Optimising rail fasteners for noise and vibration performance
Posted: 18 November 2024 | Daniel Lurcock | No comments yet
Dr Daniel Lurcock, Principal Consulting Engineer at ISVR Consulting, explains how working alongside the ISVR (Institute of Sound & Vibration Research) academic department at the University of Southampton, they have been providing advice on noise and vibration solutions for the last 50 years.
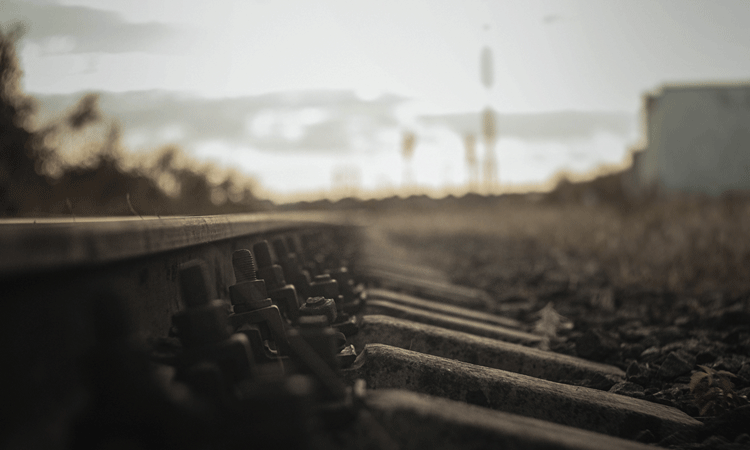
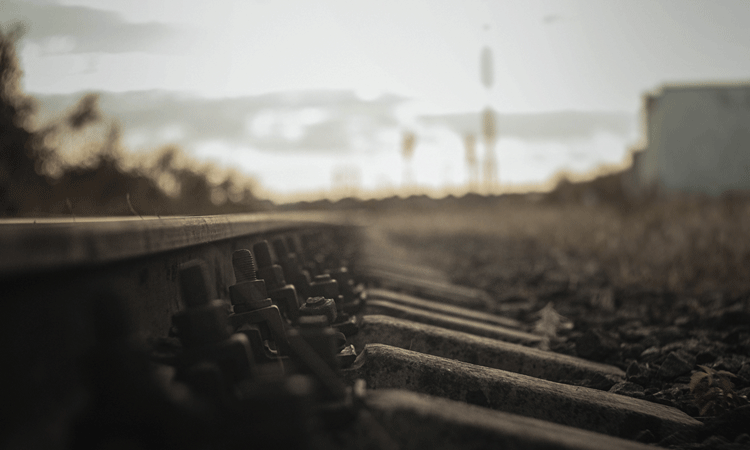
Over the last few decades, we have developed a particular specialism in railway noise and vibration applications, working with clients, and on research projects, to understand and solve rail-specific challenges.
Our work has included measurements to improve understanding on the factors affecting noise such as the surface unevenness (roughness) of the rails and wheels, and the dynamics of the track. We have worked in the development of mitigation solutions such as rail dampers that reduce noise radiated by the track. In our research into railway noise and vibration we also use measurements conducted from the comfort of our own acoustic laboratories and test track, often alongside advanced computer models.
Noise and vibration sources
Noise from a passing train is generated from several sources. These can include rolling noise radiated from the track and wheels, aerodynamic sources, propulsion components and ventilation plant. Each of these individual source types has its own ‘sound power’ characteristics which can depend on the track conditions and the operating conditions of the train.
For passing trains, in most situations it is the rolling noise that is the dominant noise source. This is generated where surface unevenness (roughness) on the surfaces of the wheel and rail generates forces that cause the track and the wheel to vibrate; these vibrations are in turn radiated as sound, which travels through the air to the ears of nearby residents as well as passengers inside trains.
Vibration also travels through the track structure and the ground. At nearby buildings, the vibration can also be ‘re-radiated’ as sound, resulting in occupants often being able to hear and even feel trains passing. This is referred to as ‘ground-borne’ noise and vibration.
Why is this a problem? Not only are noise levels an important contributor to passenger satisfaction, but for lineside residents the World Health Organisation has linked noise disturbance to negative health effects including heart conditions. Above any contractual or legal obligations that require railway operators to minimise these environmental emissions, quiet railways are good for the image of the industry, increasing confidence in the future of rail as an effective, reliable and sustainable mode of transportation.
