to the appropriate damping selection transfers the vibration energy to the ballast.
The side compaction units are laterally movable and have a split vibrating plate so that they can simultaneously compact the ballast next to the sleeper head and the ballast shoulder in order to maintain the appropriate ballast profile.
The outer blade of the centre plough is fitted with shields that can be hydraulically adjusted to recreate the appropriate ballast profile on the track and in the tightness of stations and their platforms. In the past this manipulation of the shield had to be executed manually.
For track maintenance work where there is ballast on the sleepers and near the rails, MATISA’s R 20 RD Ballast Regulator is equipped with a front plough that is designed to move the ballast and distribute it to one (or both) sides of the track. The system can auto-adjust to prevent potential derailment.
The ballast brush on the R 20 RD has also been adapted for the narrow gauge working environment. Located under the rear overhang, the brush housing is able to rotate in short track radiuses enabling appropriate transfer and loading onto the lateral conveyors.
Always striving to ease maintenance of its products, the MATISA lateral conveyors are designed to allow easy replacement using the same principle as a drawer. The brush axle can also be replaced laterally for easy maintenance.
A 500l water tank can also be added to provide water spraying. This efficient equipment holds down the dust in an economical way and increases operator’s safety.
Modern drive and braking system
These new machines for meter-gauge railways are featured with proven and reliable hydrostatic drive and brakes, working like a motor brake and allowing long brake solicitation, especially designed for long mountain slopes and steep tracks. This increases safety by significantly reducing the heat built up and the wear of brake blocks.
The approval authority imposes released spring loaded braking systems for the new narrow gauge machines. This system allows the hand-brake to be applied from the cab. In other words the driver does not need to leave the vehicle in order to secure it. Special air tanks ensure that whilst the machine is hauled, such as in train formation, the released spring loaded braking system will be out of function. For example, in the Rhätischen Bahn (Swiss Alps Railway company) the locomotives have only one vacuum-brake.
Similar to the standard gauges, the diesel engine works with low rate rpm to enable valuable energy savings, even in demanding operations. This reduces diesel consumption as a well as noise emissions. Mandatory for Switzerland, the diesel engine exhausts are featured with particle filters allowing safe tunnel work.
Conclusion
The MATISA B 38 C Tamper and R 20 RD Ballast Regulator are two small narrow gauge on-track machines, suitable for conducting complex properties of metre-gauge tracks. They are ergonomic and reliable, which allows operators to provide the best on-track maintenance quality. With ease-of-use, they also provide clever self-diagnoses and user-friendly tools. This leads to high availability and in turn improves the return on investment.