Muirhead’s state-of-the-art seating calorimeter offers turnkey testing
Posted: 16 May 2022 | Khalil Safadi, Muirhead | No comments yet
Khalil Safadi, Laboratory Manager at Muirhead, explains the importance of the company’s new in-house Fire Resistance Lab for the global rail sector.
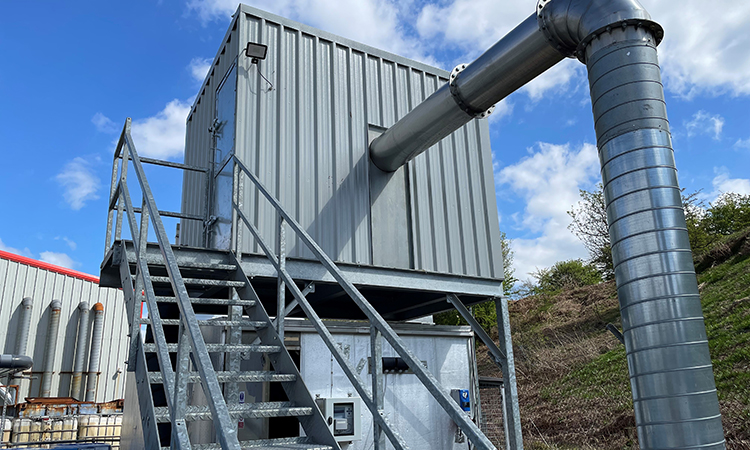
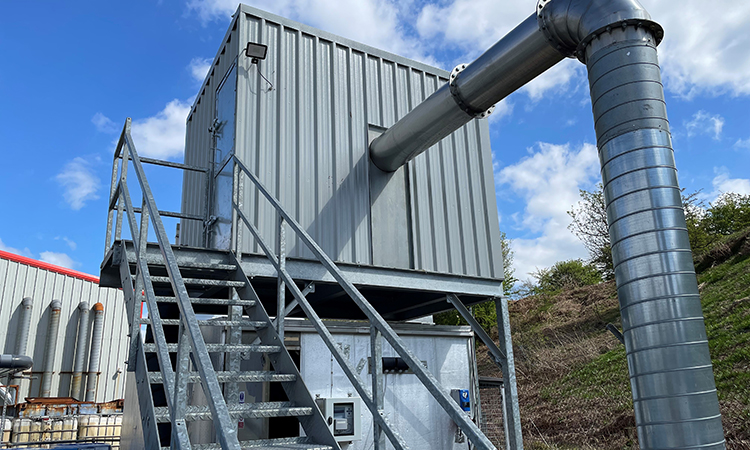
The thermal energy plant area of the Fire Resistance Lab.
Why is the new in-house Fire Resistance Lab important for the company?
Muirhead’s state-of-the-art Fire Resistance Lab has been in the pipeline since 2018. While many companies put investments on hold during the pandemic, our directors chose to continue developing the test facility because it will have such a fundamental impact on how we can develop new products for the rail sector in the years ahead.
This new £250,000 facility, coupled with the recent launch of our ‘Cut and Sew’ seat cover service and manufacturing plant in Scotland and China, will give us the opportunity to support rail sector customers beyond simply being a leather supplier. We want to work with the entire supply chain to support our customers from concept to delivery, and for all parties involved to b.e able to proceed together with total performance and regulatory confidence in our leather and seating products.
This new £250,000 facility, coupled with the recent launch of our ‘Cut and Sew’ seat cover service and manufacturing plant in Scotland and China, will give us the opportunity to support rail sector customers beyond simply being a leather supplier.
The technology in the lab allows us to test and validate new innovations and developments prior to market release, enabling us to greatly reduce development time due to controlling all product safety testing here on site.
To give that statement some ‘real-world’ context, we currently use external testing companies for large-scale heat release tests. This involves sending samples off-site to a company that has a public transport passenger seating calorimeter, which means fire resistance testing can take anywhere from six to eight weeks to turnaround.
Access to our own on-site public transport passenger seating calorimeter now means we can set up and conduct testing on new leather products at a moment’s notice and, most importantly, we will have results back with our product development team within a single shift. The turnaround time for new product fire resistance testing will realistically fall from as much as two months to as little as four hours.
This type of investment and innovation really allows us to push the limits in new product development and further cement Muirhead’s position as the experts in fire retardant leather.
What are some of the features of the new facility?
The installation of this large-scale heat release apparatus compliments Muirhead’s existing on-site bench testing capabilities, such as our cone calorimeter and smoke density chamber. The new facility takes our testing capability to whole new, and much larger, level.
