Elcowire Rail: Let us make you ready for your project with the most sustainable solution!
Posted: 27 August 2021 | Elcowire Rail, Johannes Kaltenbach | No comments yet
Why are overhead contact line systems necessary? What are the requirements on the conductors? What about LCC and sustainability? Johannes Kaltenbach, Application Engineer at Elcowire Rail answers these, and other questions, here.
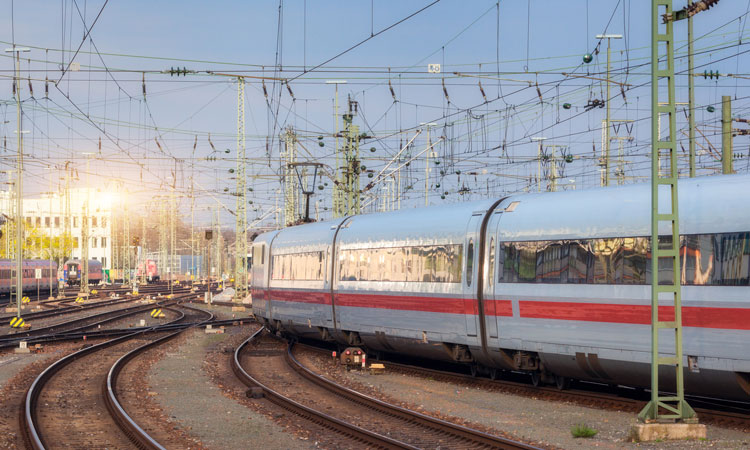
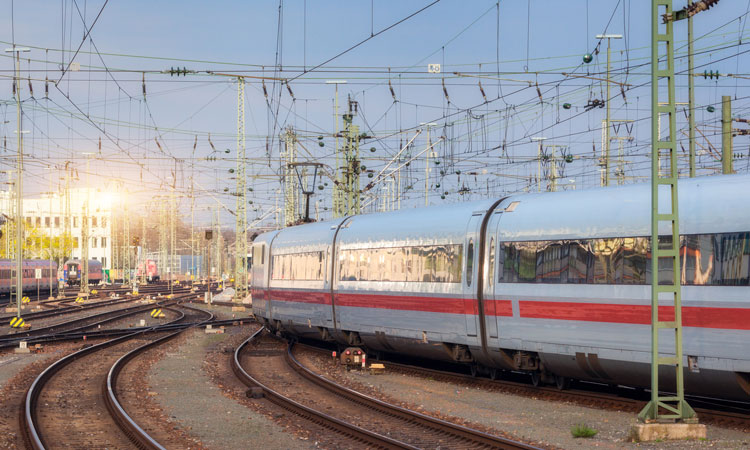

Accelerate your journey for lower CO2
Conductors and wires for overhead contact lines with satisfied customers all over the world
Elcowire takes customer satisfaction very seriously. It’s a key factor in how we measure performance as a supplier giving us a powerful tool in our development of long-term sustainable customer relationships. It was therefore all the more meaningful when we received a very high rating in our Customer Satisfaction Survey.
We would here like to share some common questions with you, and if you have any further questions we are always at your service and happy to support you with your specific targets.
Five questions and answers:
Why are overhead contact line systems necessary?
Efficient overhead contact line systems are the base for electrically powered rail traffic, which is more sustainable than diesel powered rail traffic.
Renewable energy sources can substitute fossil fuels in any power grid of railway operators. Therefore, the ecological footprint of electric traction is considerably lower than that of diesel traction.
What are the requirements on the conductors?
The conductors must carry the electric load as well as mechanical load. High life time of these components is essential for overhead contact lines with a design of 50 to 100 years.
There are pure copper products and alloyed products. What are the differences?
Whilst conductors made of pure copper feature best electrical properties, the mechanical and thermal characteristics of pure copper are suboptimal. A pure copper wire can only be operated at a lower continuous temperature than a low alloyed copper wire. Copper can only be tensioned with lower forces than an alloyed wire. Copper also has a higher wearing rate. Alloying metals will enhance the mechanical properties of the copper wire but often decrease the electric conductivity. The aim for us was to develop an alloy that offers same or better properties than copper.
After various tests we have developed our own VALTHERMO alloy, an alloy with same electrical characteristics as copper. Thermal and mechanical features of the VALTHERMO alloy exceed those of pure copper by far and equal those of copper-silver-alloys (CuAg) at least.
In contrast to CuAg products, VALTHERMO is independent of the silver price on the metal exchanges and has lower wear rates than CuAg when used for contact wires. By making both contact wires and stranded conductors from VALTHERMO, we can offer our customers a uniform system, which means that catenary wire and contact wire have the same properties.
How are properties such as creeping behaviour, wear and thermal resistance?
Catenary and contact wires are produced from copper or a copper alloy and expand or contract, depending on the temperature. To compensate that change in length, the conductors are tensioned. Under tension the conductors expand elastically immediately and by the so called creep strain additionally slowly. This creep strain expansion varies from alloy to alloy. VALTHERMO products offer, compared to pure copper, reduced creeping ratios by a factor of 2 to 3. The improvement in the creeping behaviour means that the readjustment work needed for pure copper wires after installation can be completely omitted when using VALTHERMO products. The reduced wear of the VALTHERMO contact wire leads to a longer durability.
At Deutsche Bahn (DB), the aim is a service life of up to 100 years for the entire overhead line. A pure copper contact wire must be renewed several times during this period, whilst the VALTHERMO contact wire is expected to last up to the whole lifetime of the overhead line which offers both economic and ecological advantages. Pure copper products are limited in operation temperature of 80°C compared to VALTHERMO, which can be operated at a maximum permanent temperature of 100°C. Therefore, VALTHERMO products provide higher ampacity.
What about LCC and sustainability?
The total costs of a catenary system do consist of the purchase price of the components and their installation cost. The production cost of an alloyed product for catenary systems is higher than the production of a pure copper product. Installation effort and therefore the costs are equal. When it comes to maintenance, however, alloyed products like VALTHERMO and VALCOND conductors offer advantages. Further significant savings result from the elimination of the need to renew contact wires. Whilst in operation, savings in energy losses contribute additionally. All in all, an overhead catenary system made of VALTHERMO and VALCOND products offer significantly less costs over the intended life cycle compared to a system made of pure copper. Estimation regarding CO2 savings have been carried out proving that VALTHERMO products are enablers to save large amounts of CO2 emissions. In summary, rail electrification can be made significantly more sustainable by using VALTHERMO and VALCOND products compared to conventional material.
Selected application references from our portfolio
For more information, please contact Johannes Kaltenbach via email or mobile +49 (0) 1761 8508 205.