The Smart Freight Train
Posted: 26 May 2016 | | 8 comments
Consultants Rob van Looveren MSc and Peter van Kats MSc discuss the benefits of implementing the Smart Freight Train system, designed to inform train drivers on the technical condition of hauled wagons.
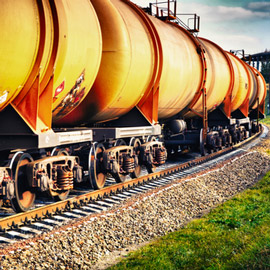
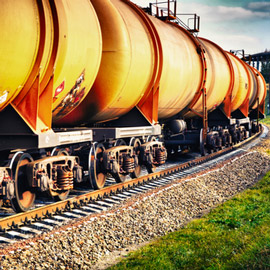
According the 4th Railway Package the transportation of goods via rail should become more reliable and attractive. Innovation is necessary for rail modality to gain a greater market share in the transportation of goods. Freight corridors will reduce transport times and ERTMS will facilitate seamless cross border traffic. The technology used for wagons is robust and demands human activities on yards. A train driver, responsible for the safe movement of his train, has little to no means for checking and supervising the technical condition of the wagons joined to his train consist. The Smart Freight Train system (SFT) will provide the train driver with a “rear view mirror” to observe his train and train reports are send to trackside concerning the health of wagons and the progress of the train in relation to the time schedule. An innovation that is a win-win situation for many parties.
Rail goods transportation in Europe
The European Committee decided to create a Single European Railway Area. Transportation should be seamless throughout Europe, especially in relation to international goods. The Railway Package goals are set to improve the reliability and attractiveness of rail transport – goods transport should shift from road to rail.
Transportation of goods via rail is sustainable and can be done at low costs. The maintenance of the railway network and rolling stock is a continuous process. Keeping tracks and trains in good condition is vital because derailments can easily turn into a disaster. The train driver is responsible for the safe movement of his train, but he is dependent on efficient and effective maintenance. This raises some questions. How will Railway Undertakings be convinced that all wagons are in good condition? Will the ECM (Entity in Charge of Maintenance) plan a visit to the workshop in time for their wagons?
Risks in freight train operations
Collisions between trains are usually related to traffic management. One-sided accidents with trains are track or train related. Thorough investigation into the causes of accidents has provided a lot of knowledge which is valuable when looking for remedies and solutions.
Freight trains are longer and heavier than passenger trains. Freight trains use pneumatic brake systems whilst passenger trains are equipped with electro-pneumatic disc brakes. The reaction time of the brakes on freight trains demands an appropriate brake procedure. A human error of the train driver can be seen as a safety risk. Other risks for the train driver are events on wagons which he cannot notice while moving his train; i.e. unreleased handbrakes, shut off of the brakes, hot box, un-roundness of wheels, loss of brake shoes, etc. Also, the derailment of a wheelset or bogie is hard to detect by the train driver and during marshalling and (un)coupling of wagons, human errors of yard personnel may lead to unexpected situations. For example, valves of the brake system not closed or open and handbrakes not set or not released.
Other risks are related with technical failures of the wagons and/or the tracks. This could include non-alignment of tracks running through a switch not properly locked. A hot box or sticking brake shoes are also causes for derailments. Other indirect causes are overloading, which might damage bearings, and insufficient maintenance.
The need for inspection of tracks and trains is evident. Freight trains can be monitored when passing wayside monitoring locations. There is however the uncertainty about “are technical faults detectible and did they arise” when passing the monitoring location. Instead of location dependent detection you should apply a continuous observation method to detect irregularities in time. Studies and investigation in the past did not result in an operational solution. This inspired us, and our belief is that we designed a system which is technical feasible at reasonable costs.
‘We designed a system which is technical feasible at reasonable costs’
Electronics on railway wagons
Passenger coaches need electricity for on-board lighting. A generator is driven by the axle of the wheel set. Batteries provide power supply when the train is halted. Freight wagons however are designed for the transport of goods. The wheel sets and the pneumatic brake system on each wagon are vital elements for a safe movement of the train. To monitor these elements while moving the train you need an on-board electronic system with sensors which also need electricity. This however gives quite a different challenge. What kind of power supply do you need? How do you switch on the system in time? Will the power supply on each wagon still hold energy after a standstill of a few weeks or months? We have gone through a variety of solutions and we had to reject a lot of them because they would soon fail in the operational rail environment. How to develop such a system? With “proof of concept” projects, we realised which choices we should make. From this we now know that the design of a system with low energy electronic components demands precise engineering.
The on-board solution
The measuring methods applied on-board a wagon will face challenges due to the harsh rail environment, i.e. all types of weather conditions and mechanical impacts. Electronic equipment is needed for measuring physical parameters. A vital element is the power supply. Will batteries meet the requirements? In order to create a solution with a long life cycle more expertise and creativity is required. As electrical engineers with a long working experience we were not afraid to take on the challenge.
The Intelligent Smart Freight Train concept
How do we implement all the required functions technically? More than 10 years ago a concept was created called the Intelligent Freight Train. The technology available at that time made the application very costly and power consumption was too high to realise an economic system. Nowadays a lot of low energy electronic components are available which make it feasible to create a self-providing energy supply system on each wagon with a long life cycle (> 10 years). The technical requirements are clear, but it is for certain that the system needs appropriate life pilot testing.
Continuous condition monitoring
The on-board system of the Smart Freight Train performs continuous monitoring while the train is moving. Irregularities are reported in real-time to the driver and reports are sent to trackside.