Essentially, the new facility is a large self-contained stainless-steel box, but it is the specialist technology inside which makes this a very rare facility, and not just in Scotland.
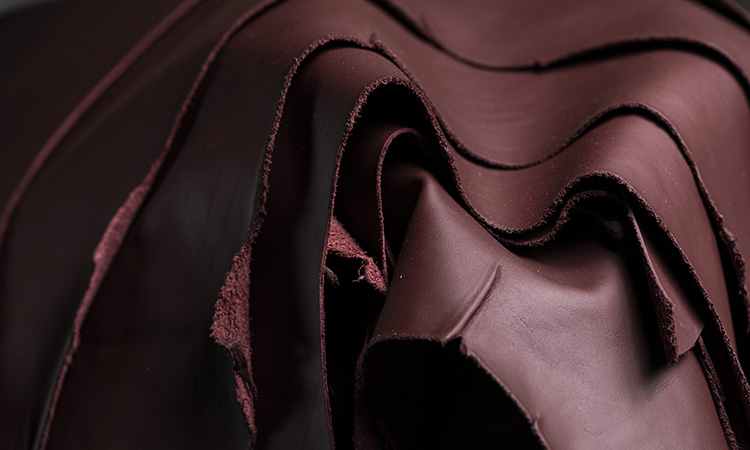
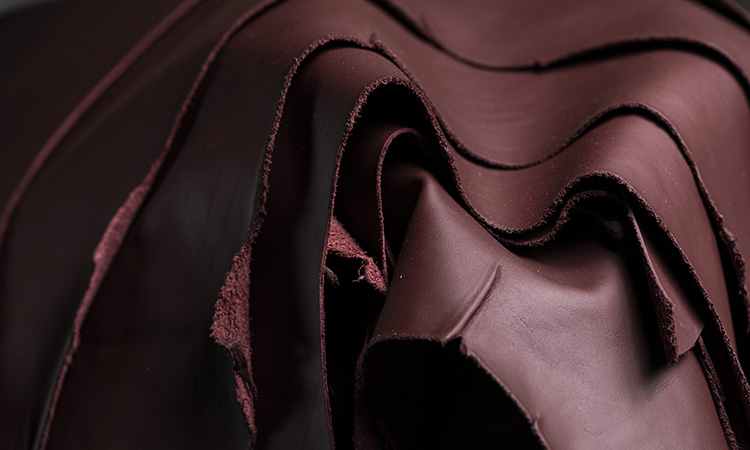
Muirhead’s on-site public transport passenger seating calorimeter means the company can set up and conduct testing on new leather products at a moment’s notice.
Internally, the facility has two distinct areas: a large burn area and a measurement and analysis area. The burn area is spacious and designed to allow for the mock-up of full train seat configurations, which our technicians can then ignite by re-creating genuine ignition scenarios such as lit cigarettes, matches, gas and so on. Any heat, flames, fumes, and hazardous gasses are extracted from the burn area by a huge overhead local exhaust ventilation (LEV) hood, which decelerates the gasses so the sensitive measuring equipment can assess every element produced during the burn as it heads out of the exhaust flume. That data is then sent to the testing area within the facility for analysis by lab technicians, who will record and store all the data, allowing us to factor in important learnings along the way.
The brain of the facility is the Servomex SERVOPRO MultiExact 4100 multi-gas analyser, which uses paramagnetic, GFx infrared, SBSW infrared, zirconia and aluminium oxide sensing technologies to provide highly accurate gas stream measurements. The MultiExact 4100 is designed to provide up to four simultaneous gas stream measurements including oxygen, carbon dioxide, carbon monoxide, nitrous oxide, methane, and moisture.
The lab also incorporates sophisticated temperature and humidity control systems, so that we can regulate and re-create numerous climate and environmental conditions to ensure our fire resistance tests are carried out as accurately as possible. We supply leather to customers who operate vehicles in many different climates, so it’s essential that we know how our leather will react to flame in any given atmospheric condition.
How important is it to now be able to test seat constructions to the EN45545 standard?
Being able to test all our high-quality leathers to EN45545 standard is paramount, not only to us, but to the many rail and mass transit organisations to whom we supply leather and our ‘Cut and Sew’ seat coverings. It is even more important to the millions of passengers who travel on public transport during any typical year.
Being able to test all our high-quality leathers to EN45545 standard is paramount, not only to us, but to the many rail and passenger transport organisations to whom we supply leather and our ‘Cut and Sew’ seat coverings.
There are always potentially dangerous elements created when you burn something. It’s not simply the visible flame that can do damage. There is the intensity of the heat, the density of the smoke, the chemical contents of the smoke, all important elements that we need to recognise, measure, and mitigate against.
