Gaining traction on the route to decarbonization
Posted: 17 October 2023 | Edgar Keller | No comments yet
Low-carbon hydrogen offers an enticing prospect as the fuel for future low-emission traction. The challenge is that the supply chain is not yet ready to support the large-scale deployment needed to decarbonize rail transportation. Even so, there are interim decarbonization measures that operators can adopt using existing technology, as Edgar Keller, President of ABB’s Traction business, explains.
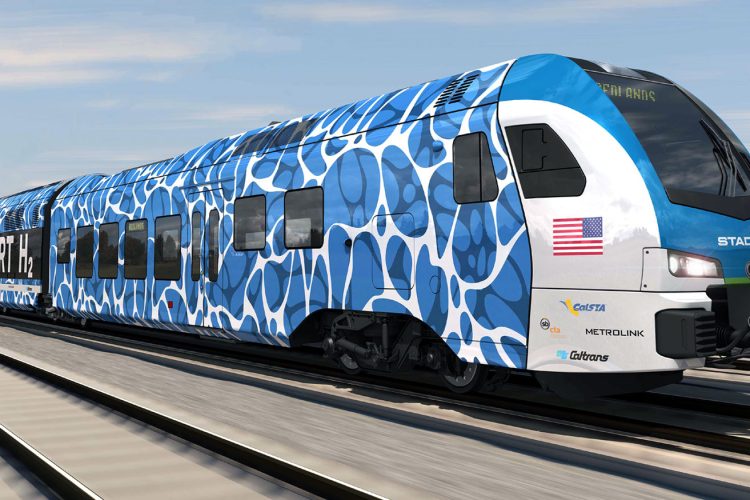
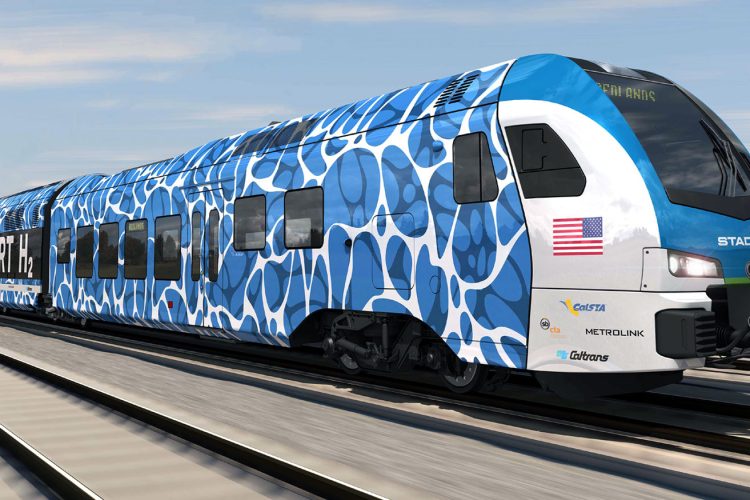
Rail transport is already more efficient for passenger and freight transport than road transportation. Despite being responsible for moving 7 percent of total goods and 9 percent of all passengers, railways consume only 3 percent of the world’s electricity supply. Yet, there remains a need for an increased commitment toward decarbonization.
Diesel-powered locomotives emit a significant portion of the rail industry’s emissions. The European Association of Rail Rolling Stock Lessors (EARRL) reports that more than half of the locomotives in the European Union, particularly those dedicated to freight transport, rely on diesel. This includes 2,850 on mainlines, 10,500 for shunting, and 950 passenger locomotives.
Replacing diesel traction is also complicated in regions where catenary supplies and third-rail power are not readily available to transition to electrified traction.
Hydrogen fuel cells can turn non-electrified railway lines into zero-emission lines, but despite substantial headway, the technology needs time to mature. However, our industry can’t afford to wait; we are in an urgent race to achieve Net Zero emissions.
Fortunately, there are readily available measures for reducing emissions. For example, energy storage system (ESS) technology based on lithium-ion batteries is well-developed and can significantly cut emissions when paired with diesel engines in a hybrid concept.
Another reason to invest in ESS technology is its sustained relevance, extending well into the hydrogen transition. This is because fuel cells need to work alongside batteries to deliver the required power profile for acceleration.
The environmental benefits and enhanced energy efficiency of train electrification are critical to achieving Net Zero. However, this process comes with financial complexities, requiring substantial investments in both infrastructure and equipment. While not hindered by technical challenges, the significant cost factor presents a formidable obstacle to achieving comprehensive electrification.
Improving traction converter efficiency
Operators can implement a series of actions today to improve the sustainability of their vehicles. A primary measure that stands out is increasing the traction converters’ efficiency in existing diesel and electric vehicles.
The most efficient, commercially available multi-level traction converters use high switching frequency, insulated-gate bipolar transistors (IGBTs), and best efficiency control (BEC). These advanced converters can reduce the energy consumption of a standard commuter train by up to 20 percent. Moreover, their reduced weight not only eases mechanical stress on critical components but also contributes to quieter train operations.
For example, as part of a comprehensive modernization program for the Swiss Federal Railways (SBB) rail fleet, ABB has retrofitted 119 locomotives with modern traction converters and control systems. The retrofit work includes replacing the older and less efficient GTO (gate turn-off thyristor) converters with more efficient and flexible IGBT converters. The improvements are expected to result in savings of approximately 27 GWh/year, equivalent to the energy consumption of 6,750 Swiss households.