Before departure the train driver will make his train ready. Can he really check if all brakes function properly and no handbrakes are still set on? How can he verify that the train consist corresponds with the train documents? Once the on-board SFT system is activated and the brake test is performed, an automatic check will be made on the status of the brake system and the real train consist will be checked against the digital train documents.
After departure continuous monitoring will be performed on the function of brakes and smooth running of wheels and bearings. Irregularities will be reported to the train driver in real-time. The train driver will be able to slow down or stop his train in order to prevent a derailment. Condition reports are sent to trackside and can be used for predictive maintenance planning. The progress of the train against the time scheduled will also be reported. Within TAF (Telematic Applications for Freight), these real-time train reports can be used for further evaluation of the train movements on freight corridors. Another important issue is the monitoring of the Train Integrity which is a mandatory function for deployment of ERTMS Level 3.
The future change
In the world of railways, long existing working procedures are not easy to change and working methods across European countries have their own origin from the past. New technology creates the opportunity to make the step forward. With the introduction of the Smart Freight Train system the scene will change. Real-time information coming directly from the moving train will provide more accurate information to be used in the various trackside processes. We admit that all parties involved in freight train operations should be informed in an early phase about these innovations. Adopting changes takes time and therefore we take the chance to present our ideas.
SFT Associate Partners
We, a Dutch team of engineers, believe in this concept of the Smart Freight Train. Who will help us to make this become a reality?
Biography of Rob and Peter
![]() ![]() Rob van Looveren MSc – Consultant Telecom & Railway System |
![]() ![]() Peter van Kats MSc – Consultant Radio & Telecom System |
Rob and Peter both have a degree in electrical engineering from the Technical University of Delft and have a long working experience.
Rob started his career in automation as a systems analyst. He continued his career in telecommunications in various fields (technical planning, network planning, policy making, special projects and innovation). Now he is self-employed as a consultant for Telecom & Railway systems.
Peter started his career at the telecommunications laboratory for investigation of radio technology and was involved in setting up regulations for EMC on a European level. He continued his career in the management of public telecommunication networks and deployment of new technologies such as fibre cables and transmission technology. The next phase of his career involved working on projects for large data centres for worldwide area networks. Now he is self-employed as a consultant for Radio & Telecom systems.
Whilst the article and web information are very interesting, but some technical issues are no longer in use, at least in most of the USA and Europe. E.G. on passenger trains, the “hotel” electricity hardly ever comes from axle-driven generators any longer, but through the train-heating and lighting bus from the locomotive. Train condition monitoring is done at various points along the line with e.g. Wheel Impact Load Detectors, Hot Axle Box detectors etc. I wonder if all that kit is fitted to freight wagons, the condition of which is not very rarely compromised through lacking care with maintenance, are we not introducing a serious possibility for spurious alarms and lots of expensive delay? Parking brakes not released? A simple valve in the brake pipe, which opens when the parking brake is applied, stops a train from moving off and makes this known by hissing brake air escaping under the wagon. Simple things work and can be dealt with by local train staff rather than someone who has to come in from some far away office. I miss a bit of “the daily grind” reality check here..
Dear Peter,
Thank you for your response.
You are quite right about passenger trains being modernized. And I agree with your remark concerning maintenance of freight wagons. About the “the daily grind” reality I can tell you that the system will not cause an interruption of the train movement, because that will be left to the train driver. The train driver is the first to be warned about irregularities.
Hi Rob
I am an electronics engineer working as consultant with GAIAOSE the official keeper of rolling stock in Greece.
We are looking for solutions to problems like those mentioned in your Smart Freight Train analysis.
We would welcome all information regarding this issue as well as any opportunity to work on the subject offering any help we could possibly contribute.
Wishing you the best in this effort we remain at your disposal for any help we might contribute on this.
Best regards
Dear Dimitris,
You just made your comment while I was in Berlin at the Innotrans Messe. I am very busy to start up the project. I think we should continu our contact, because when I succeed you will become a future user of this system. Click on my name and you will be directed to my website where you already can find some information. After reading you should send me a message directly. And I suggest we have a telephone call and then I will answer your questions.
Best regards.
In Switzerland we selected another way to check freight trains. The control systems are part of the infrastructure as multiples train-monitoring installations :
http://www.sbb.ch/en/group/the-company/responsibility-society-environment/customers/sbb-and-safety/train-monitoring-installations.html
which cover most of the smart freight train device, except the EoT check (still secured by track side equipment). The measurements are only made at specific point but any irregularities sends an alarm which permits the train dispatcher to react: usually stop the train and contact the train driver.
If you want more information about this topic, let me know and I’ll put you in contact with the right person. There are also some presentation and information on Internet if you look for “zugkontrolleinrichtung SBB”.
Dear Mr. François Bianco,
Thank you for your comment. You give us a good insight on the very well organized trackside monitoring system in Switzerland. From a historical point of view the Infrastruture Manager takes the responsiblity to guarantee the safety on the tracks. With the introduction of ERTMS a shift is started to equip trains with intelligent systems on-board. The role of the Railway Undertaking is to guarantee the required condition of trains to move safely on the railway network. With the introduction of the Smart Freight Train system we want to equip freight trains with an intelligent transport system and provide RU’s means to take their responsibility.
Hi François, thank you for taking the time to comment, some useful insights.
@All, I hope you enjoy reading my article and get insight in freight train operations. Forward your questions (click on my name), because learning from others never ends. Thank you.