In rail and passenger transport, you are often dealing with hundreds of souls in a single vehicle, and in the unfortunate event of an accident, or an instance of vandalism, we need to know that anything that we were responsible for in that vehicle – be that the leather, the cushions, the scrims and so on, is safe – and exactly what it would take to set it alight.
Essentially, we are measuring and prolonging the escape time from the vehicle. If something happened to a rail carriage, we need to know the contents of that vehicle are as low combustion as possible. And, if the leather is going to combust, we need to know that the chemicals coming from the smoke are not a risk to life. Operating to EN45545 standard gives us, our clients, and their passengers the reassurance that their safety has been carefully considered.
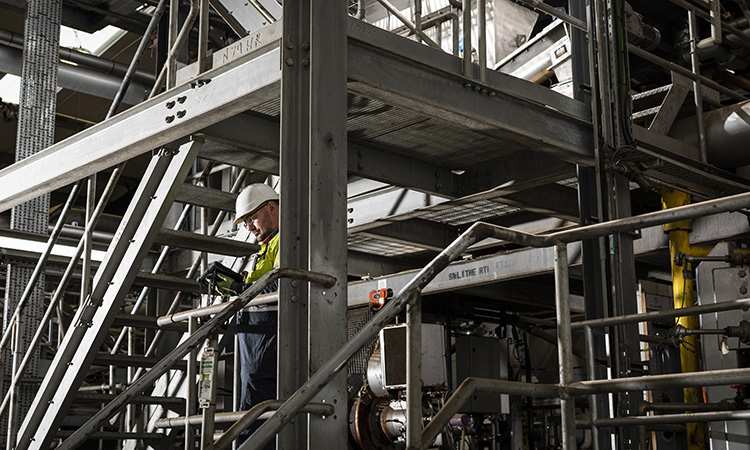
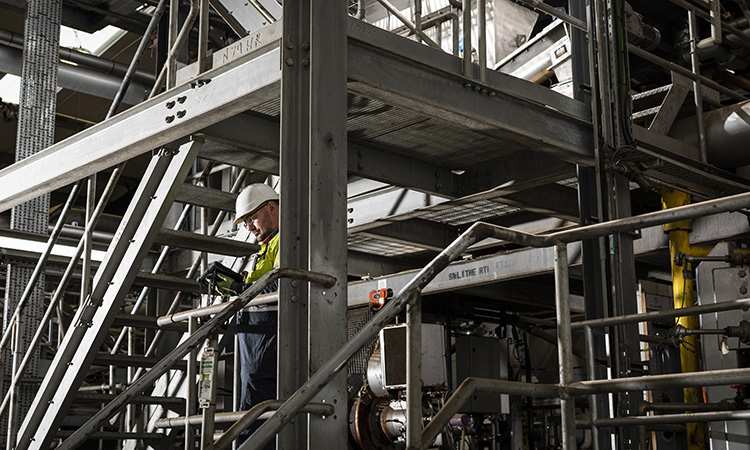
The thermal energy plant area of the Fire Resistance Lab.
Leather, in many ways, is the perfect and natural material to use in rail seat coverings due to its inherent fire-retardant properties. Additional treatments we have developed can further increase that flame retardancy, make it incredibly durable and, since the introduction of Muirhead’s ActiveHygiene Leather, also improve its biological performance.
In what ways will this new facility help support your sustainability goals?
As the manufacturer of the world’s lowest carbon leather for the passenger transport industry, sustainability and doing what is best for the natural environment has always driven what we do here at Muirhead. We circularised our manufacturing, source locally from responsible farms, own our energy efficient tannery, reclaim energy from process waste and end-of-life leather. We source natural, clean, local water from our own loch and our ultrafiltration plant enables us to recycle it.
As the manufacturer of the world’s lowest carbon leather for the passenger transport industry, sustainability and doing what is best for the natural environment has always driven what we do…
It is our intention that by having access to this new fire resistance testing facility, we will, in the months and years ahead, help build the confidence of the rail and mass transit sectors to specify natural and sustainable leather for their seat coverings, head rests and all associated internal soft furnishings.
Every single hide that we use to create our high-quality luxury leather is a by-product of the food industry, and if these hides are not given a second lease of life by being tanned and transformed into leather then they go directly to landfill, which is never a good outcome for the environment.
Looking to the future, access to this unique testing facility will also enable our innovative product development team to accelerate the rate at which they can develop, test, and bring new, innovative, and sustainable products to market.
Muirhead developed the world’s first lightweight full substance leather that helps to save weight for electric vehicles, without compromising durability.