These power-saving measures produce substantial reductions in energy and maintenance costs. The accrued financial savings will gradually offset the initial upgrade expenses, ultimately reducing the operating expenditure (OpEx) throughout the machinery’s operational lifespan.
Hybrid ESS drivetrain as a catalyst
Another effective way to cut diesel train emissions is to add an on-board ESS. An ESS can capture energy generated during braking and reuse it when the vehicle accelerates. The stored energy can also help to support auxiliary loads such as door opening and communications during station stops, eliminating the need to run the diesel engine. This not only decreases local noise but also reduces emissions.
Hybrid vehicles are able to use smaller diesel engines. This means the engine can run closer to its optimal efficiency point, further decreasing emissions. In such a scenario, the ESS acts as buffer storage for braking energy while providing peak power.
It’s worth noting that rail batteries differ from those used in road vehicles. They require high-power charging capabilities and must withstand frequent charging cycles while adhering to safety standards. Incorporating battery-based solutions into rail also contributes to greater operational flexibility and lower total cost of ownership (TCO).
Fortunately, advances in battery technology have ensured the availability of ESSs that meet these stringent criteria. These systems are compatible with both retrofits and new designs. A concrete example is provided by the Government of South Australia, which is retrofitting Adelaide Metro vehicles to become the country’s inaugural diesel-hybrid trains.
The 44 Class 3000 vehicles will use a lithium-ion-based ESS alongside their diesel engines. This transition, coupled with adopting a more efficient propulsion system, is expected to result in an approximately ~20 percent reduction in fuel consumption and a 35 percent reduction in CO2 emissions.
In certain applications, batteries can meet the entire power requirements of a train. For instance, several cities globally are already leveraging battery-powered trams. Full ESS-powered rail vehicles are likely to become more prevalent as battery technology advances.
Furthermore, hydrogen-powered systems will also benefit from the advances made by today’s ESS vehicles. They will use hydrogen fuel cells for electricity generation, with batteries serving as storage units to meet all dynamic requirements.
An example of this approach is Stadler Rail’s FLIRT H2, the first hydrogen-powered train in the United States with zero emissions. Due to enter service in 2024, the train comprises two cars, each equipped with six FCmove HD+ fuel cells, each delivering 100 kW. They transmit power to the drivetrain, where ABB provides a range of essential components, including the traction converter, a DC/DC converter, three Bordline® ESS 28 kWh battery packages, and a battery thermal management system.
The fuel cell-battery combination delivers enough energy for the train to cover over 286 miles (460 km) daily, while the entire traction system is engineered for an impressive 25,000 hours of operating life. The FLIRT H2 will operate on the Redlands Passenger Rail Project, covering nine-miles (14 km) from the San Bernardino Transit Center to the University of Redlands in Los Angeles’ eastern suburbs. Additionally, the train features a regenerative braking system, highlighting its eco-friendly design.
The Redlands Passenger Project marks a significant milestone in U.S. transit systems’ quest for more sustainable operations. Although the technology isn’t new, it positions San Bernadino’s transportation authority as a valuable resource for transit agencies seeking emissions-free propulsion options.
Overcoming the challenges
Operators face several challenges that require careful navigation. The development of charging infrastructure for ESS demands substantial investment and collaboration among various stakeholders. However, given the ongoing relevance of ESSs for hydrogen-powered vehicles, this investment holds significant promise for the future.
As with any emerging technology, stakeholders must focus on establishing safety standards, regulations, and industry-wide best practices. Globally, railways are dedicating efforts towards these aspects to ensure the seamless integration and operational efficacy of these technologies in the times ahead.
Furthermore, there is a pressing need for additional training to ensure that railway personnel possess the necessary skills for the secure operation and maintenance of these new systems. This evolving role will increasingly involve using sensors connected to the equipment to detect components at risk of failure, thereby notifying operators to take predictive maintenance actions.
The promise of hydrogen
It’s essential to understand why hydrogen technology is considered the future of sustainable rail transport and why it is not yet available on a large scale. Hydrogen fuel cells efficiently produce electricity, emitting only water vapor, which underpins their appeal.
Hydrogen can be manufactured through the process of electrolysis, powered by renewable energy sources such as wind and solar. This “green hydrogen” is characterized by an absence of carbon emissions, making it an environmentally sustainable power source. The advances in fuel cell technology are also progressing rapidly, as shown by the introduction of the world’s first hydrogen-powered passenger trains in Germany in 2022.
However, the supply chain for large-scale green hydrogen production, storage, transportation, and vehicle refuelling is still evolving. Simultaneously, fuel cell technology, mass production, and comprehensive service support require a maturation period. Experts suggest that it could take a decade or even longer for hydrogen to be fully prepared to replace diesel in rail applications, even though the first vehicles are already operational.
Transitioning from diesel to hydrogen
While hydrogen-based traction technology and its corresponding supply chains continue to develop, operators have a variety of choices to reduce the emissions associated with carbon-intensive diesel trains. By optimizing traction converters and transitioning to hybrid drivetrains, railways can efficiently reduce their emissions now, paving the way for a zero-emission future with the evolution of hydrogen technology.