Making the rail and wheels as smooth as possible is the single most effective method of reducing railway noise and vibration. However, since the rail and wheel conditions deteriorate over time, maintaining smooth rails and wheels require costly regular grinding with specialist equipment and expertise, which is often not feasible.
The role of rail fasteners
In addition to the effects of unevenness (roughness), the design of the track itself plays an important role in the level of noise and vibration that is generated by passing trains. Rails are connected to sleepers and track components via a railpad, which is an integral part of the rail fastener assembly. Railpads act as an isolator between the rail and the rest of the track primarily to reduce track structure damage and can be specified with different stiffnesses depending on operational requirements such as cornering behaviour.
The stiffness of the railpad affects the dynamic behaviour of the system, and therefore how much noise and vibration is generated.
Influence on noise and vibration
To illustrate this effect of railpad stiffness on railway noise and vibration, we have performed some calculations using industry-standard prediction tools developed within the ISVR:
- Train Noise Expert is a software tool that takes train and track parameters (along with sound emission parameters of other sources such as traction/equipment) to predict airborne noise levels at different train speeds (see trainnoiseexpert.com for more info)
- MOTIV is a vibration prediction tool that uses information about the train/track and the ground composition to predict ground-borne noise and vibration (see motivproject.co.uk/motiv-software for more info).
These models have been used to explore three indicative cases for a regional train running at 80km/h running on standard ballasted track with three levels of vertical railpad stiffness: high (800MN/m), medium (250MN/m) and very low (50MN/m). For the airborne noise predictions, we have assumed that the microphone is 7.5m from the centre of the track. For the ground-borne noise predictions, we have assumed that the train is running in a tunnel at a depth of ~30m and a building is about 8m from the tunnel centreline. Indicative results are shown in Table 1.
The predictions above reflect real-world experiences of engineers around the world; that the railpad stiffness plays an important role in railway noise and vibration emissions. When it comes to passenger and bystander noise levels, it is clear that opting for higher railpad stiffness is likely to be optimum. Meanwhile, the opposite is true when it comes to ground-borne noise – and in this particular case, use of rail fasteners with ‘very low’ stiffness show a good potential for use as a mitigation option.
Physical mechanisms
So, what is really going on? Why is there a trade-off between noise and vibration control?
When soft railpads are used, less vibration is transmitted from the rail to the rest of the track structure and ground. Consequently, this results in less ground-borne noise and vibration affecting nearby buildings. However, this comes at a price: the soft railpads allow a greater length of rail to vibrate, and radiate noise – leading to an increase in noise levels for passengers and bystanders.
Conversely, there is the opposite trade-off: stiffer railpads result in less of the rail vibrating (so less airborne noise generated) but more vibration transmitted to the ground.
The length of the rail allowed to vibrate by the track design is characterised by a metric referred to as ‘track decay rate’, which is a crucial consideration in making accurate railway noise predictions and can be measured on-site.
Whilst the above considers standard rail fastening systems with a single railpad, there are various types of systems available on the market, some with ‘dual-stages’ (with different pad stiffnesses above/below a metal intermediate plate) which can, in some cases, help provide an optimum balance between noise and vibration control.
Appropriate selection of rail fasteners should therefore consider the project’s sensitivity to airborne and/or ground-borne noise as part of the track design process.
Other unknowns
Control of noise and vibration is just one aspect of the track design process; where optimising for rail contact fatigue, lateral displacement, and of course cost, are also important considerations. Additional aspects that could potentially be influenced by the rail fastener design and that are receiving increased attention are curve squeal and rail corrugation.
Curve squeal tends to exhibit a tonal characteristic at exceedingly loud noise levels, often causing discomfort for passengers and bystanders. It occurs through complex dynamic interactions between the wheels and rails under certain conditions, of which track corner radius, train conditions and even environmental aspects have been observed to play a part, making its likelihood of occurring very difficult to predict.
The right approach to a quieter future
There is continued research going on in the field to better understand and predict railway noise and vibration, including curve squeal and corrugation growth. This is really important due to the significant costs and disruption required to mitigate noise and vibration problems. The work that ISVR Consulting are doing to support the rail industry includes engagement in this research, development of prediction tools, and working with system designers to select the optimum solutions, striking the best balance between noise and vibration mitigation, operational requirements and minimised future maintenance costs.
It is recommended that track designers engage with specialist acoustic engineers at early stages of their projects to help ensure that the risk of future costly noise and vibration problems is minimised.