Our ActiveHygiene leather with ViralOff technology was developed specifically for the passenger transport industry. This new self-disinfecting product works continually to reduce viruses.
Again, the impact of this is that we can better meet the needs of our rail sector clients and deliver the most sustainable products possible that also supports their environmental goals and commitments.
How do you see this new facility impacting the future of the company?
This new testing facility is just part, albeit a very important part, of Muirhead’s long-term strategic vision to be the only high technical performance leather manufacturer able to provide a complete end-to-end turnkey solution to the global rail market.
That is a very important objective for us as we believe that having full vertical control, including the in-house ability to fully test every element of our products in real world set-ups and scenarios, will help us to build our presence and reputation in the rail market in the years ahead.
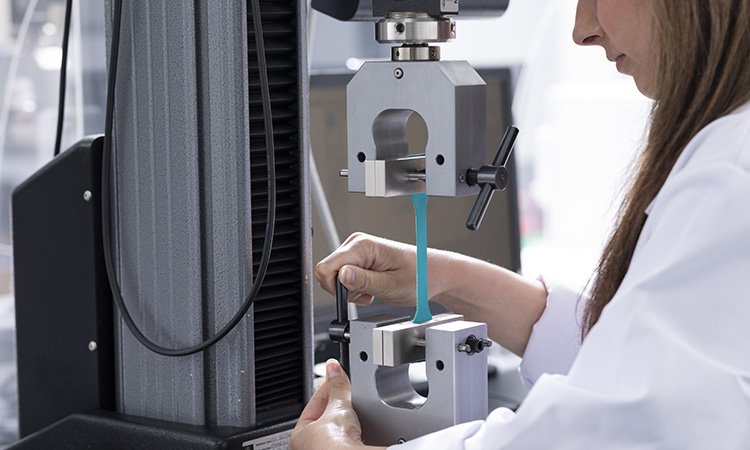
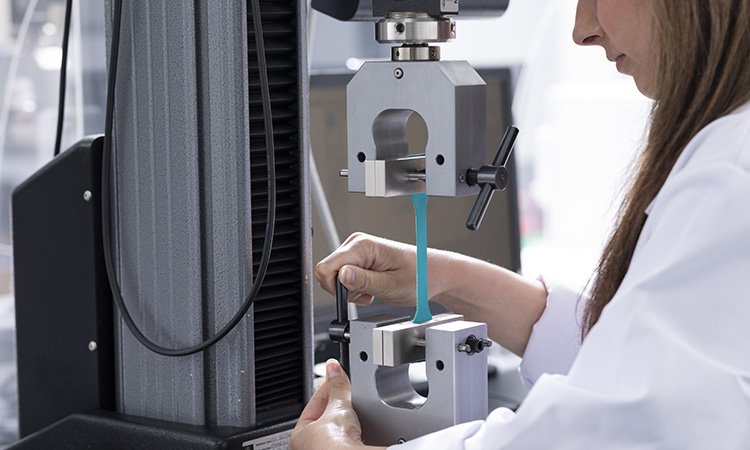
The new testing facility is part of Muirhead’s long-term strategic vision to be the only high technical performance leather manufacturer able to provide a complete end-to-end turnkey solution.
The rail sector has been particularly challenged in recent years with upgrading carriage interiors and incorporating economically viable ways of making the rail travel experience a more pleasant one for all travellers. We fully believe that by looking to leather for their seating and soft furnishing choices rail companies can add a more luxurious and comfortable feel to their carriages that deliver incredible long-term performance and durability, coupled with improved hygiene benefits and low maintenance requirements.
This new testing facility is just part, albeit a very important part, of Muirhead’s long-term strategic vision to be the only high technical performance leather manufacturer able to provide a complete end-to-end turnkey solution to the global rail market.
We have made many improvements over many years to our hide sourcing, tanning, testing, and finishing processes to ensure that the leather products we manufacture today are the highest and most consistent quality they can possibly be.
The new Fire Resistance Lab now means that our capability to test new products in record-quick time will increase Muirhead’s ability to better meet the demands of the ever-changing and dynamic rail sector, while greatly accelerating the rate at which we can innovate in the market.
We support the seat makers to offer operating companies full leather seat solutions. We will also be working with foam and fire barrier suppliers to find the correct combinations to meet the rail standards in the UK, EU and globally.
Our continued investment in new facilities and processes can only help us to build new relationships across the rail industry and further support our global position as the pre-eminent leather supplier to ambitious rail and rolling stock companies.
Related topics
Passenger Experience/Satisfaction, Rolling Stock Components (Interior/Exterior), Sustainability/Decarbonisation